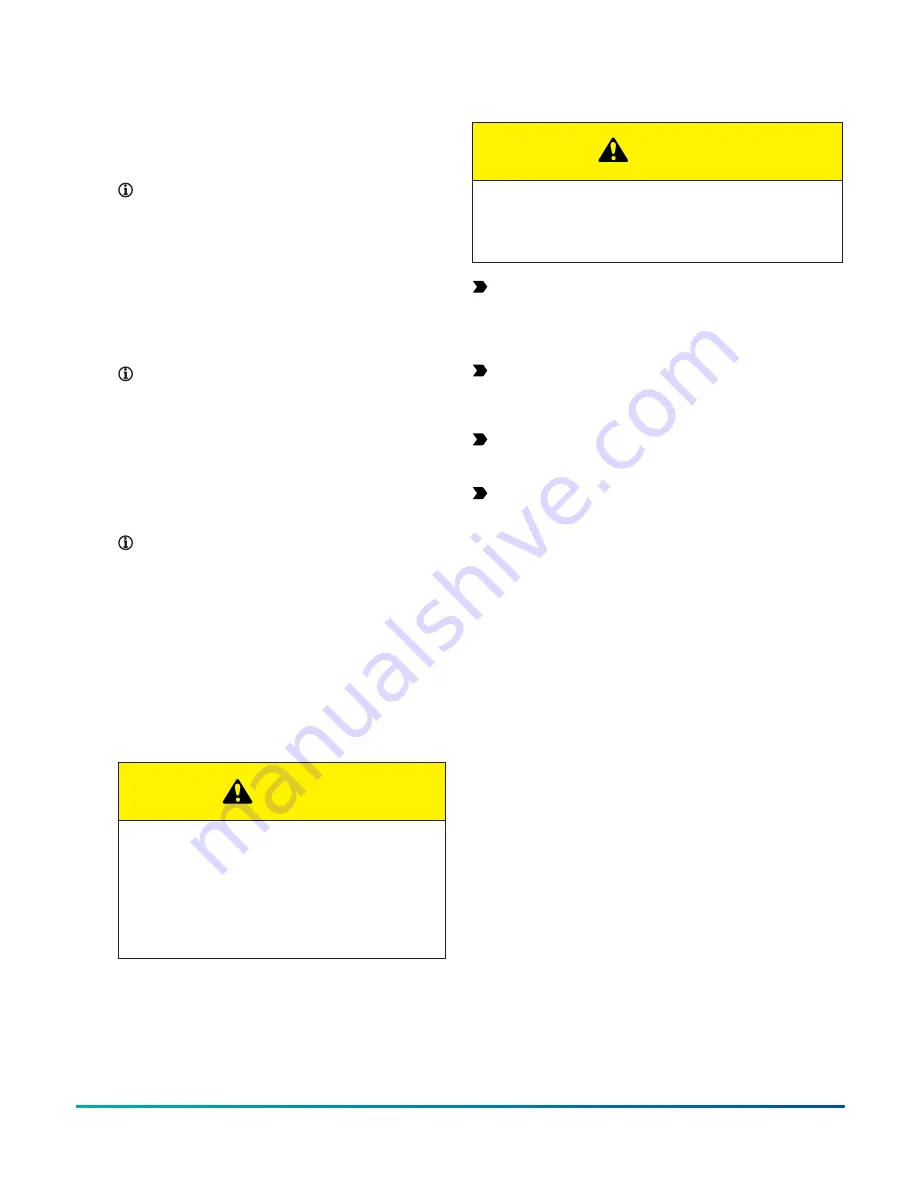
For 45° and 60° boxes, you must provide hard stops
at both full-closed and full-open damper positions.
When you install the controller at the full-open
position, the controller provides the open stop for
45° and 60° boxes. The closed damper seal pro-
vides the full-closed stop.
Note:
The integrated actuator has a stroke
time of 60 seconds for 90° of travel. The
stroke time is the amount of time (in seconds)
that it takes the actuator to move from the
fully closed to the fully opened position
or from the fully open to the fully closed
position.
8. Tighten the square coupler bolt to the shaft with an
8 mm (5/16 in.) wrench or 10 mm (3/8 in.) 12-point
socket. Tighten to 10.5 N·m to 11.5 N·m (95 to 105
lb·in).
Note:
The models have either a round shaft
up to 13 mm in diameter, or a 10-mm square
shaft.
9. Loop the pneumatic tubing that field personnel
supply to include a trap for condensation. Take the
needed length of tubing that field personnel supply
and install, and attach one end to the dual port
fitting on the controller, and attach the other ends
of the tubing to the pressure transducer in the VAV
box application.
Note:
The controller uses a digital differential
pressure sensor with bidirectional flow
operation. You can connect the high- and low-
pressure DP tubes to either barbed fitting
on the controller. You do not need to make
a specific high- or low-side connection when
you attach the tubing to the barbed fittings
on the controller.
10. Push the
Manual Override
button, and turn the
actuator coupling manually to ensure that the
actuator can rotate from full-closed to full-open
positions without binding.
11. Rotate the damper to the full-open position.
CAUTION
Risk of Property Damage
Rotate the damper to the full-open position
before starting the air handler. Failure to rotate
the damper to the full-open position may result
in damage to the VAV box or ductwork when
the air handler is started.
Wiring
CAUTION
Risk of Electric Shock
Disconnect the power supply before making electrical
connections to avoid electric shock.
Important:
Do not connect supply power to the
controller before you finish wiring and before
you check all wiring connections. Short circuits or
improperly connected wires can result in damage to
the controller and void any warranty.
Important:
Do not exceed the controller electrical
ratings. Exceeding controller electrical ratings can
result in permanent damage to the controller and
void any warranty.
Important:
Use copper conductors only. Make
all wiring in accordance with local, national, and
regional regulations.
Important:
Electrostatic discharge can damage
controller components. Use proper electrostatic
discharge precautions during installation, setup, and
servicing to avoid damaging the controller.
For detailed information about configuring and wiring an
FC bus or an SA bus, refer to the
MS/TP Communications
Bus Technical Bulletin (LIT-12011034)
.
Wiring guidelines
See
for terminal and bus port locations
on the controller. Observe the following guidelines when
you wire the controller.
Input and output terminals
See
I/O terminal blocks, ratings and requirements
for information about the functions, ratings, and
requirements for the input and output terminals. See
Cable and wire length guidelines
lengths guidelines.
In addition, observe the following guidelines when you
wire inputs and outputs:
• Run all low-voltage wiring and cables separate from
high-voltage wiring.
• Use twisted, insulated, and stranded copper wires for
all input and output cables, regardless of wire size or
the number of wires.
• Shielded cable is not required for input or output
cables. However, it is best practice to use shielded
cables for input and output cables that are exposed to
high electromagnetic or radio frequency noise.
• Cable runs of less than 30 m (100 ft) do not require an
offset in the input and output software setup.
• Cable runs over 30 m (100 ft) may require an offset in
the input and output software setup.
VAV1717 and VAV1732 VAV Controllers Installation Guide
6