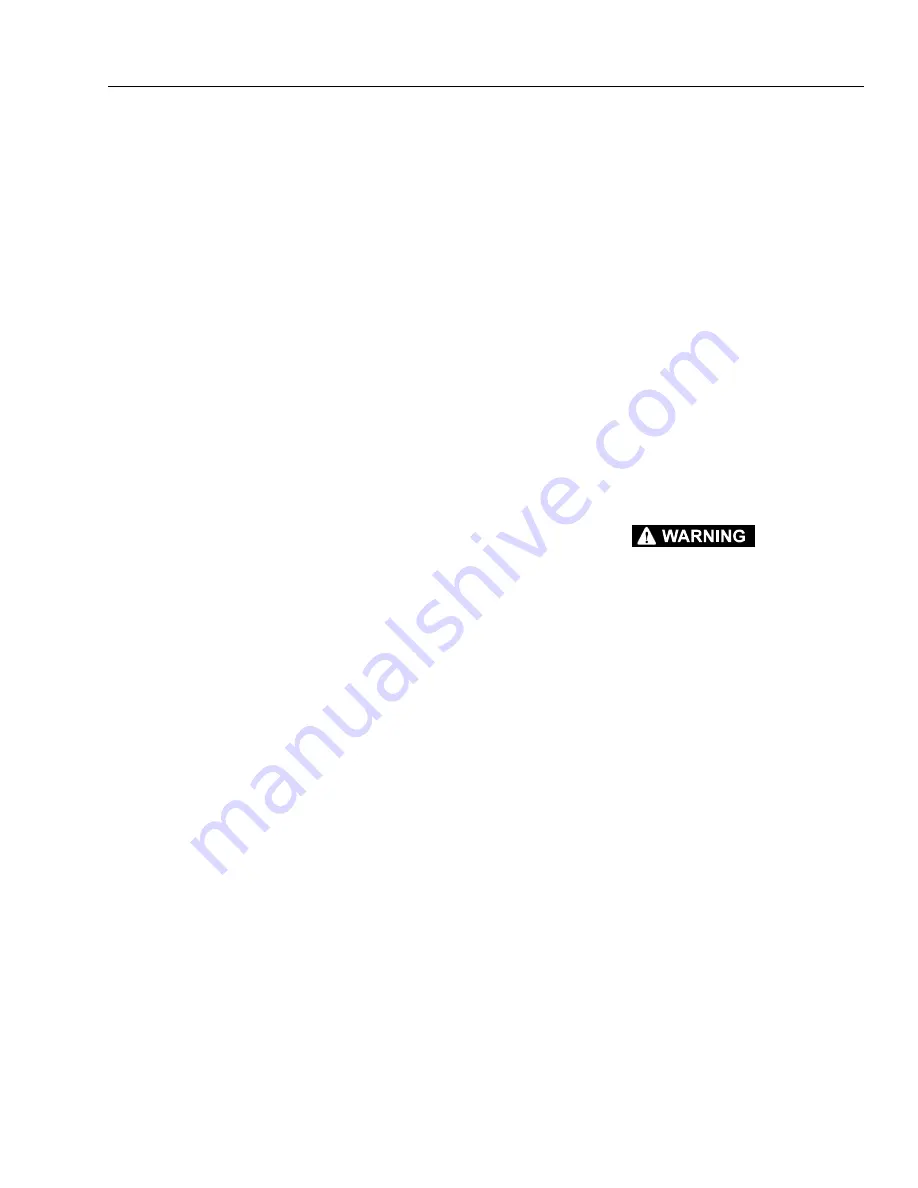
SECTION 3 - CHASSIS & TURNTABLE
3121234
3-1
SECTION 3. CHASSIS & TURNTABLE
3.1
TIRES & WHEELS
Tire Inflation
The air pressure for pneumatic tires must be equal to the
air pressure that is stenciled on the side of the JLG product
or rim decal for safe and proper operational characteristics.
Tire Damage
For pneumatic tires, JLG Industries, Inc. recommends that
when any cut, rip, or tear is discovered that exposes sidewall or
tread area cords in the tire, measures must be taken to remove
the JLG product from service immediately. Arrangements
must be made for replacement of the tire or tire assembly.
For polyurethane foam filled tires, JLG Industries, Inc. recom-
mends that when any of the following are discovered, mea-
sures must be taken to remove the JLG product from service
immediately and arrangements must be made for replace-
ment of the tire or tire assembly.
• A smooth, even cut through the cord plies which exceeds
3 in. (7.5 cm) in total length.
• Any tears or rips (ragged edges) in the cord plies which
exceeds 1 in. (2.5 cm) in any direction.
• Any punctures which exceed 1 in. in diameter.
• Any damage to the bead area cords of the tire.
If a tire is damaged but is within the above noted criteria, the
tire must be inspected on a daily basis to ensure the damage
has not propagated beyond the allowable criteria.
Tire Replacement
JLG recommends a replacement tire be the same size, ply and
brand as originally installed on the machine. Please refer to the
JLG Parts Manual for the part number of the approved tires for
a particular machine model. If not using a JLG approved
replacement tire, we recommend that replacement tires have
the following characteristics:
• Equal or greater ply/load rating and size of original.
• Tire tread contact width equal or greater than original.
• Wheel diameter, width, and offset dimensions equal to the
original.
• Approved for the application by the tire manufacturer
(including inflation pressure and maximum tire load).
Unless specifically approved by JLG Industries Inc. do not
replace a foam filled or ballast filled tire assembly with a pneu-
matic tire. When selecting and installing a replacement tire,
ensure that all tires are inflated to the pressure recommended
by JLG. Due to size variations between tire brands, both tires
on the same axle should be the same.
Wheel Replacement
The rims installed on each product model have been designed
for stability requirements which consist of track width, tire
pressure, and load capacity. Size changes such as rim width,
center piece location, larger or smaller diameter, etc., without
written factory recommendations, may result in an unsafe
condition regarding stability.
Wheel Installation
It is extremely important to apply and maintain proper wheel
mounting torque.
WHEEL NUTS MUST BE INSTALLED AND MAINTAINED AT THE PROPER TORQUE
TO PREVENT LOOSE WHEELS, BROKEN STUDS, AND POSSIBLE DANGEROUS
SEPARATION OF WHEEL FROM THE AXLE. BE SURE TO USE ONLY THE NUTS
MATCHED TO THE CONE ANGLE OF THE WHEEL.
Tighten the lug nuts to the proper torque to prevent wheels
from coming loose. Use a torque wrench to tighten the fasten-
ers. If you do not have a torque wrench, tighten the fasteners
with a lug wrench, then immediately have a service garage or
dealer tighten the lug nuts to the proper torque. Over-tighten-
ing will result in breaking the studs or permanently deforming
the mounting stud holes in the wheels. The proper procedure
for attaching wheels is as follows:
1.
Tighten all nuts by hand to prevent cross threading. DO
NOT use a lubricant on threads or nuts.
Summary of Contents for 680S
Page 2: ......
Page 52: ...SECTION 2 GENERAL 2 14 3121234 NOTES...
Page 55: ...SECTION 3 CHASSIS TURNTABLE 3121234 3 3 This page left blank intentionally...
Page 89: ...SECTION 3 CHASSIS TURNTABLE 3121234 3 37 Figure 3 28 Assembly Tools Seal Pressing...
Page 139: ...SECTION 3 CHASSIS TURNTABLE 3121234 3 87 Figure 3 62 Swing Hub Prior to SN 0300134352...
Page 143: ...SECTION 3 CHASSIS TURNTABLE 3121234 3 91 Figure 3 64 Swing Brake...
Page 205: ...SECTION 3 CHASSIS TURNTABLE 3121234 3 153 This page left blank intentionally...
Page 208: ...SECTION 3 CHASSIS TURNTABLE 3 156 3121234 Figure 3 91 Generator Electrical Circuit Diagram...
Page 224: ...SECTION 3 CHASSIS TURNTABLE 3 172 3121234 Figure 3 103 EMR 2 Engine Side Equipment...
Page 225: ...SECTION 3 CHASSIS TURNTABLE 3121234 3 173 Figure 3 104 Deutz EMR 2 Troubleshooting Flow Chart...
Page 229: ...SECTION 3 CHASSIS TURNTABLE 3121234 3 177 Figure 3 108 EMR 2 Engine Plug Pin Identification...
Page 230: ...SECTION 3 CHASSIS TURNTABLE 3 178 3121234 Figure 3 109 EMR 2 Vehicle Plug Pin Identification...
Page 231: ...SECTION 3 CHASSIS TURNTABLE 3121234 3 179 Figure 3 110 EMR2 Fault Codes Sheet 1 of 5...
Page 232: ...SECTION 3 CHASSIS TURNTABLE 3 180 3121234 Figure 3 111 EMR2 Fault Codes Sheet 2 of 5...
Page 233: ...SECTION 3 CHASSIS TURNTABLE 3121234 3 181 Figure 3 112 EMR2 Fault Codes Sheet 3 of 5...
Page 234: ...SECTION 3 CHASSIS TURNTABLE 3 182 3121234 Figure 3 113 EMR2 Fault Codes Sheet 4 of 5...
Page 235: ...SECTION 3 CHASSIS TURNTABLE 3121234 3 183 Figure 3 114 EMR2 Fault Codes Sheet 5 of 5...
Page 264: ...SECTION 3 CHASSIS TURNTABLE 3 212 3121234 NOTES...
Page 285: ...SECTION 4 BOOM PLATFORM 3121234 4 21 This page left blank intentionally...
Page 333: ...SECTION 4 BOOM PLATFORM 3121234 4 69 Figure 4 25 Load Sensing Device...
Page 336: ...SECTION 4 BOOM PLATFORM 4 72 3121234 NOTES...
Page 416: ...SECTION 5 BASIC HYDRAULICS INFORMATION SCHEMATICS 5 80 3121234 NOTES...
Page 423: ...SECTION 6 JLG CONTROL SYSTEM 3121234 6 7 Figure 6 2 ADE Block Diagram...
Page 480: ...SECTION 6 JLG CONTROL SYSTEM 6 64 3121234 NOTES...
Page 528: ...SECTION 7 BASIC ELECTRICAL INFORMATION SCHEMATICS 7 48 3121234 NOTES...
Page 529: ......