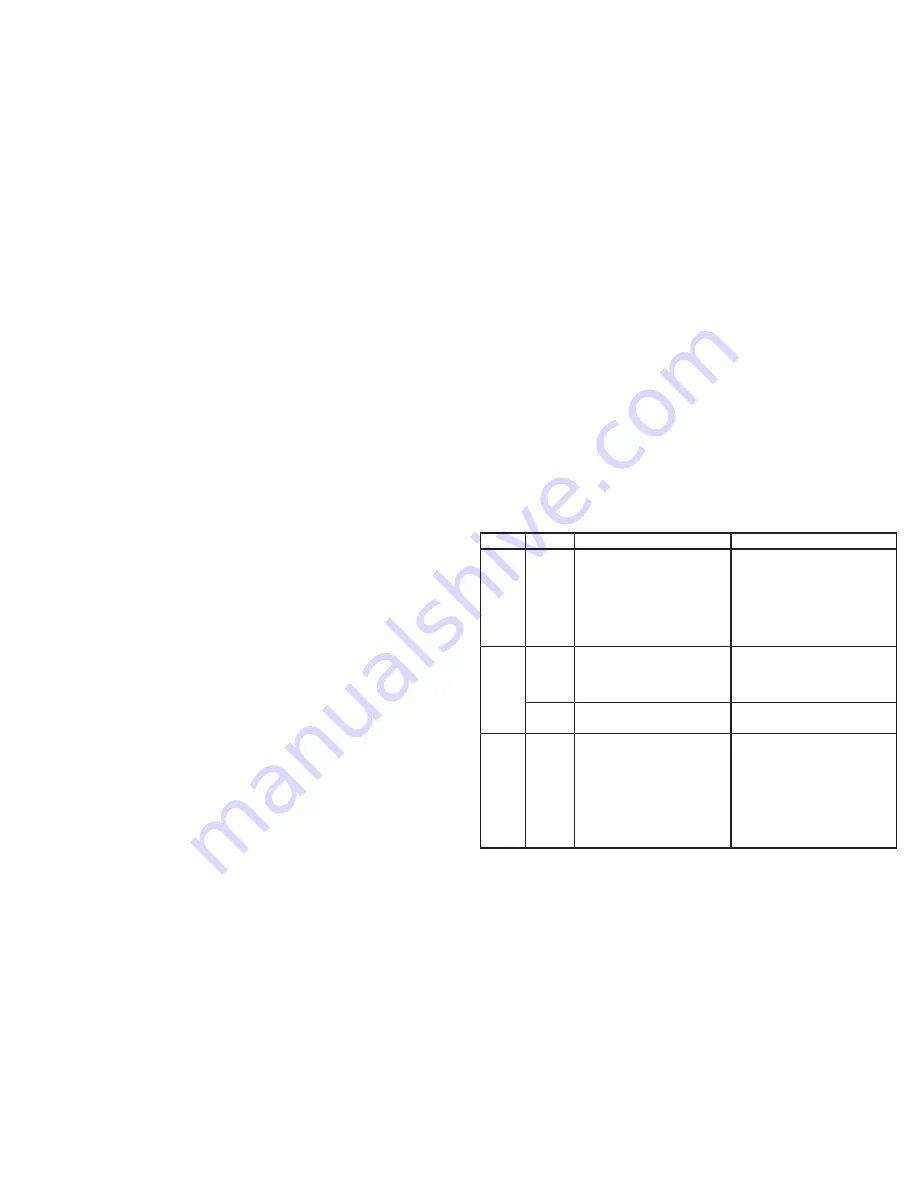
(6) 12-Gallon, 100 PSI Carpet Extractor
12-Gallon, 100 PSI Carpet Extractor (11)
3.0 Set-Up / Prepare Unit for Use
DO NOT USE ON WET SURFACES. DO NOT EXPOSE TO RAIN. STORE
INDOORS.
•
All Carpet Extractors, no matter what the time of year, are shipped with antifreeze in
the solution lines. Prior to first use, fill the tank with one quart of warm water. Attach
the hose and using the hand tool wand, flush out the system by spraying the one quart
of water through the pump.
•
Attach the 1-1/2 inch vacuum hose and the brass quick disconnect.
•
Fill the base unit (the recovery tank must be removed) with warm water (less than
100 degrees Fahrenheit). Fill to approximately 4 inches from the top. Use a liquid
detergent made for carpet cleaning or upholstery. Read and mix to the dilution ratios
as directed.
• Be sure to replace any filters back into the machine prior to use.
•
Do not use citrus acid, buterol or harsh degreasers inside the machine.
3.1 Electrical
Plug cord(s) into 20 AMP grounded wall outlet(s). 20 AMP circuits are normally found in
kitchens and bathrooms. Never remove ground prong from the plug. If a circuit breaker
trips during operation, turn machine off, reset the breaker and move the electrical cord to
a different outlet and resume operation.
3.2 Vacuum System
The extractor uses a dual vacuum motor system that provides outstanding water lift and
air flow.
Vacuum Float Assembly Warning System:
the float assembly on the vacuum stand
pipe prevents the waste tank from overflowing the stand pipe and damaging the vacuum
motors. Motors will reach a fast, high-pitched sound alerting you when the recovery tank
is about to over flow. When this happens, immediately turn OFF the vacuum switches and
empty the waste tank.
The float assembly has a filter to prevent lint and debris from entering the stand pipe.
Refer to the “Maintenance” section for removal and proper cleaning.
Recovery Tank:
the vacuum system requires the use of an external filter. The clear
view in-line filter is included with the machine and must be used on every job.
It is also necessary to use a defoamer to eliminate foam build-up in the recovery
tank which could lead to foam/moisture entering the vacuums and contributing to
early failure of the vacuum motors.
If moisture does enter the vacuum motors, contact an authorized service center. To
prevent moisture from damaging the vacuum motors during storage, empty the recovery
tank and store with the lid open.
6.0 Storage and Freeze Protection Continued
Recommended Procedure for Storage Continued
•
Disconnect the solution hose from the chemical feed and allow the system to bypass
for 10 minutes. This will work antifreeze into the pressure gauge.
•
Attach and wands and hand tools that will also be stored with the Carpet Extractor.
Open the valve for 30 seconds, directing the spray to the solution tank. Disconnect the
hose and with the valve open and the jets pointing down, depress the dimple on the
male QD. This will drain the solution out of the tool. Drain thoroughly before storing.
•
Turn off the pump and disconnect all hoses and tools. Vacuum out the solution tank
and thoroughly drain the recovery tank and vacuum hose.
To return to service, flush the pressure system by repeating the above steps, using
fresh water in place of antifreeze.
7.0 Trouble Shooting Guide
Never operate this Carpet Extractor when the equipment is not performing as expected
or when any part is visibly damaged. When repair is needed, take the equipment to an
authorized service center.
System
Problem
Possible Cause
Remedy
Vacuum
System
No Vacuum
/ Weak
Vacuum
1.
Vacuum Tank Full
2.
Float Assembly Tank Screen Dirty
3.
Float Ball Stuck
4.
Damaged or Loose Vacuum Hose
5.
Dump Valve Open
6.
Access Lid not Sealed
7.
Vacuum Hose Clogged
8.
Air Intake Grid Clogged
9.
Leak in Recovery Tank
10.
Water Coming out of Vacuum Exhaust
1.
Empty Tank
2.
Clean the Screen with Water
3.
Tap Float to Unstick then Clean
4.
Attach or Replace
5.
Close Valve
6.
Replace Gasket
7.
Clear Debris
8.
Clean
9.
Clean and Dry Area, Patch with Silicone
10.
Use a Low Foaming Detergent
Electrical
System
Unit will not
Turn On
1.
Extension Cord not Plugged In
2.
Switch not in the “On” Position
3.
Building Circuit Overloaded
4.
Wiring Connections Loose
1.
Check if Machine and Cord are Plugged In
2.
Check Switches, Replace if Necessary
3.
Reset Circuit
4.
Unplug Machine and Check for Loose
Wires
Burning
Smell
1.
Vacuum Motor Hung Up
2.
Pump Motor Hung Up
1.
Replace Vacuum Motor
2.
Replace Pump
Pump
System
Pump is not
Running
Properly
1.
No Power to the Pump
2.
Jets on Wand are Clogged
3.
In-Line Water Filter is Clogged
4.
Debris in Solution Tank Covering Inlet
5.
Kinked or Loose Hose
6.
Pump Failed
7.
Quick Disconnects are not Completely
Locked Together
8.
Heater is Clogged with Deposits
9.
Pump is Pulsating
10.
Auto Prime Valve is Open
1.
Check the Electrical System
2.
Clean Jet Filters
3.
Clean In-Line Filter
4.
Clear Debris
5.
Check and Replace Hoses if Necessary
6.
Replace Pump
7.
Snap Quick Disconnects Together\
8.
Flush Heater with System Maintainer or
Replace if Necessary
9.
Check for Clogged Jets and Clean
10.
Close Valve