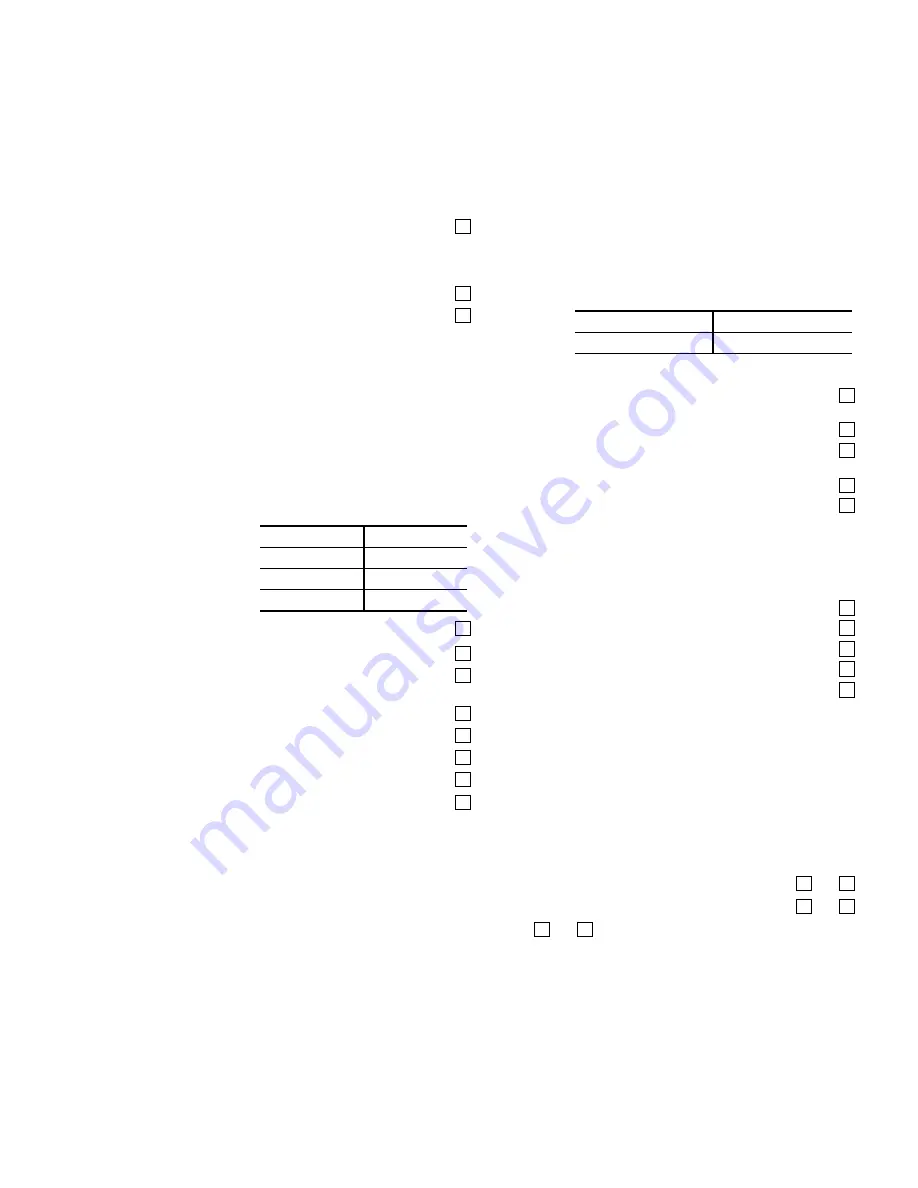
37
SECTION 1 - INSTALLATION
FORM 145.18-IOM2
ISSUE DATE: 06/17/2020
C. WATER LOOP
CAUTION: Entering Water Temperature (EWT) should
be within the Optimal Temperatures listed in the IOM. Out
of range measurements indicate a water flow issue in the
building's water system that may result in equipment dam-
age and degraded performance.
HEATING
COOLING
EWT:
°F
°F
LWT:
°F
°F
Verified Entering Water lines are connected to IN
and Leaving Water lines are connected to OUT on
chassis
.......................................................................
Verify water riser stub penetrations into cabinet are
sealed to prevent air leaks from unconditioned space
.
Trapped condensate drain .........................................
Inspected condensate drain for leaks or blockage
by pouring water into drain
.........................................
Optional circulating pump operating ..........................
Size of Auto-Flow Regulator
________________ GPM
Actual flow measurement
___________________ GPM
D. CONTROLS
Non-heat pump thermostat setting checked
..............
Thermostat options operational: Fan
.........................
Cooling ...................
Heating ...................
Optional continuous fan operational
..........................
A. ELECTRICAL
Measured supply voltage unit: __________________
Unit Disconnect operational ......................................
Panel fuse/breaker size:
__________________ AMPS
Optional inline fuse size:
__________________ AMPS
Connections checked for tightness
............................
Circuit checked for shorts and ground faults
..............
Fan speed 1: ___________________________ AMPS
Fan speed 2: ___________________________ AMPS
Compressor: ___________________________ AMPS
Control voltage: _________________________VOLTS
B. AIRSIDE
NOTE: CFM measurements should be within the param-
eters listed in the associated tables in the IOM.
HEATING
COOLING
Coil Inlet (Dry Bulb)
°F
°F
Coil Outlet (Dry Bulb)
°F
°F
Coil Inlet (Wet Bulb)
°F
°F
Coil Outlet (Wet Bulb)
°F
°F
Unit supply airflow properly balanced
........................
Chassis positioned so front gasket is engaged
..........
Air coil clean & unrestricted .......................................
Properly-sized and recommended MERV rated
filters in place
.............................................................
Filters clean................................................................
Secured all panels .....................................................
Checked chassis vibration
.........................................
Cleaned debris from cabinet
......................................
Service Tec
hnician's Signature:
_____________________
Customer Rep's Signature: ________________________
Mailing Address: _________________________________
_______________________________________________
Telephone No.:
__________________________________
START-UP AND PERFORMANCE CHECKLIST AND DATA
WARNING: Ensure the Prerequisite Checklist section has been properly evaluated. Failure to complete System Verification and
Electrical and Physical Inspection prior to completing these checks could result in possible injuries or damage to equipment.
Upon completion of start-up, please either scan and e-mail this completed Start-Up Checklist to
or mail a copy to:
Johnson Controls at 505 Finley Avenue, Ajax, ON Canada L1S 2E2
Warranty on this equipment will depend on Johnson Controls receiving this completed sheet.
BEFORE LEAVING JOB
1.
Warranty certificate filled out and given to owner?
Yes
No
2.
Operating & Maintenance Instructions given to owner?
Yes
No
3.
Owner instructed on System Operation?
Yes
No
____________________________
Owner's Name