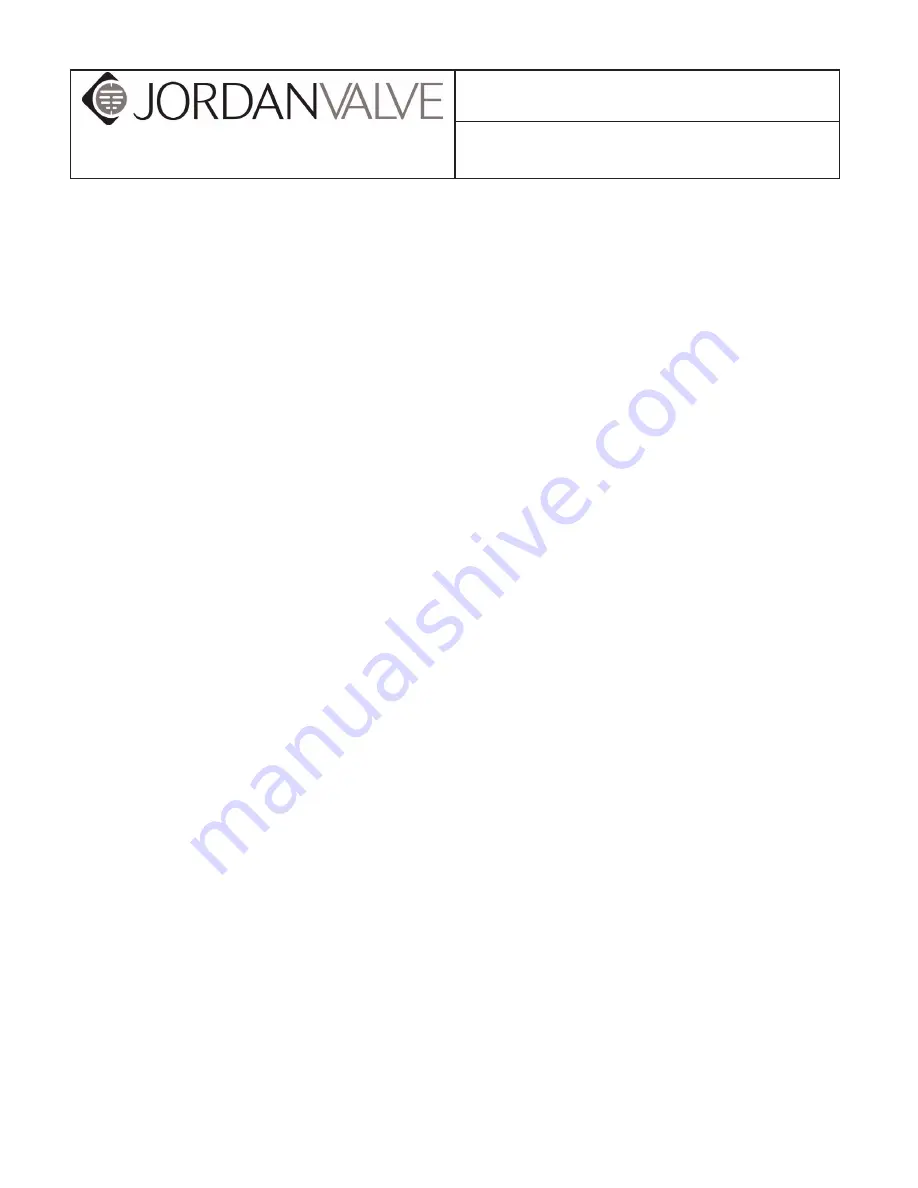
I
nstallatIon
Exceeding the recommended pressure and tempera-
ture limits indicated on the nameplates of your Jordan
valve control valve, can result in personal injury and
property damage. Jordan Valve recommends the
installation of a relief valve to protect against overpres-
sure situations.
The Mark EW Series valve bodies are designed to
meet specific conditions for fluid control, temperature,
pressure and pressure drop. The limiting factor on
these valves can be the body/trim material combina-
tions. Do not install these valves in any other applica-
tions without first consulting with your Jordan Valve
representative.
During installation, Jordan Valve recommends the use
of a sling to protect the painted surfaces of the valve.
Position the sling to avoid damage to tubing and ac-
cessories.
1.
Inspect the valves for shipping damage and
foreign debris while uncrating.
2.
Ensure the pipeline is free of welding slag,
chips and other debris by blowing out the line
before installation.
3.
Position the valve so the arrow on the valve
body is in the same direction as the pipeline
flow.
4.
Specific orientation of the control valve as-
sembly is flexible, unless limited by the
seismic criteria. Normal positioning
is with the actuator vertical above the valve
body. Should a different position be required,
be aware that the result may be uneven valve
plug and cage wear, and inefficient opera-
tion of the control valve system. Also,
be aware that the actuator may need addi-
tional support. Consult Jordan Valve for further
information on orientation.
5.
Always employ proper piping and welding
practices when installing the valve in the line.
If welding is required, internal elastomeric
parts may remain in place. If the valve
has buttwelding ends and composition
trim, remove the composition trim prior
to welding into the line.
6.
For flanged bodies, install an appropriate gas
ket between the pipeline and valve body flang
es.
7.
With leak-off bonnet construction, remove the
pipe plugs (Figure 1, Keys 14 and 23)
to connect the leak-off piping. To avoid an
interruption of service during inspection or
maintenance, install a three-valve bypass
around the control valve assembly.
8.
Most Jordan valves are shipped with
the actuator already installed according to
customer specifications. If your actuator has
been shipped separately, refer to the appropri-
ate mounting instructions in the actuator
manual.
I
ntroductIon
Contained in this manual are installation instructions,
maintenance procedures and parts information for the
Mark EW Series Valve Body designs EWD, EWS and
EWT. Refer to the appropriate manuals for instructions
for the accompanying actuator and additional acces-
sories.
Trained or experienced personnel should carry out
operation and installation of all pressure equipment.
If you have any questions regarding the equipment,
contact your Jordan Valve representative.
3170 Wasson Road • Cincinnati, OH 45209
Phone 513.533.5600 • Fax 513.871.0105 (f)
[email protected] • www.jordanvalve.com
I & M Mark EW Series
Installation & Maintenance Instructions for the
Mark EW Series Globe Style Control Valve
Warning:
Jordan Valve Control Valves must only be used, installed and repaired in accordance with these Installa-
tion & Maintenance Instructions. Observe all applicable public and company codes and regulations. In the event
of leakage or other malfunction, call a qualified service person; continued operation may cause system failure or
a general hazard. Before servicing any valve, disconnect, shut off, or bypass all pressurized fluid. Before disassem-
bling a valve, be sure to release all spring tension.