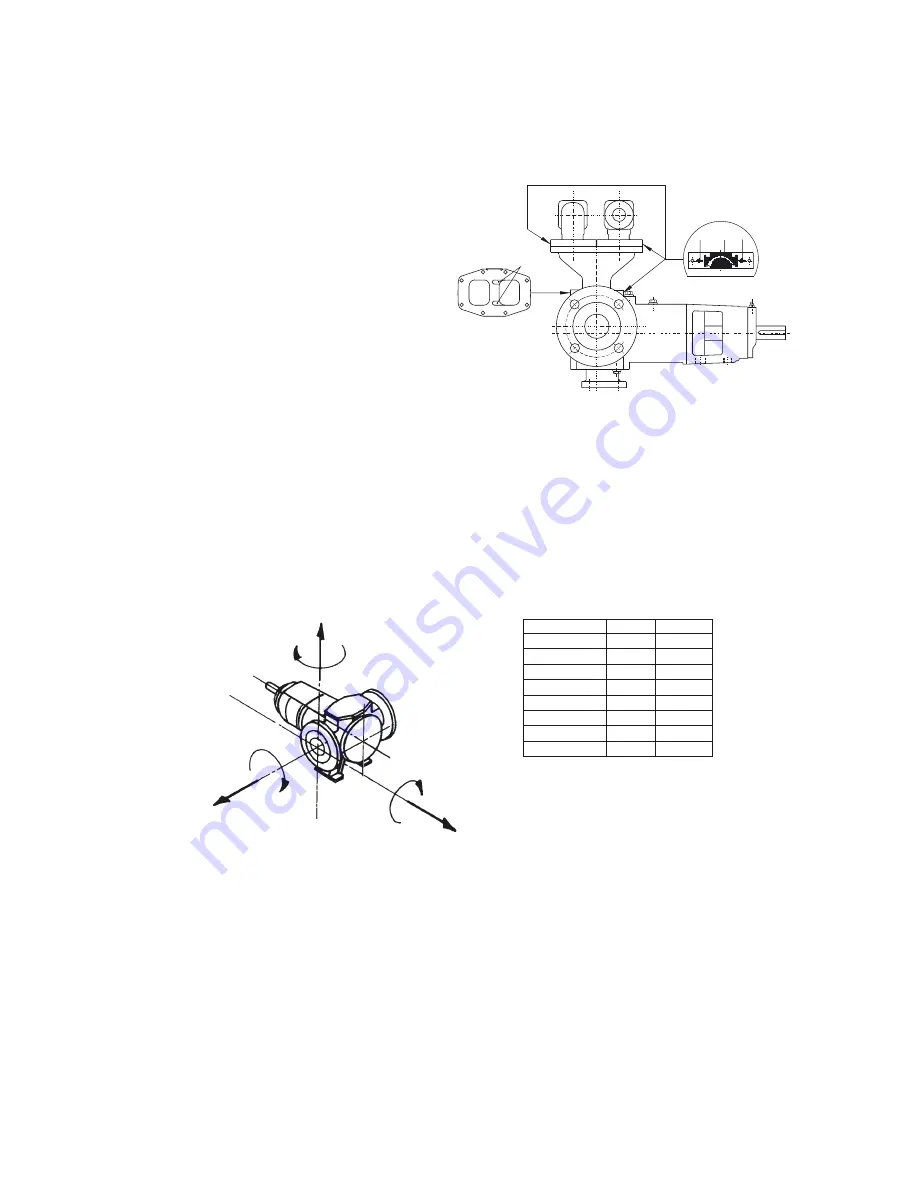
31
D
A
B
C
1 2
3
F
y
F
x
F
z
M
y
M
z
M
x
A.0500.501 – IM-TGGS/05.01 EN (03/2013)
3.18.5 Double safety relief valve
When a double safety relief valve is installed three arrow plates are attached – one on each valve
(A and B) indicating the liquid flow direction of each valve (small arrows 2 and 3) and one on the
Y-casing (C) indicating the most favourable direction of rotation of the pump (arrow 1).
The two suck-back grooves (D) will help
to evacuate air or gases during start-up
or whilst running. As they only function
in one direction of rotation, the Y-casing
should be positioned in such a way that
the suck-back grooves (D) are placed
towards the most used suction side.
In case of doubt, contact your local
supplier.
Be sure that the safety relief valves are
mounted opposite each other so that
the arrow plates on the safety relief
valves (A and B) are indicating opposite
liquid flow directions.
3.18.6 Suction and discharge pipes
3.18.6.1 Forces and moments
Note!
Excessive forces and moments on the nozzle flanges derived from piping can cause
mechanical damage to pump or pump unit.
Pipes should therefore be connected in line, limiting the forces on the pump connections.
Support the pipes and make sure they remain stress-free during operation of the pump.
See table for maximum allowable forces (F
x, y, z
) and moments (M
x, y, z
) on the nozzle flanges
with pump
on a solid foundation (e.g. grouted base plate or solid frame).
When pumping hot liquids attention should be given to forces and moments caused by thermal
expansion in which case expansion joints should be installed.
Check after connecting whether the shaft can move freely.
TG GS pump size
F
x, y, z
(N)
M
x, y, z
(Nm)
2-25
2000
315
3-32
2050
325
6-40
2200
385
15-50
2600
675
23-65
2900
800
58-80
3550
1375
86-100
4100
1750
185-125
5900
3750