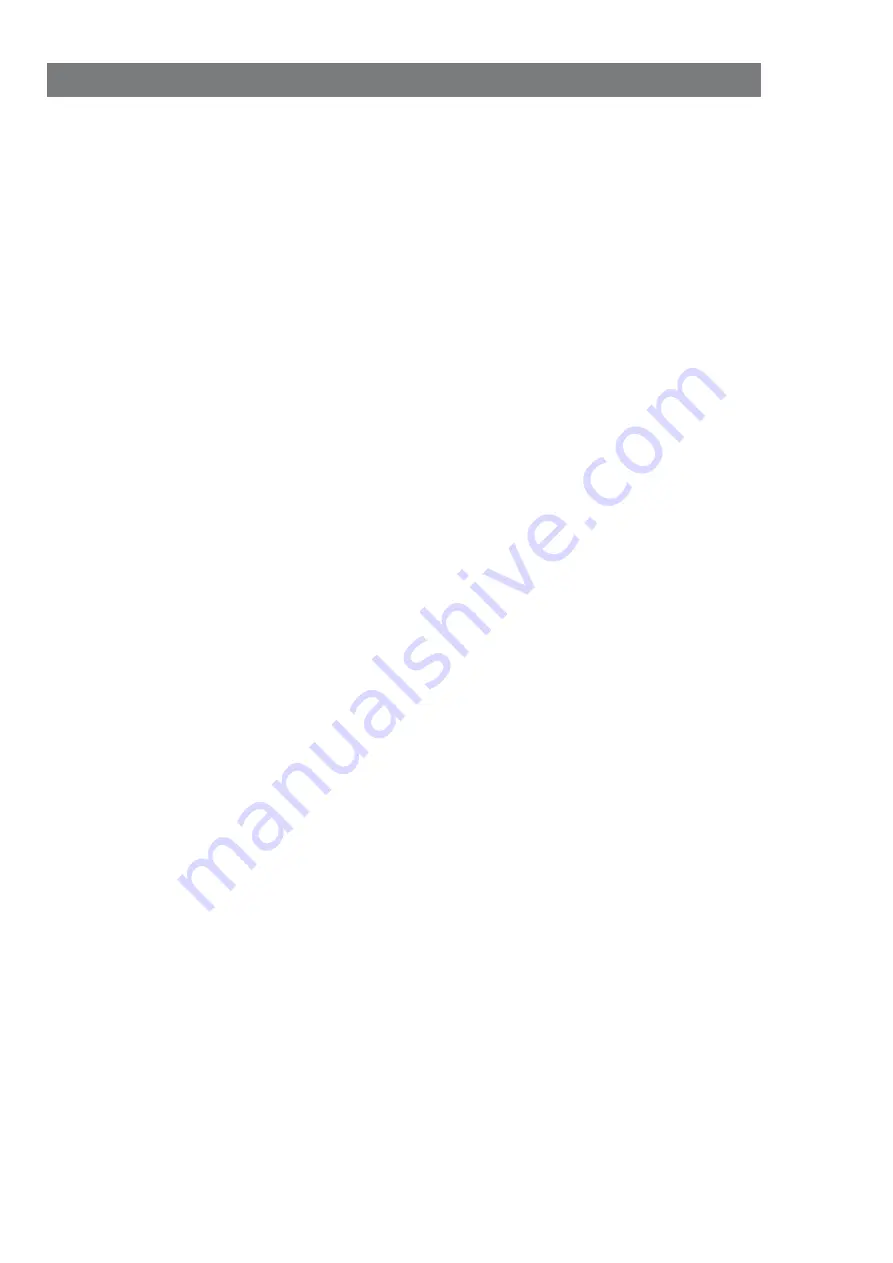
www.johnsonandstarley.co.uk
14
12
8.
MAINTENANCE
IMPORTANT: Ensure gas and electricity supplies are isolated before commencing any maintenance or replacement of
components. After completion of any maintenance, always test for gas soundness and carry out a complete functional test
of the appliance in accordance with Commissioning Instructions at Sect 6.1 to 6.8 inclusive.
8.1
ROUTINE MAINTENANCE:
8.1.1
Operate the appliance and check for the correct function of the burner and controls.
8.1.2
Turn OFF the gas and electrical supplies to the appliance.
8.1.3
Remove the air heater front panel.
8.1.4
Remove and check the return Air Filter/Cleaner for cleanliness, remove and clean the Air Circulation fan as
detailed in para 8.7.
8.1.5
Remove the Burner and Controls Assembly as detailed in para 8.2. Inspect and clean the Main Burner and Injector
as necessary. Examine the Main Burner for cracks, including hairline cracks, exchanging the burner as necessary.
8.1.6
Inspect and clear the Pilot Burner orifice.
8.1.7
Clean the Heat Exchanger flueways by thoroughly brushing from above and below.
8.1.8
By viewing through the Fan Aperture, and using a torch or similar, examine the Heat Exchanger externally for
signs of cracks or holes, particularly around welded joints.
8.1.9
Using a torch or similar, introduce a light source into the Heat Exchanger burner aperture and upper access port,
and again examine the Heat Exchanger for signs of cracks or holes, particularly around welded joints, whilst again
viewing through the Fan Aperture.
8.1.10 Refit the Air Circulation fan, Burner and Controls Assembly, and Air Filter/Cleaner.
8.1.11 Light the appliance and note the Main Burner flame profile. If the flame profile is affected when the Air
Circulation Fan switches on, check for any air leaks between the air heater and the Base Plenum, paying particular
attention to heaters with rear Draught Diverters. Rectify any air leaks before continuing with this procedure.
8.1.12 Allow the air heater to operate for approximately 15 minutes to ensure stability, and with the Main Burner lit,
ensure that the operation of Air Circulation Fan does not affect the Main Burner flame profile.
8.2
BURNER AND CONTROL ASSEMBLY REMOVAL:
8.2.1
Ensure that the Gas and Electrical supplies are switched OFF
8.2.2
Remove the appliance lower front door.
8.2.3
Disconnect the Igniter at the Piezo Unit.
8.2.4
Disconnect the Multifunctional Control electrical connections.
8.2.5
Disconnect the gas supply by breaking the union at the input side of the Multifunctional Control.
8.2.6
Whilst supporting the Burner and Control Assembly, remove 2 x Burner Assembly fixing screws and withdraw the
Burner and Control Assembly.
8.2.7
Refit the Burner and Control Assembly in reverse order, ensuring that the guide plates on the end of each burner
arm engage in the slots at the rear of the Heat Exchanger, and that the Spillage Baffle above the Burner and
Controls Assembly contacts the top of each burner arm.
8.3
BURNER AND CONTROL ASSEMBLY CLEANING:
8.3.1
Remove the Burner and Controls Assembly as detailed in 8.2.
8.3.2
Clean the burner thoroughly both inside and out with a soft brush.
DO NOT ENLARGE, DISTORT OR
DAMAGE BURNER HOLES
.
8.3.3
Reassemble in reverse order.
8.4
MAIN INJECTORS REMOVAL, CLEANING AND REPLACEMENT:
8.4.1
Remove the Burner and Controls Assembly as detailed in 8.2
8.4.2
Unscrew the 3 x Main Injectors, and 1 x Cross Lighter Injector from their housings.
8.4.3
Clean as necessary.
DO NOT ENLARGE, DISTORT OR DAMAGE MAIN INJECTOR HOLES.
8.4.4
If the injectors are to be replaced, ensure that they are correctly marked, referring to the Data Badge for details.
8.4.5
Refit or replace injectors in reverse order.
f.
Fan runs for excessive
i.
Fan Delay Control set incorrectly.
Check for correct settings.
period or operates
intermittently after
main burner shuts down.
g.
Noisy operation.
i.
Gas pressure too high.
Check burner pressure setting.
ii. Noisy fan motor.
Replace fan assembly.
iii. Fan speed setting too high.
Adjust fan speed.
MODAIRFLOW models:
h.
Incorrect operation
Fault related to Modairflow
Consult diagnostic chart and follow
of fan or main burner.
Control system (refer to pages 18-22) recommended procedure.
Non-MODAIRFLOW models:
j.
Pilot alight but main
i.
Mains electrical supply not
Check mains supply.
burner not igniting.
connected to heater.
ii. Controls not demanding heat
Check that time control and room thermostat
are operating correctly.
iii. 3A fuse failed.
Replace. If failure occurs again, check
wiring for short circuits.
iv. Loose connection to room thermo-
Check connections.
stat, Limit Switch, Multifunctional
control lead, Time Control, or
transformer.
v. Transformer open circuit.
Check with test meter and replace transformer
(Modairflow) or electrical assembly (non-
Modairflow).
vi. Multifunctional Control faulty.
Replace Multifunctional Control.
vii. Limit Switch faulty.
Short circuit switch and replace if necessary.
viii. Room thermostat or external
Fit temporary loop in heater thermostat
wiring faulty.
socket. If heater ignites, external circuit
or room thermostat is faulty.
ix. TTB Faulty
Check TTB and wiring for open circuit.
17
8. MAINENANCE
Summary of Contents for 42-451-15
Page 25: ...25 Sales Spares Replacement Help Line 01604 762881 Fig 5b Non MODAIRFLOW CIRCUIT DIAGRAM...
Page 26: ...www johnsonandstarley co uk 26 12 FUNCTIONAL DIAGRAMS Fig 6a Non MODAIRFLOW FUNCTIONAL DIAGRAM...
Page 27: ...27 Sales Spares Replacement Help Line 01604 762881 Fig 6b Non MODAIRFLOW FUNCTIONAL DIAGRAM...
Page 28: ...www johnsonandstarley co uk 28 13 DIMENSIONS Fig 7 HI SPEC J90 DIMENSIONS...
Page 29: ...29 Sales Spares Replacement Help Line 01604 762881 14 NOTES...