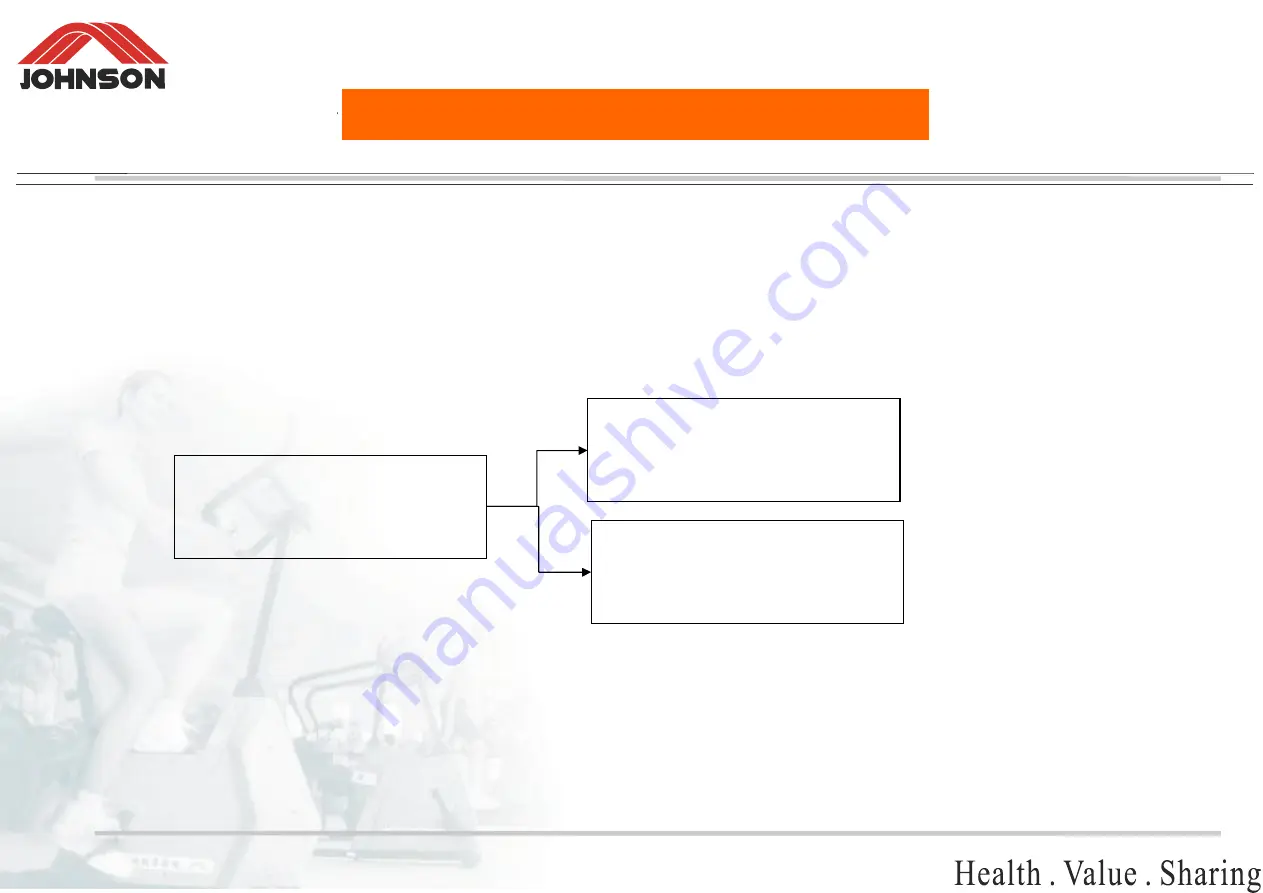
Johnson Health Tech. Co., Ltd.
Treatment:
a. First, rule out that the internal thermal protection of air pump is
caused by long-time operation
b. Judge whether the air pump works or not by listening to its sound.
c. Check if the solenoid valve works normally. No: Check air valve
connecting line or replace master control panel
No: check air pump
power supply
Normal (AC24-28V)
Replace air pump
Replace master
control panel
Normal
Abnormal
4-5.
All air bags do not work
All air bags do not work