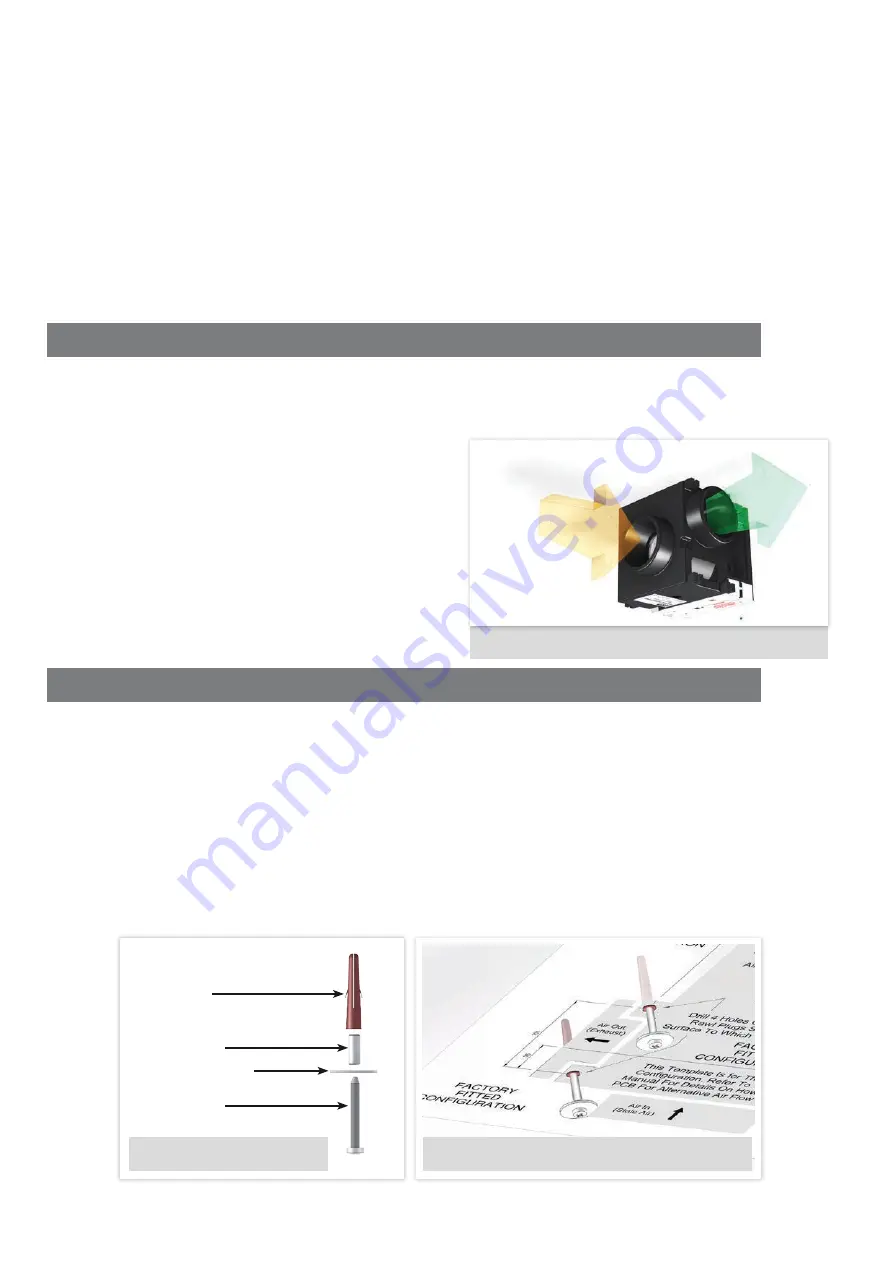
5
Sales/Replacement Telephone 01604 762881
FIGURE 2. AIRFLOW THROUGH UNIT
BASE MOUNTED
- with ducting connected horizontally and exhaust exiting through a wall or roof
terminal. If used in this position make sure there is an adequate working area with a secure base.
VERTICALLY MOUNTED
- when using flexible ducting ensure the connections are made, with the
correct radius bends.
SUSPENDED
- Ensure ductwork is supported throughout it’s length.
NOTE:
A clear space of at least 50mm below and 230mm to the sides is required to allow the cover to be
removed and provide sufficient access for maintenance.
7.3
SPIGOTS
7.3.1 The unit has one stale air inlet spigot and one exhaust air outlet spigot.
7.3.2
The spigot has and internal diameter of 100mm and 125mm outer diameter.
7.4
HANDING
7.4.1
If Q-Vent CE50 air flow configuration is required to be handed opposite to the factory default see
publication Number ZZ1518 for the correct change procedure.
8.
DUCT & DUCT CONNECTIONS
8.1
For satisfactory operation of the unit, ensure ducting used is as detailed on the design drawing. Any deviation
from the design drawing could lead to noise increase on boost.
NOTE:
In situations where it is either not possible or not desirable to use 125mm ducting on the stale air outlet.
100mm ducting can be used but it MUST be noted, in ‘BOOST’ mode, it might increase noise levels.
8.2
Where 125mm rigid ducting is used it must fit on the
125mm (outer) spigots and for 100mm ducting on the
100mm (inner) spigots.
IMPORTANT:
When inserting 100mm ducting into the spigot,
ensure it is no longer the 45mm.
8.3
Where rigid ducting is used, it should be installed using
the least number of fittings to minimise resistance to air
flow. Where possible, final connection from the rigid
ducting to grilles and the unit should be made with a
flexible connection.
8.4
The exhaust air must exit to outside through either a
wall or a roof and must be protected by a wall baffle or
recognised roof terminal.
9.
INSTALLATION INSTRUCTIONS
IMPORTANT: The installation should be carried out by a competent person in accordance with the appropriate
authority and conforming to all the statutory and governing regulations.
NOTE:
The enclosure of this product is made from EPP. Failure to use the correct screw spacers or the over
tightening of any screws may damage the appliance.
9.1
Identify the directional airflow requirements and determine if the factory configuration is suitable. If not, then
refer to document ZZ1518 to re-configure to an alternative airflow.
9.2
Place the template in the position and drill the 4 fixing holes. Take into consideration the material you are
drilling into and use appropriate screws and fixings to support the unit. Use the rawl plugs where necessary.
Use the M5 x 25mm washers and screw spacers provided. Alternative fixings may be used if deemed more
suitable to the site requirements at the time of installation. These are not included.
9.4
Fix the 2 screws, washers and 16mm spacers into the Air Out/Exhaust fixing holes as shown on the template.
DO NOT OVER TIGHTEN.
RAWL PLUG
16mm SPACER
M5 x 25mm WASHER
FIXING SCREW
EXHAUST
AIR OUT
STALE AIR IN
FIGURE 3. FIXING SCREW
FIGURE 4. TEMPLATE & FIXING SCREW