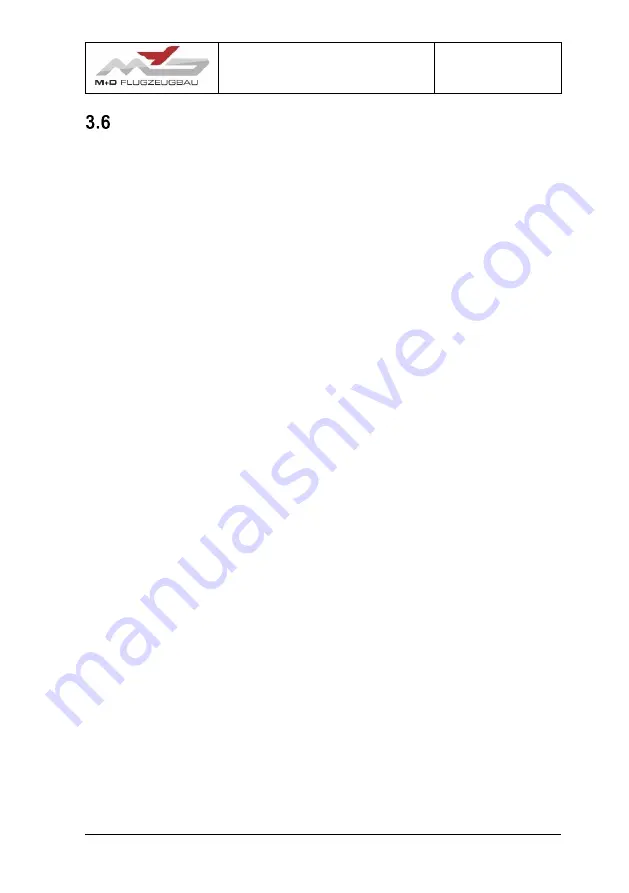
JS-MD 3
Aircraft Flight Manual
MD10-AFM-00-001
Issue: 01
Rev. 00
Rev. Date: 14-Feb-20
Page 3
–5
Spiral dive recovery
A spiral dive may occur when:
•
The aircraft terminates spinning automatically but the pilot
continues applying into-spin control inputs, or
•
During excessive slip angles with full rudder deflection.
Indications of a spiral dive are a high bank angle, increasing airspeed
and a high G-load.
Spiral dive recovery is performed by:
1. Apply the aileron, co-ordinated with the rudder, gently against
the direction of the turn until the wings are level with the horizon.
2. When the wings are level, neutralize both aileron and rudder.
3. Gently pull out of the resulting dive.
CAUTION:
During the resulting dive take care not to exceed V
NE
.