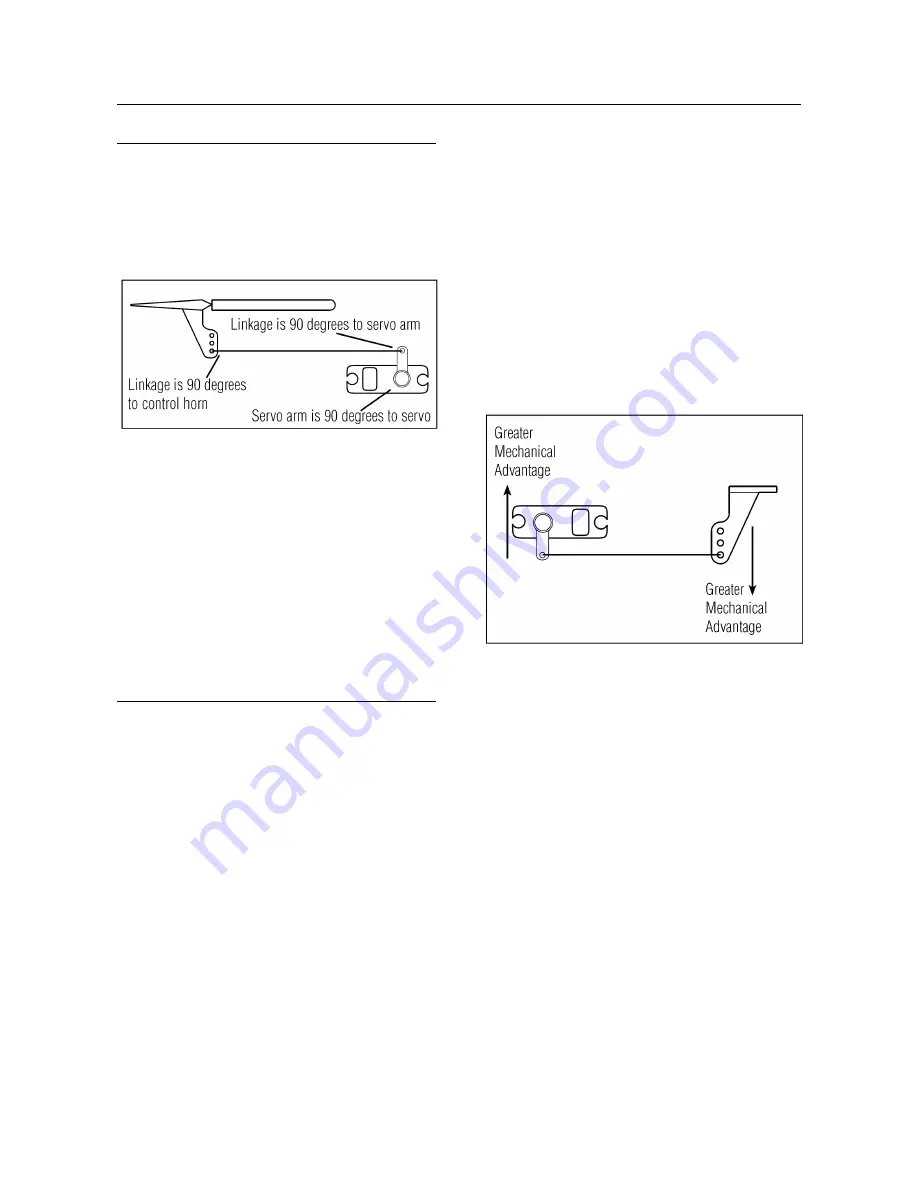
29
General Section
Sub Trim Usage and Mechanical Advantage
Sub Trim
Sub Trims are intended for relatively minor adjustments
to servo linkages and not for major trim adjustments to
the aircraft. Using excessive sub trim percentages can
cause a loss in servo resolution, where the servo
reaches its travel limit and stops moving before the
control stick is fully deflected.
The diagram below illustrates an ideal servo/linkage
setup when the servo is at neutral (no sub trim and
digital trims centered). Notice that the servo arm is
positioned at 90˚ or perpendicular to the servo. Also
note that the linkage or rod is attached at 90˚ to both
the servo arm and the control surface horn. This setup
will result in the same amount of throw in both
directions (0 differential throw). If the servo cannot be
mounted parallel to the linkage/rod then just make sure
the servo arm is at 90˚ to the control rod when the
servo is at neutral.
Mechanical Advantage
Mechanical Advantage is a very important concept
when dealing with larger aircraft. It refers to the
leverage that the servo can exert on the control surface.
Since the control surfaces are rather large, it is
important for the servo to have enough mechanical
advantage or leverage to control them, regardless of
the servo’s rated torque. A large amount of torque is of
little value if there is not enough leverage to use it.
Insufficient leverage can lead to control surface flutter
(usually a catastrophic event) and blow-back, where the
air flow pushes the control surface backwards resulting
in mushy or no control at higher speeds.
There are two ways to increase the mechanical
advantage of the servo. One is to make sure that the
control horn device, whether it be a horn as shown in
the illustration above or a bolt with a Rocket City-type
fastener, is long enough. The horn is the lever that the
servo uses to control the surface. The longer the horn,
the more leverage the servo has. It’s like a Lug Wrench
– when you can’t get a lug nut loose you put a piece of
pipe over the end of the lug wrench to extend the
handle and that gives you more leverage to break the
lug nut free. It’s the same thing—the lug nut is the
control surface and you are the servo trying to move it.
As a general rule-of-thumb, try to attach the linkage at
the control surface so that it is at least 1” away from the
surface – longer is better.
The second way to increase the mechanical advantage
for the servo is to attach the linkage at the servo arm as
far inward (towards the servo arm retaining screw) as
possible while still providing enough throw. It’s the
“lever thing” again, but in reverse, as we are taking
leverage away from the control surface by providing it
with a shorter lever to work against the servo.
Ensure that the attach point is the same distance from
the hinge line for like surfaces (two Ailerons, two
Elevators and two Rudder horns). If the attach points
are not the same distance from the hinge line there will
be unequal throw and it will be more difficult to
synchronize the surfaces for equal deflection. This is
especially critical for the Rudder where two servos are
attached to the same surface – unequal throw will
cause the servos to fight one another causing
excessive battery drain, and in severe cases may
cause servo damage.
Always try to use the maximum amount of Travel
(100%) that the radio provides. If it is too much travel,
don’t reduce the percentage of travel in the radio.
Instead, move the linkage further away from the hinge
line at the control surface and/or move the linkage
inward on the servo arm or use a shorter arm. If you
use high percentages of travel, you maintain resolution
(fine movements of the stick result in fine positive
movements of the control surface). When we decrease
travel percentages, we lose resolution.