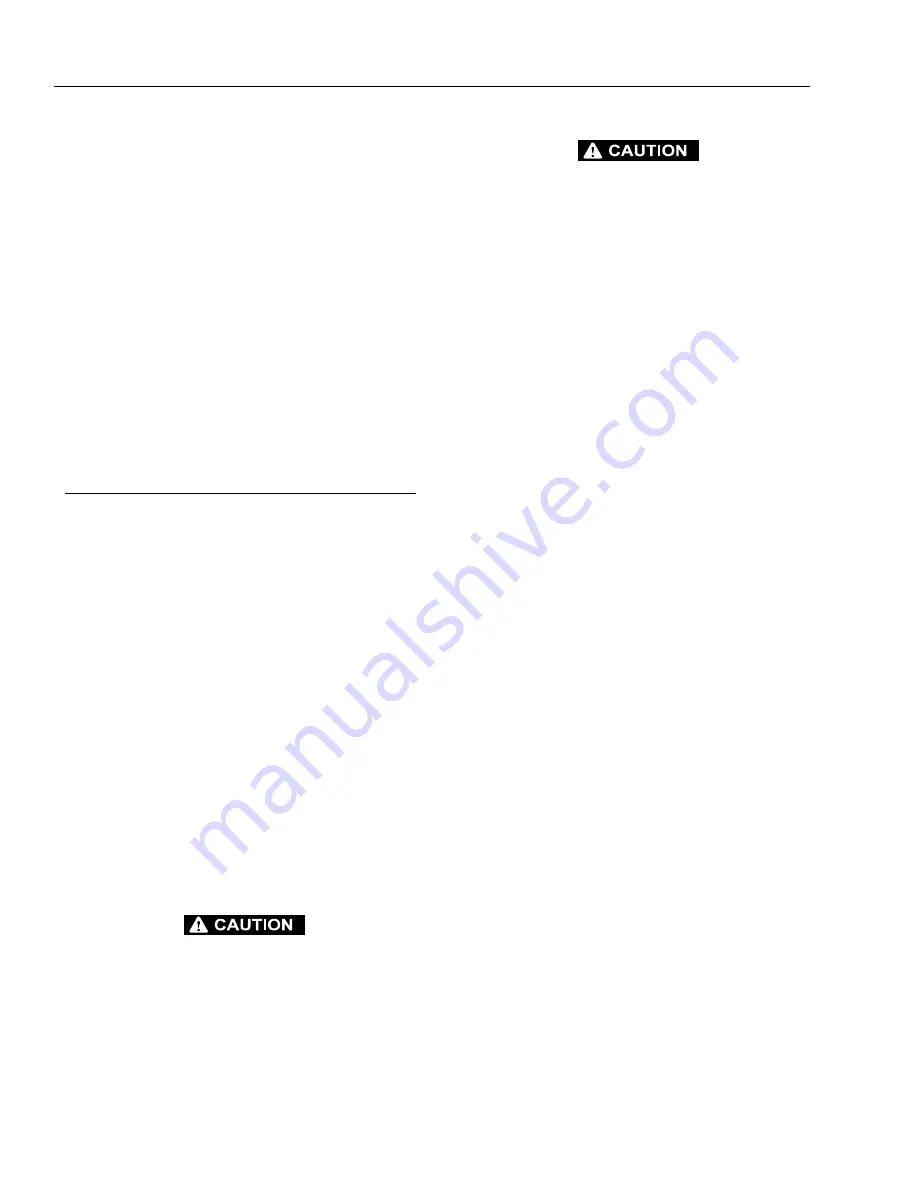
SECTION 2 - PROCEDURES
2-18
– JLG Sizzor –
3120791
14.
Assemble the bearing cup into the bearing bore of
the axle housing. Ensure the cup backface is seated
firmly against the bearing seat of the housing.
15.
Install the axle shaft into the axle housing, taking
care not to damage the seal lip and bearing rollers.
16.
Line up the holes of the axle shaft retainer with the
mounting holes in the end of the axle housing, then
push the axle shaft into the housing as far as it will
go.
17.
Install the bolts and nuts in the mounting holes of
the axle shaft retainer plate and tighten by hand.
Using a suitable speed wrench, tighten the nuts to
approximately 15 ft. lb. (20 Nm).
18.
Using a suitable torque wrench (Dana part no. C-
524-A), tighten the nuts to a final torque of 25-35 ft.
lb. (34-47 Nm).
Carrier Section
NOTE: If it becomes necessary to disassemble any parts
inside the carrier, it is suggested that the entire axle
be removed from the scissor lift and held tight in a
stand or rack.
Carrier Disassembly
1.
Remove the drain plug and drain the lubricant from
the carrier housing.
2.
Remove the cover plate screws, cover plate, and
cover plate gasket. Discard the old gasket. Tip the
carrier housing to allow lubricant to drain com-
pletely. Clean the cover face of the carrier, making
sure that it is free from any nicks and any particles
left by the old gasket.
3.
Remove the screws securing the bearing caps to the
carrier housing. Note the mating letters stamped on
the caps and the carrier. At the time of assembly,
the caps are to be assembled exactly as removed.
Letters or numbers are in horizontal and vertical
positions.
BEFORE REMOVING THE DIFFERENTIAL CASE AND RING GEAR,
ENSURE THE AXLE SHAFTS ARE PULLED OUT FAR ENOUGH
FOR CLEARANCE TO REMOVE THE DIFFERENTIAL.
4.
Mount a suitable spreader (Dana part no. D-113)
and a dial indicator (Dana part no. D-128) to the car-
rier housing. While monitoring the dial indicator,
spread the housing slightly to facilitate removal of
the differential case.
DO NOT SPREAD THE HOUSING MORE THAN 0.020 INCHES
(0.508 MM).
5.
Pry the differential case from the carrier housing with
two pry bars. Remove the spreader after the differen-
tial case has been removed. Use caution to avoid
damage to the ring and pinion. Mark on a tag which
side the bearing cups came from.
6.
Remove the differential bearing cones using a suit-
able puller (Dana part no. DD-914-9P). Wire the
shims, bearing cup and bearing cone together. Iden-
tify which side they were removed from (ring gear
side or opposite side). If the shims are mutilated,
replace them with new shims at the time of assem-
bly. Reposition the case in the puller and remove the
remaining bearing cone.
NOTE: Bearings should be replaced whenever they are
removed.
7.
Place a few shop towels over the vise to prevent the
ring gear teeth from being nicked after it is free from
the differential case. Place the differential case in the
vise. Remove the ring gear screws. Tap the ring gear
with a rawhide hammer to free it from the case.
Remove the case and ring gear from the vise.
NOTE: Ring gear screws should be replaced whenever they
are removed.
8.
Replace the case in the vise and, using a small drift,
drive out the lock pin which secures the pinion mate
shaft. Remove the shaft.
9.
Inspect all parts, including all the machined surfaces
of the case itself. If excessive wear is visible on all
parts, it is suggested that the complete differential
assembly be replaced. If any one of the gears are to
be replaced,they are to be replaced as a set.
10.
Turn the nose of the carrier housing in a horizontal
position to remove the pinion nut. Hold the end yoke
with a holding wrench (Dana part no. C-3281) and
remove the pinion nut and washer.
11.
Remove the end yoke using Dana tool no. C-452. If
the yoke shows wear in the area of the seal contact,
it should be replaced.
12.
Remove the pinion by tapping it with a rawhide ham-
mer. Catch the pinion with your hand to prevent it
from falling to the ground and being damaged.
Summary of Contents for 26MRT
Page 2: ......
Page 11: ...SECTION 1 SPECIFICATIONS 3120791 JLG Sizzor 1 5 Figure 1 2 Serial Number Locations ...
Page 12: ...SECTION 1 SPECIFICATIONS 1 6 JLG Sizzor 3120791 Figure 1 3 Torque Chart ...
Page 28: ...SECTION 2 PROCEDURES 2 16 JLG Sizzor 3120791 Figure 2 16 Drive Axle Assembly ...
Page 37: ...SECTION 2 PROCEDURES 3120791 JLG Sizzor 2 25 Figure 2 20 Brake Assembly ...
Page 40: ...SECTION 2 PROCEDURES 2 28 JLG Sizzor 3120791 Figure 2 22 ADDCO Adjustments Diesel Engine ...
Page 58: ...SECTION 3 TROUBLESHOOTING 3 14 JLG Sizzor 3120791 Figure 3 5 Hydraulic Schematic Sheet 1 of 2 ...
Page 60: ...SECTION 3 TROUBLESHOOTING 3 16 JLG Sizzor 3120791 This page intentionally left blank ...
Page 61: ......