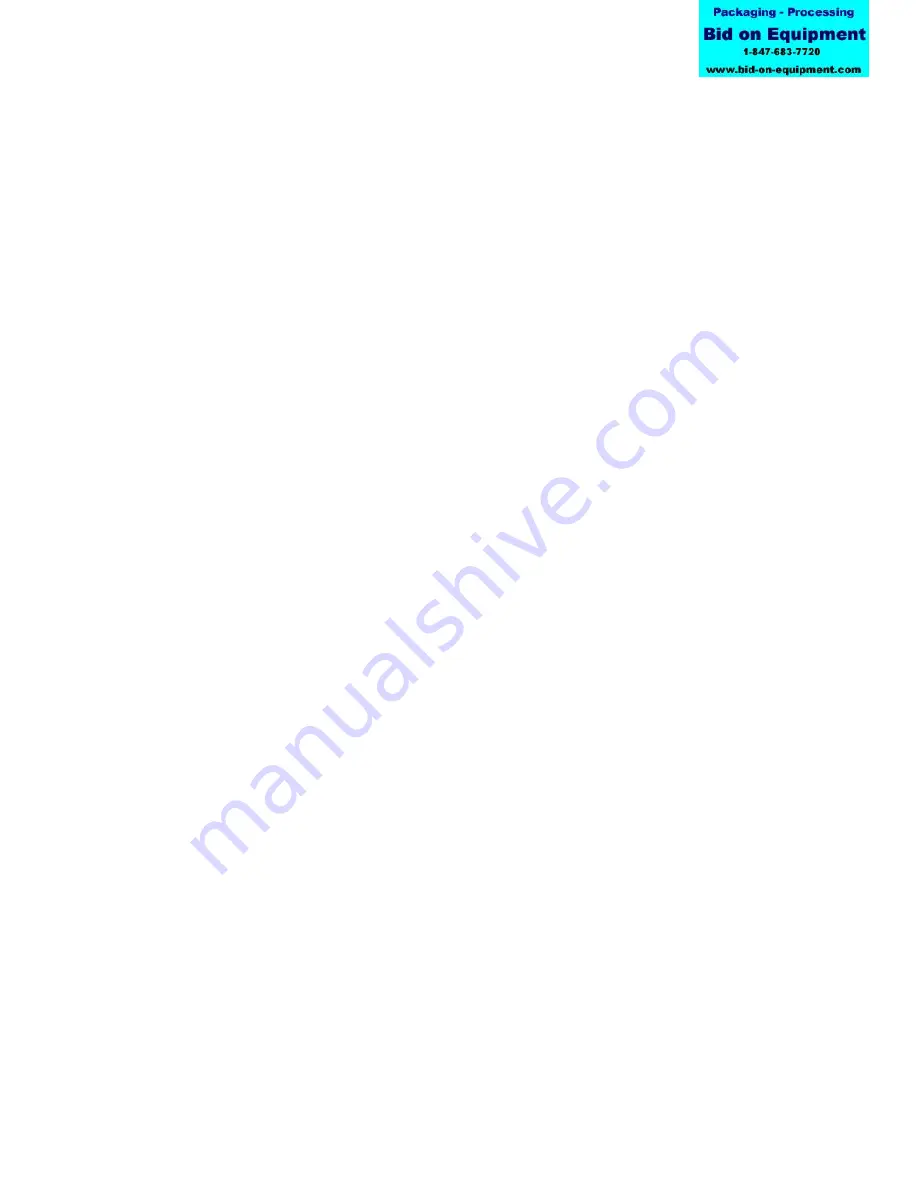
16
MDR/EN (0909) 1.0
4.5 Disassembly and assembly
See drawing, section 5.0.
Always wear suitable safety clothing. Clean the pump carefully before disassembling.
4.5.1 Disassembly
1. Place the pump vertically with the motor facing downwards and the pump body
upwards.
2. Remove the screws (pos 10) and the pump body (pos 8).
3. Remove the front wear plate (pos 4), the impeller (pos 6), O-ring (pos 7), shaft (pos 5)
and rear wear plate (pos 4). MDR105 and MDR116 have only the rear wear plate. The
front wear plate is integrated in the impeller.
4. Remove the magnet housing (pos 3) including the reinforcement (pos 19 – not
available for MDR45).
5. If the motor, drive magnet or flange is to be replaced, loosen the two locking screws
(pos 2) locking the drive magnet onto the motor shaft. The screws can be reached
through the assembly hole in the flange (see section 5.0). Remove the drive magnet
(pos 13).
6. Remove the screws (pos 12) and the flange (pos 1).
7. Check and clean all the parts which will be reused.
4.5.2 Assembly
1. Place the motor with the shaft facing upwards. Check that the drive magnet (pos 13)
easily can be slided onto the motor shaft. If necessary the motor shaft should be
polished.
2. Assemble the flange (pos 1) to the motor with the assembling hole facing in the same
direction as the motor feet. Bolt the flange to the motor with the 4 screws (pos 12) and
the washers (pos 11). Secure with Loctice.
3. Assemble the drive magnet (pos 13) to the motor shaft and lock the drive magnet with
the two locking screws (pos 2). The screws can be reached through the assembling hole
in the flange (see section 5.0).
4. Assemble the magnet housing (pos 3) with the reinforcement (pos 19 – not available
for MDR45) on the flange and check that the drive magnet can be turned without
touching the magnet housing or reinforcement.
5. Assemble the rear wear plate (pos 4) onto the ceramic shaft (pos 5). Note that the
smooth side (without the ”dot”) of the wear plate must face the impeller bearing.
Assemble the shaft and wear plate in the magnet housing. Slide the impeller (pos 6)
onto the shaft followed by the front wear plate (pos 4) with the smooth side facing the
impeller bearing (not available for MDR105 and MDR116 where the front wear plate
is integrated in the impeller).
6. If reusing an old impeller, check that the impeller bearings are not worn beyond the
diameter specified in section 4.4. If the bearings need to be replaced, the new bearings
must be reamed jointly after assembly in the impeller. Turn the impeller by hand and
check that it is running easily on the shaft.
7. Assemble the O-ring (pos 7)
for MDR45 and MDR85 in the groove of the magnet housing
for MDR75 in the groove of the pump body
for MDR105 and MDR116 at the dia 135 mm in the magnet housing.
8. Assemble the pump body (pos 8) and tighten the screws (pos 10) together with the
washers (pos 9) and nuts (pos 15).
Note!
For the MDR116 the spacer (pos 16) must be mounted before assembly in the
pump body.