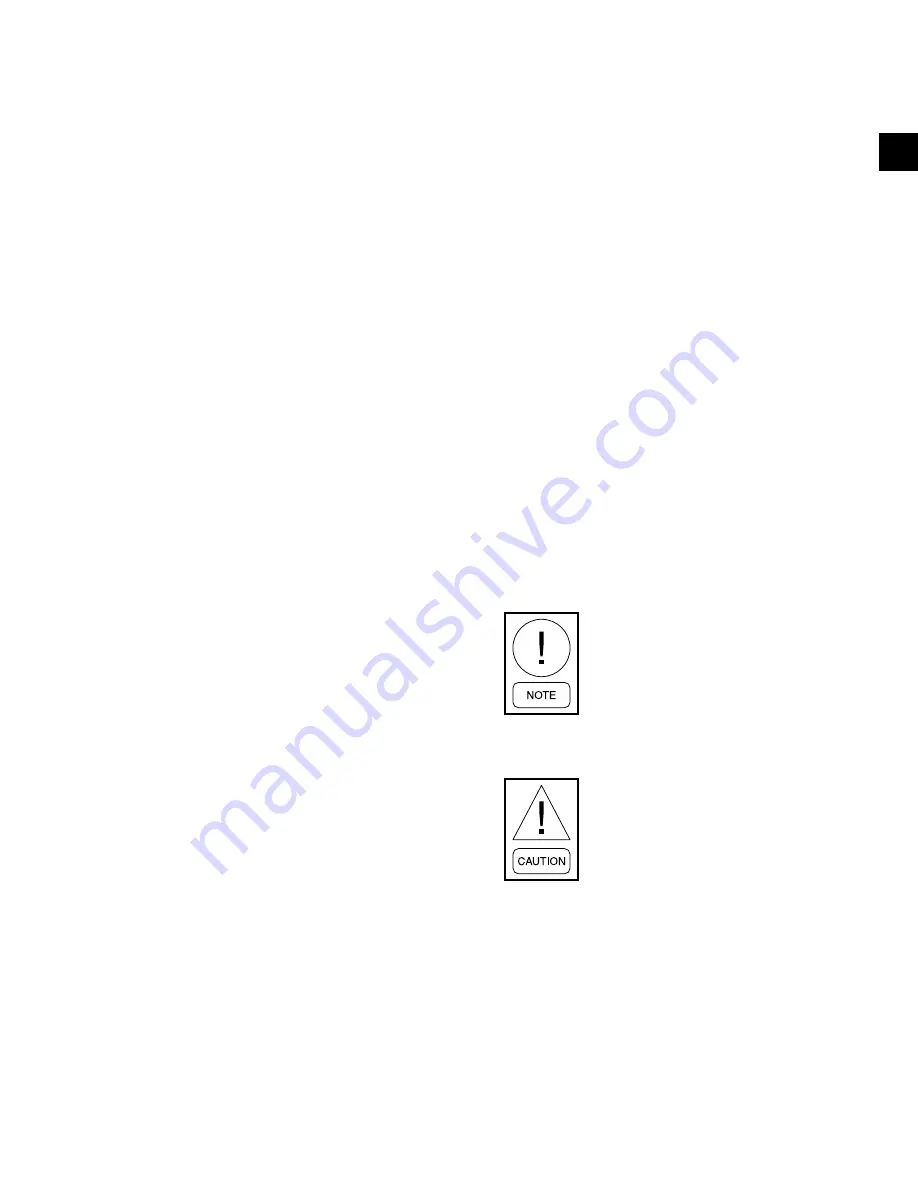
JOHNSON CONTROLS
21
SECTION 2 - INSTALLATION
FORM 160.78-N1
ISSUE DATE: 5/30/2012
2
ing Guide (Form 160.78-EG1)
for required minimum
Condenser and Evaporator temperatures. Refer to
Figure
8
for typical water piping schematic.
Stop Valves
Stop valves may be provided (by others) in the evapora-
tor and condenser water piping adjacent to the unit to
facilitate maintenance. Thermometer wells and pressure
taps should be provided (by others) in the piping as close
to the unit as possible to facilitate operating check.
Flow Switches
Thermal type water flow switches are factory mounted
in the chilled and condensed water nozzles and are fac-
tory wired to the OptiView™ Control Panel. These sol-
id-state flow sensors have a small internal heating ele-
ment and use the cooling effect of the flowing fluid to
sense when an adequate flow rate has been established.
Waterbox Drain And Vent Valves
Drain and vent valves (by others) should be installed
in the connections provided in the evaporator and con-
denser liquid heads. These connections may be piped
to drain if desired.
Checking Piping Circuits And Venting Air
After the water piping is completed, but before any
water box insulation is applied. Tighten and torque to
maintain between 30 and 60 ft. lbs. (41 and 81 N·m)
the nuts on the liquid head flanges. Gasket shrinkage
and handling during transit cause nuts to loosen. If wa-
ter pressure is applied before tightening is done, the
gaskets may be damaged and have to be replaced. Fill
the chilled and condenser water circuits, operate the
pumps manually and carefully check the evaporator
and condenser water heads and piping for leaks. Repair
leaks as necessary.
Before initial operation of the unit both water circuits
should be thoroughly vented of all air at the high points.
Refrigerant Relief Piping
Each unit is equipped with pressure relief valves lo-
cated on the condenser and on the evaporator for the
purpose of quickly relieving excess pressure of the re-
frigerant charge to the atmosphere as a safety precau-
tion in case of an emergency, such as fire.
Refrigerant relief vent piping (by others), from the relief
valves to the outside of the building, is required by code
in most areas and should be installed on all chillers. The
vent line should be sized in accordance with the ANSI/
ASHRAE-15, or local code. The vent line must include
a dirt trap in the vertical leg to intercept and permit clean
out and to trap any vent stack condensation. The piping
MUST be arranged to avoid strain on the relief valves,
using a flexible connection, if necessary.
Unit Piping
Compressor refrigerant piping and system external
piping are factory installed on all units shipped assem-
bled. On units shipped dismantled, the piping should
be completed under the supervision of the Johnson
Controls representative.
Control Wiring
On units shipped disassembled, after installation of the
control center, control wiring must be completed be-
tween unit components and control center, solid state
starter, or variable speed drive, when used, using wir-
ing harness furnished. Refer to
YMC
2
Field Connec-
tions Manual (Form 160.78-PW1)
Field wiring connections for commonly encountered
control modifications (by others) if required, are shown
in the
YMC
2
Unit Wiring and Field Control Modifica-
tions Manual (Form 160.78-PW2)
.
No deviations in unit wiring from that
shown on drawings furnished shall be
made without prior approval of the John-
son Controls representative.
Power Wiring
DO NOT cut wires to final length or make
final connections to starter power input
terminals until approved by the Johnson
Controls representative.
Supplied Variable Speed Drive.
The factory mounted Variable Speed Drive does not
require wiring to the compressor motor. The mo-
tor power wiring is factory connected to the Variable
Speed Drive (refer to the
YMC
2
Unit Wiring and Field
Control Modifications Manual (Form 160.78-PW2))
.
All wiring to the control panel is completed by the fac-
tory. A control transformer is factory furnished with
the Variable Speed Drive.