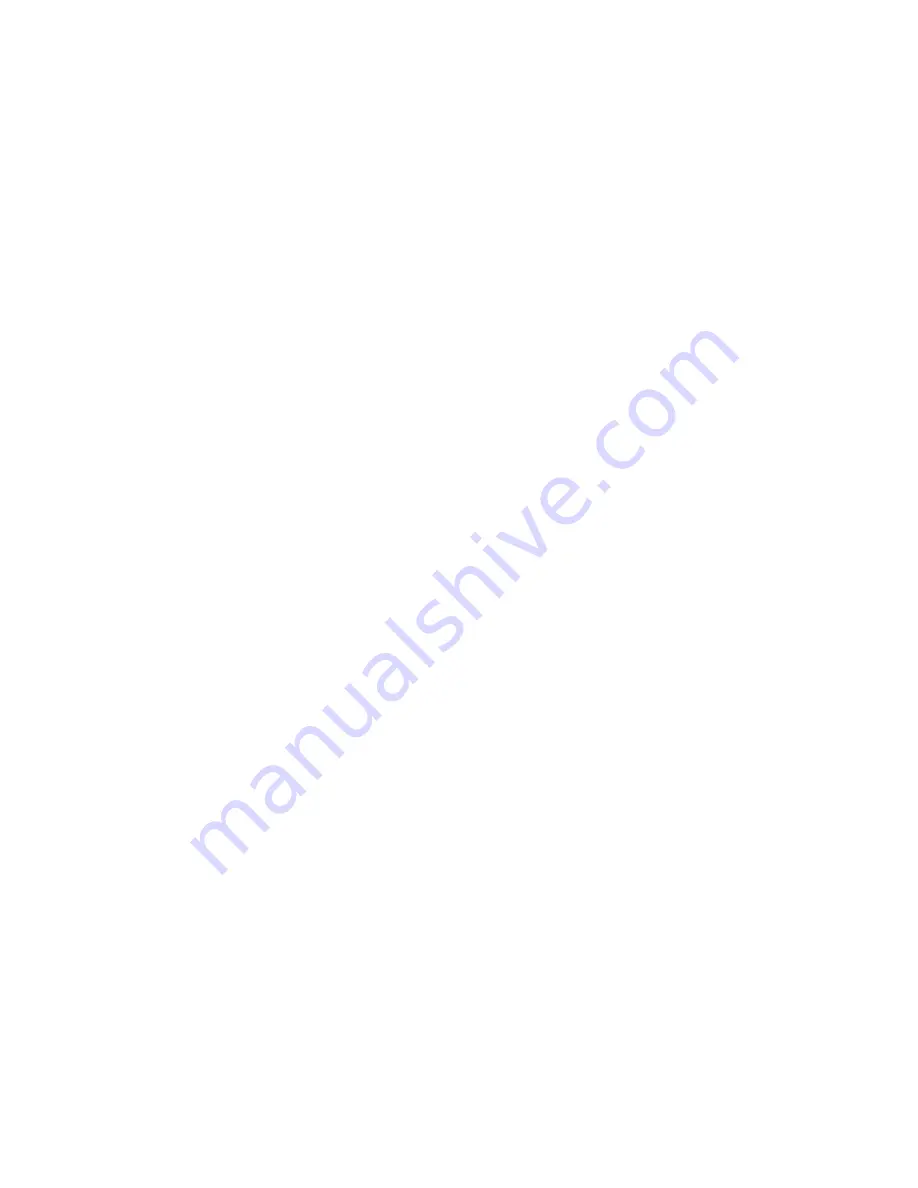
-4-
SET-UP & CALIBRATION
(See Dip Switch Table on page 5 and component
locations on page 6 for reference)
When placing the amplifier and actuator into
service, the amplifier must be calibrated for the appli-
cation. The servo amplifier is supplied factory cali-
brated when ordered with a Jordan Controls actuator
and should require only minor adjustment.
Read and follow the instructions carefully before
attempting to make adjustments to the servo amplifier.
1
. Make sure that the 120 or 240 Vac, single phase,
line power selector switch is in its proper position
(corresponds to the incoming power supply).
Improper selection will cause product failure.
(Located in blue box labled SW1)
2
. Check connections.
Power should be off and
actuator load disconnected for initial set-up
.
Check that the amplifier is properly mounted, that
all connections to the actuator are in accordance
with the correct Jordan Controls wiring diagram,
and that the unit is properly grounded in accor-
dance with all prevailing electric codes. Incorrect
wiring may cause permanent damage to the servo
amplifier and actuator. Verify that the command
signal is connected to the proper terminals. Using
a voltmeter, confirm that the command signal is
present and properly polarized.
3
. Verify settings. The DIP SWITCH is located on the
servo amplifier. Refer to the dip switch table on
page 5. Confirm that the switches are properly set
for the intended application. For special applica-
tions not listed, consult factory. Incorrect DIP
SWITCH settings will prevent proper operation.
Again, refer to the wiring diagram supplied with
the actuator for correct switch configuration.
4
. Insure that the output voltage jumper on TB1 pins
is in the correct position to correspond with the
actuator nameplate voltage (90 or 180 Vdc). See
page 6 for the location of this jumper.
5
. Apply input power.
6
. Set
ZERO
and
SPAN
. Apply command signal at
minimum input value. For 4-20mA systems this
would normally be 4mA. Adjust potentiometer
(pot) labeled
ZERO
to move actuator position to
correspond with minimum desired position,
without actuating the end of travel limit switch.
Next apply command signal at maximum input
value. For 4-20mA systems this would normally be
20mA. Adjust pot labeled
SPAN
to move actuator
position to correspond with maximum desired
position, without actuating the end of travel limit
switch. Some interaction of the above pot settings
will require repeating this procedure until proper
accuracy is achieved.
7
.
SPEED
adjust pot must be set to limit the output
voltage to a maximum of either 90 or 180 Vdc to
match actuator nameplate voltage. It may also be
adjusted to reduce this voltage output, slowing
actuator speed to match system dynamics.
WARNING: Do not exceed catalog speed rating
.
8
. The
BALANCE
pot is to adjust speed bi-directionally
to compensate for driven load dynamics such as
overhung and backdriving type applications. The
adjustment allows for matching actuator speed in
both directions of travel. To adjust, turn the balance
pot in one direction or the other until the actuator
speed is identical in both directions when under
load.
9
. Set
DEADBAND
pot. Deadband prevents unstable
operation, or hunting. Counterclockwise rotation
of the
DEADBAND
pot will increase the deadband,
preventing hunting. Clockwise rotation of the pot
will decrease the deadband, improving accuracy.
The correct setting is the point where no hunting
is observed AND when both the green and yellow
LED's go out when the actuator stops.
CAUTION
: The deadband must NEVER be ad-
justed to allow both the yellow and green LED's to
be on at the same time. This would result in danger-
ous motor and amplifier overheating and burnout.
10
. Set loop
GAIN
pot. Loop gain is the response and
stability of the actuator/amplifier combination. A
higher GAIN setting will result in better positioning
accuracy, but may cause the actuator to hunt or
oscillate when in NULL, overheating the amplifier
and shortening the actuator life. Clockwise rotation
of the
GAIN
pot increases the loop gain. With the
amplifier in null (red null LED on and actuator
stopped moving after responding to a command
signal) adjusts the
GAIN
pot until the actuator JUST
BEGINS to become unstable, or hunts. Then
rotate the pot ONE TURN COUNTERCLOCKWISE.
After setting loop gain, reset the DEADBAND as
described above. It may be necessary to reset the
GAIN and DEADBAND until proper loop response is
achieved.