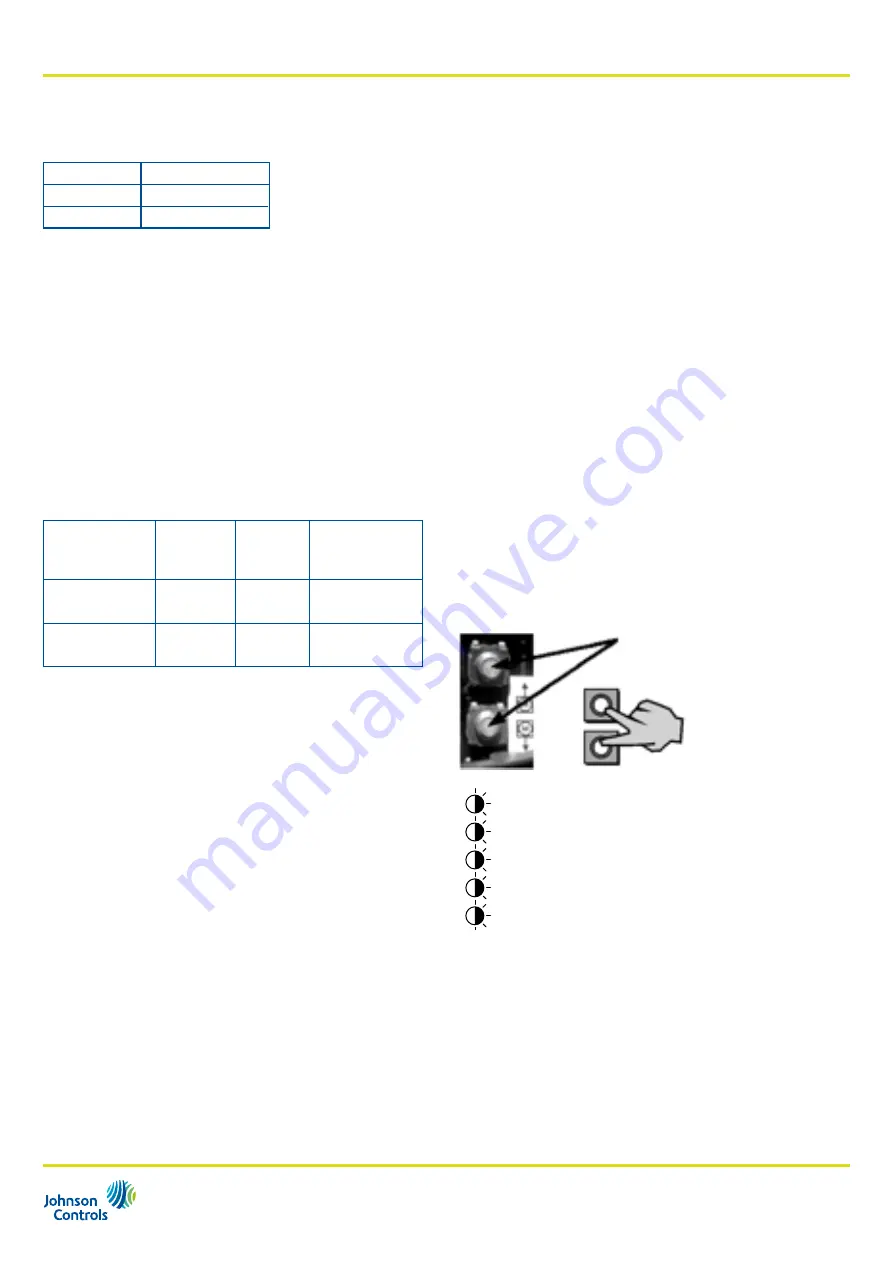
3
PB_VA-7700_Electricl Valve Actuators_02 2011
Operation
Floating■models■
Connections
Actuator■Stem
1-2
Extends
1-3
Retracts
Proportional■models■
(0…10■VDC■or■0(4)…20■mA)
The VA-77x6 provides a proportional stroke corresponding to the
control signal.
Following control signals are defined as standard:
0…10 VDC
0…5 VDC
5…10 VDC
0…20 mA
4…20 mA
Action■
(DIP■switch■set)
Input■
control■
signal
Actuator■
Stem
Position■at■
control-signal■
failure■*
Direct■(DA)
Increases
Decreases
Extends
Retracts
Selectable*
Selectable*
Reverse■(RA)
Increases
Decreases
Retracts
Extends
Selectable*
Selectable*
* "Signal failure" position pre-set does not operate when 0…20
mA control is selected
.
The action mode,
DA
(direct acting) and
RA
(reverse acting)
is set through the DIP switches
(see paragraph "DIP switch
settings")
.
The actuator control signal has a buffer zone, at each end of the
span, of 0.3 V or 0.3 mA.
This ensures definite valve close-off.
Control■signal■failure■pre-set■position■
(not functional with 0…20 mA control selected)
A control-signal failure on proportional models will cause the
actuator to automatically move the stem to a (via DIP-switches)
pre-selected position (100% extended or 100% retracted).
Auto■Calibration■procedure■with■standard■
input■signal■ranges.
The standard control signals are selected by setting DIP switches
3 and 4 switch
(see paragraph "DIP switch settings").
It is recommended to set the actuator to the desired control signal
and action before fitting to the valve
(see paragraph "DIP switch
settings").
Power must be connected before the auto-calibration cycle can
be started.
Procedure:■Actuator■is■mounted■on■valve.
• Verify that with the stem fully retracted, there is a minimum
distance of 1 mm between the top of the actuator stem nut and
the stem guide bush in the actuator motor housing base plate.
If necessary correct the distance by adjusting the actuator /
valve stem connection.
• To start the auto calibration cycle, push both calibration buttons
for at least 5 seconds. The actuator will make a full cycle to
detect the stem extended and retracted limits.
• When the auto calibration cycle is completed the LED
stop flashing, the actuator stem moves to the position that
corresponds to the control signal and the five LED indicate the
stem position.
• When the control signal changes the actuator stem moves to
the new position this is indicated by one flashing LED. The LED
stops flashing when the position corresponding to the control
signal has been reached.
Note:
When ever the actuator is newly placed on a valve,
auto-calibration must be carried out.
Calibration buttons
> 5 sec
During auto-calibration cycle all five
status indication LED flash simultaneusly