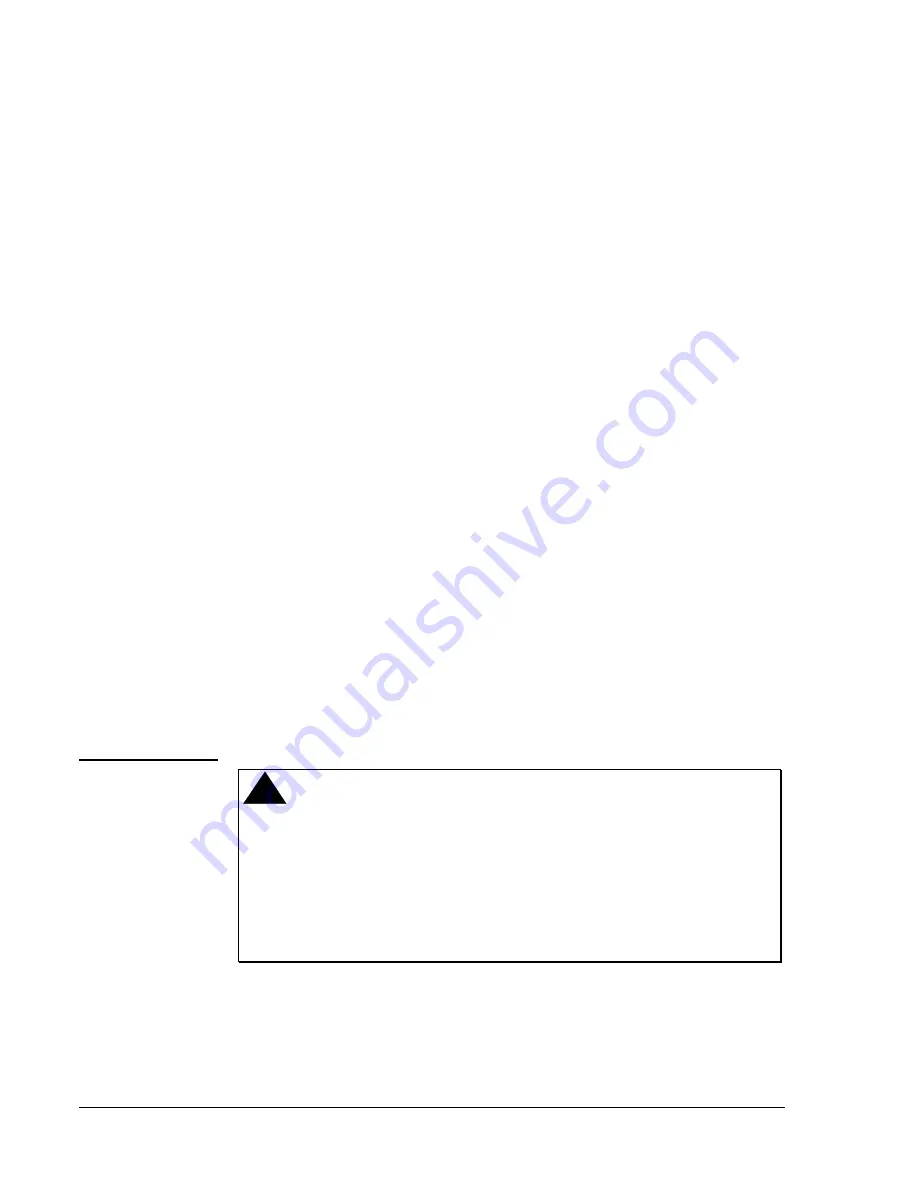
6 G Gas Combustion Combination Controls and Systems—G961DAJ Integrated Function Ignition Control
The controls are connected to a two stage thermostat. When the first stage
calls for heat (or cool), the blower motors are simultaneously energized,
but the ignition sequence (or cooling sequence) only takes place in the first
furnace. When the second stage calls for heat (or cool), the ignition
sequence (or cooling sequence) starts in the second furnace without
interrupting the operation of the blowers.
In any of the safety functions, soft lockout, or abnormal operation modes,
if only one furnace is affected, the other furnace will continue its normal
operating cycle and maintain control of the affected furnace’s blower.
The affected furnace will initiate its abnormal operating sequence, with
the exception of interrupting blower operation.
If the abnormal condition still exists after the demand for heat (or cool) is
satisfied, the safety function or abnormal operation sequence will take
over the operation of both blowers.
Twinning communications can be lost due to:
1.
Lack of continuity between “TWIN” terminals and/or between the
common terminals of the two furnaces.
2.
Loss of power in one of the twinned furnaces.
3.
The 24 VAC signal on the two controls out of phase.
A loss of communications will result in the two controls de-energizing all
outputs except the inducer, which runs for 4 seconds and the blower,
which runs for 180 seconds. The “OK” LED will flash to indicate loss of
communication between furnaces while in twinning mode. Once the
purge period expires, the controls attempt to restore communications
before returning to normal operation.
!
WARNING: Shock Hazard. Disconnect power supply before
wiring to prevent electrical shock or equipment
damage.
Fire or Explosion Hazard. If the control is installed
in an area that is exposed to water (dripping, spraying,
rain, etc.) it must be protected. If the control has been
exposed to water in any way, do not use it.
This instruction sheet is intended as a guide for qualified personnel installing
or servicing Johnson Controls ignition controls. Carefully follow all
instructions on this sheet and all instructions on the appliance. Limit repairs,
adjustments, and servicing to the operations listed in this sheet or on the
appliance.
Two Stage
Operation
Abnormal
Operation
Loss of
Communications
Installation and
Wiring