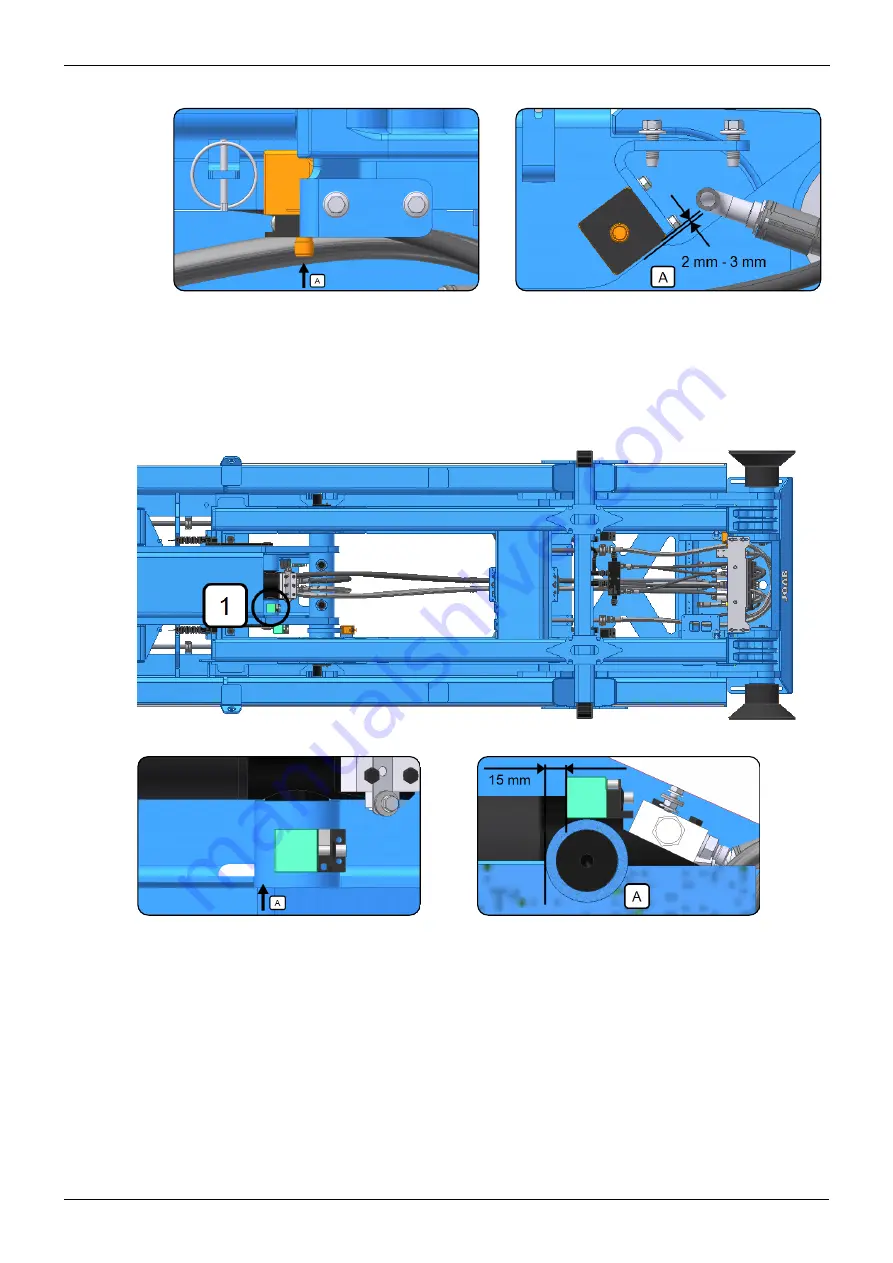
14
4:5
Inspect the ultra sonic sensor for the extending-section, where applicable. Make sure
that it is positioned correctly and free from damage.
NOTE:
This is optional equipment. It is not standard.
4:6
Verify that the ultra-sonic sensor functions correctly and that it stops the extending-sec-
tion. To do this, follow the procedure below:
1. Operate the hook-lift and tip it up, in tip mode.
2. Operate the extending section and fully retract it (move it inwards). The ultra-
sonic sensor should detect the extending section moving towards it and even-
tually signal for the extending-section to be stopped, approximately 300 mm
from its end point. This ensures that the centre-lock is not activated.
Service Instruction: EcoDrive | 13301 Edition 1b | 2019-02-31
Group 4 – Inspection and Adjustment
Summary of Contents for EcoDrive Hook-Lift L
Page 2: ...ii Service Instruction EcoDrive 13301 Edition 1b 2019 02 31 ...
Page 4: ...iv Service Instruction EcoDrive 13301 Edition 1b 2019 02 31 Table of Contents ...
Page 6: ...vi Service Instruction EcoDrive 13301 Edition 1b 2019 02 31 Introduction ...
Page 10: ...4 Service Instruction EcoDrive 13301 Edition 1b 2019 02 31 Group 1 Replace Service Components ...
Page 32: ...26 Service Instruction EcoDrive 13301 Edition 1b 2019 02 31 Group 4 Inspection and Adjustment ...
Page 34: ...28 Service Instruction EcoDrive 13301 Edition 1b 2019 02 31 Group 5 Lubrication ...
Page 42: ...36 Service Instruction EcoDrive 13301 Edition 1b 2019 02 31 Appendix 2 CBW User Interface ...
Page 45: ...39 Service Instruction EcoDrive 13301 Edition 1b 2019 02 31 Contact Information ...