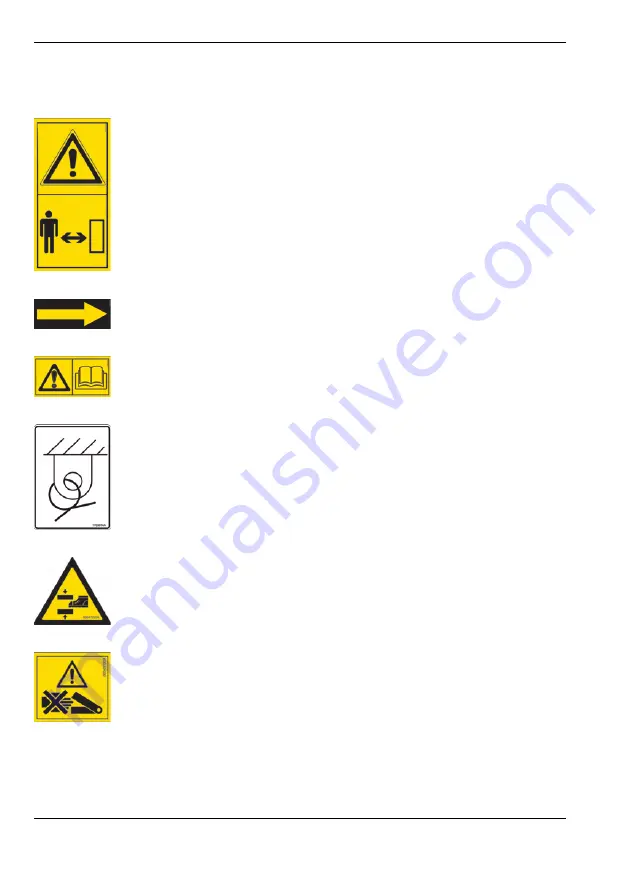
36
Boom
Lift
Models X17JPLUS
TECHNICAL
INFORMATIONS
MUX17JP021602
Decals
description
Warning
keep
safe
distance
Sense
of
moving
undercarriage
defined
as
the
direction
forward.
Obligation
to
read
the
manual
before
use
of
machine.
Fixing
point
for
transport
indicates
correct
fixing
point
for
transport
of
the
machine.
Crushing
hazard
feet
indicates
areas
where
there
is
a
danger
of
cru
‐
shing
lower
limbs
for
the
operator.
Crushing
hazard
person
indicates
areas
where
there
is
a
danger
of
crushing
upper
limbs
for
the
operator.
Summary of Contents for X17JPLUS
Page 2: ......
Page 8: ...MUX17JP021602 6 Boom Lift Models X17JPLUS ...
Page 34: ...32 Boom Lift Models X17JPLUS TECHNICAL INFORMATIONS MUX17JP021602 ...
Page 162: ...160 Boom Lift Models X17JPLUS MAINTENANCE MUX17JP021602 ...
Page 192: ...190 Boom Lift Models X17JPLUS WIRING DIAGRAM MUX17JP021602 16 WIRING DIAGRAM ...
Page 193: ...WIRING DIAGRAM 191 MUX17JP021602 Boom Lift Models X17JPLUS Fig 172 Petrol ...
Page 194: ...192 Boom Lift Models X17JPLUS WIRING DIAGRAM MUX17JP021602 Fig 173 Diesel ...
Page 195: ...WIRING DIAGRAM 193 MUX17JP021602 Boom Lift Models X17JPLUS Fig 174 Lithium ...
Page 197: ...WIRING DIAGRAM 195 MUX17JP021602 Boom Lift Models X17JPLUS Worldwide locations ...
Page 198: ...196 Boom Lift Models X17JPLUS WIRING DIAGRAM MUX17JP021602 ...
Page 199: ......