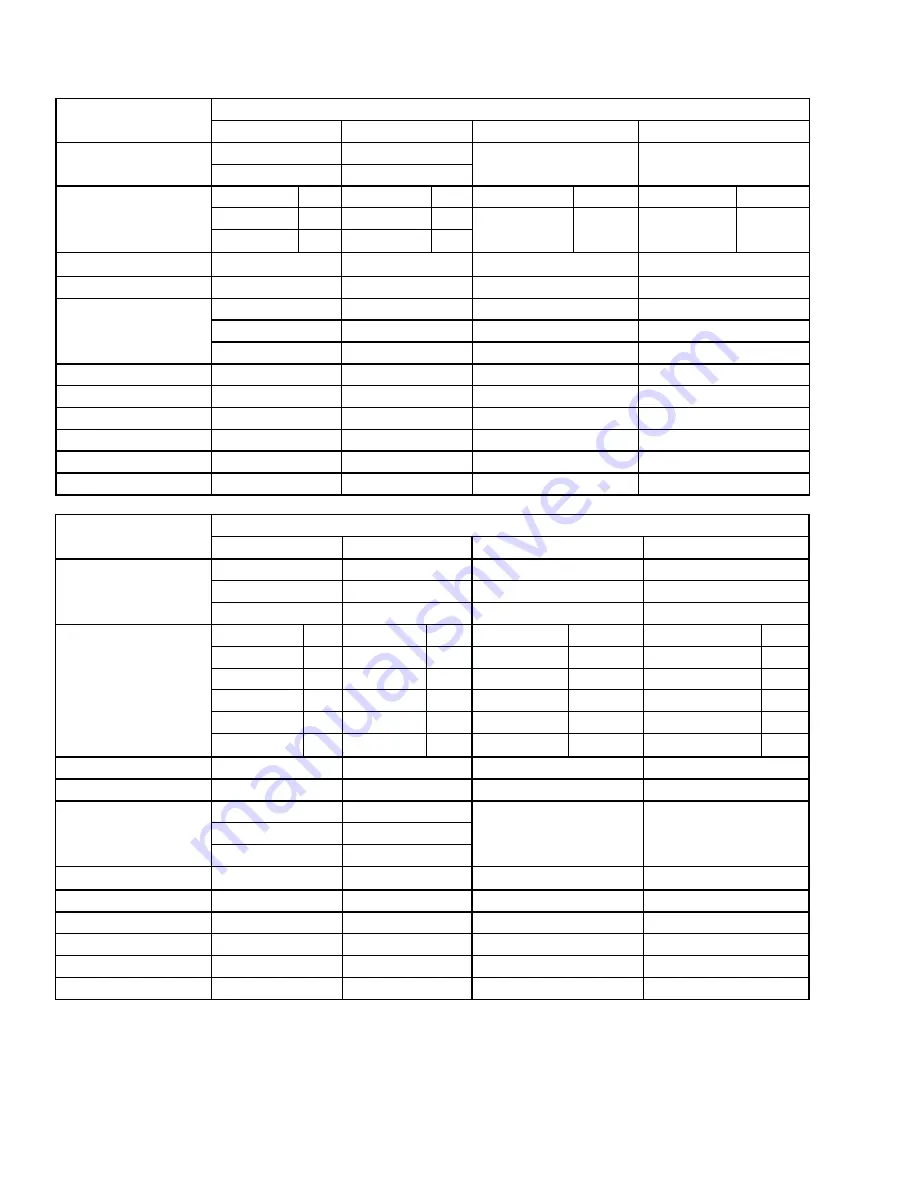
JOHNSON CONTROLS
10
FORM 50.40-OM1 (713)
ISSUE DATE: 07/17/2013
SECTION 1 - INTRODUCTION
TABLE 2 -
RSR SPECIFICATIONS – METRIC
DESCRIPTION
MODEL
RSR-1100V
RSR-1600V
RSR-1100V114
RSR-1600V114
Refrigerant
CFC-11
CFC-11
CFC-114
CFC-114
HCFC-123
HCFC-123
Refrigerant Storage
Capacity (kg)
80% Full at 32° C
Refrigerant
kg
Refrigerant
kg
Refrigerant
kg
Refrigerant
kg
CFC-11
478
CFC-11
680
CFC-114
478
CFC-114
680
HCFC-123
478
HCFC-123
680
Working Pressure (kPA)
345
345
345
345
Kilowatts
0.75
0.75
1.5
1.5
Standard Voltages
115V-1-60
115V-1-60
115V-1-60
115V-1-60
208V-1-60
208V-1-60
208V-1-60
208V-1-60
230V-1-60
230V-1-60
230V-1-60
230V-1-60
Plugs Included
Yes
Yes
Yes
Yes
Weight (kg)
318
386
318
386
L x W x H (mm)
1549 x 609 x 1386
2134 x 609 x 1346
1549 x 609 x 1346
2134 x 609 x 1346
Wheels Included
Yes
Yes
Yes
Yes
Relief Valves
(2) 1-1/4” FNPT
(2) 1-1/4” FNPT
(2) 1-1/4” FNPT
(2) 1-1/4” FNPT
ASME Approved
Yes
Yes
Yes
Yes
DESCRIPTION
MODEL
RSR-2212
RSR-2222
RSR-4436
RSR-4445
Refrigerant
CFC-12, 500 & 502 CFC-12, 500 & 502
CFC-12, 500 & 502
CFC-12, 500 & 502
HCFC-22
HCFC-22
HCFC-22
HCFC-22
HFC-134a
HFC-134a
HFC-134a
HFC-134a
Refrigerant Storage
Capacity (kg):
80% Full at 32°C
Refrigerant
kg
Refrigerant
kg
Refrigerant
kg
Refrigerant
kg
CFC-12
562
CFC-12
992
CFC-12
1804
CFC-12
2265
HCFC-22
511
HCFC-22
900
HCFC-22
1638
HCFC-22
2057
CFC-500
440
CFC-500
878
CFC-500
1589
CFC-500
1995
CFC-502
531
CFC-502
927
CFC-502
1702
CFC-502
2137
HFC-134a
517
HFC-134a
903
HFC-134a
1659
HFC-134a
2082
Working Pressure (kPA)
345
2069
2069
2069
Kilowatts
1.1
1.1
7.5
7.5
Standard Voltages
115V-1-60
115V-1-60
460V-3-60
460V-3-60
208V-1-60
208V-1-60
230V-1-60
230V-1-60
Plugs Included
Yes
Yes
4 Prong
4 Prong
Weight (kg)
601
726
1452
1905
L x W x H* (mm)
2134 x 609 x 1349
2368 x 762 x 1527
3022 x 914 x 1956
2845 x 1067 x 2286
Wheels Included
Yes
Yes
Optional
Optional
Relief Valves
(2) 5/8” Flare
(2) 3/4” FNPT
(2) 1” FNPT
(2) 1” FNPT
ASME Approved
Yes
Yes
Yes
Yes
*Wheels add 330 mm to overall height dimension of RSR-4436 and 4445.