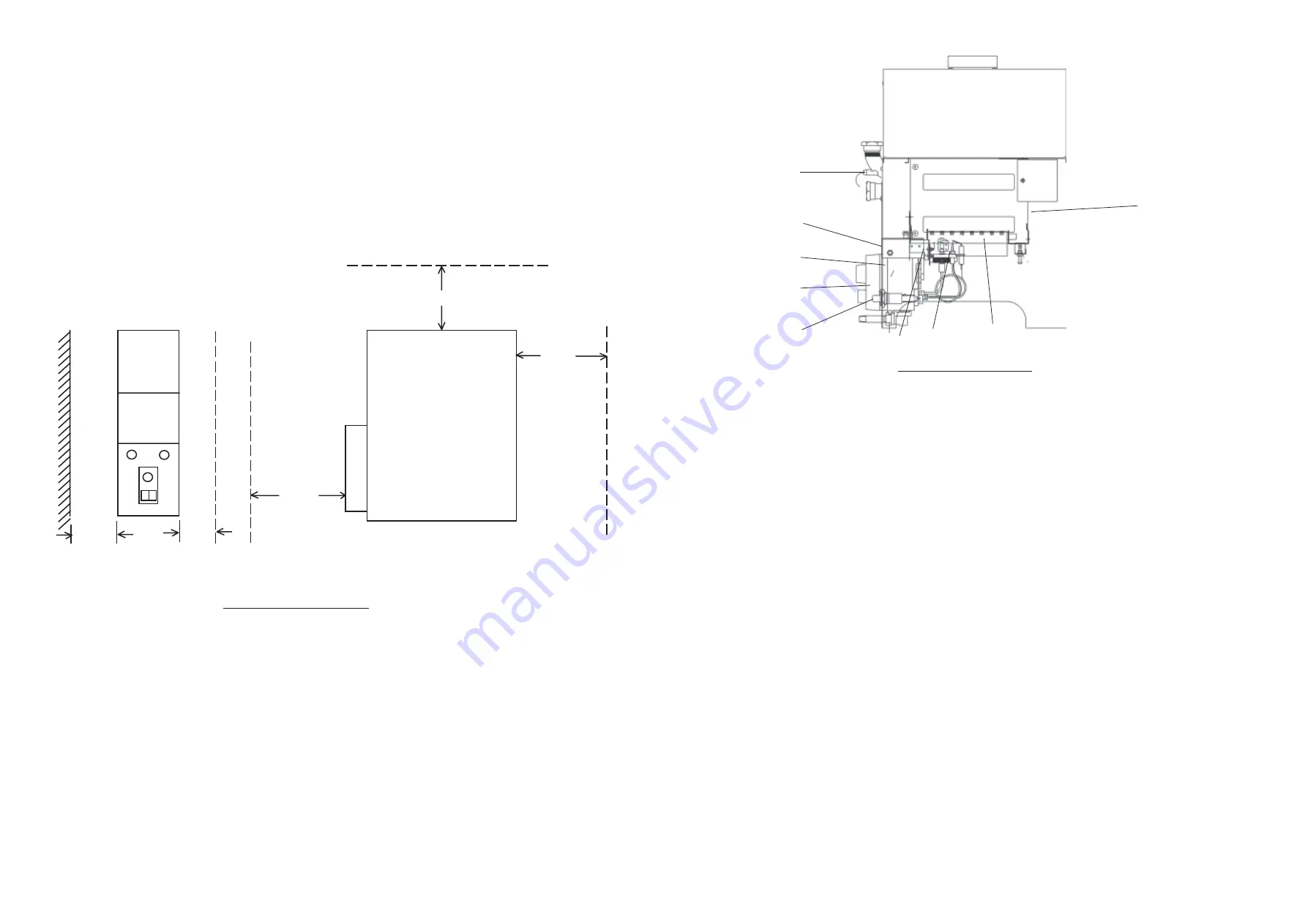
2.5
INSTALLATION AND CLEARANCES:
IMPORTANT: Care must be taken to ensure that adequate space is available at the front and ‘open’ side of the
heater for installation purposes.
2.5.1
Minimum clearance for combustion:
Front: 25mm (1in) from controls cover.
Sides: 16mm (
5
/
8
in) from side nearest to wall, 13mm (
1
/
2
in) from open side to any cylindrical obstruction
(i.e.. Hot water cylinder)
Note:
If these minimum side clearances are to be adopted, special care must be
taken in the compartment construction to permit access to appliance mountings.
Rear:
100mm (4in).
Base:
Nil. The appliance may be floor mounted on noncombustible material.
2.5.2
Minimum clearance for servicing:
Front: 300mm (12in).
Side:
200mm (8in).
Note:
Flow and return pipes may be routed over the top of the heater, provided adequate access is available for
heat exchanger cleaning.
2
16mm
13mm
WALL SIDE
OPEN SIDE
100mm
200mm
300mm
FRONT
REAR
Fig. 1
Minimum clearances for JANUS 6/30
3.
GENERAL REQUIREMENTS
3.1
RELATED DOCUMENTS (refer to current issues).
This appliance MUST BE installed in accordance with the relevant requirements of the Gas Safety (Installation and
Use) Regulations, local Building Regulations, and the Bye-laws of the local Water Company. It should also be in
accordance with any relevant requirements of the local Gas Region and Local Authority, and the relevant
recommendations of the following British Standard Codes of Practice:
BS 6798:
Specification for installation of gas fired hot water boilers of rated input not exceeding 60kW.
BS5546:
Installation of gas hot water supplies for domestic purposes (2
nd
family gasses).
BS5440 Pt. 1: Flues.
BS5440 Pt. 2 Air supply.
BS6891:
Installation of low pressure gas pipe work up to 28mm (R1) in domestic premises.
BS6700:
Design, Installation, testing and maintenance of services supplying water for domestic use within
buildings and their curtilages.
3.2
LOCATION:
3.2.1
The location chosen for the circulator must permit the provision of a satisfactory flue and termination, an
adequate air supply for combustion purposes, and an adequate space for servicing and air circulation around
the appliance.
The JANUS 6/30 must not be installed in a room containing a bath or shower, or either a
bedroom or a bed-sitting room.
11
2
3
6
4
1
5
7
8
9
9.
SHORT LIST OF SPARES
Key
G.C. No
J&S Part No
Description
Qty
1
242 279
S00102
Main Body Assembly
1
2
793 243
JAN6/30/062
Burner and Controls Assembly (comprising of)
1
3
244 878
S00301
Multifunctional Control Mini SIT
1
381 670
S00260
‘O’ Ring Seal
1
4
384 615
BOS 00562
Burner Arm
1
5
JAN3-0704000
Pilot burner mounting bracket
1
6
379 874
1000-0704265
Pilot Burner Assembly
1
1000-0704320
Pilot Gas Feed Pipe
1
397 819
1000-0705400
Igniter Lead
1
BOS 01458
Lock Nut
2
393 389
S00132
Main Injector
1
BOS 01160
Copper washer
1
8
395 945
1000-0700570
Piezo Unit
1
9
230 328
1000-2500075
Phial Retaining Plug
1