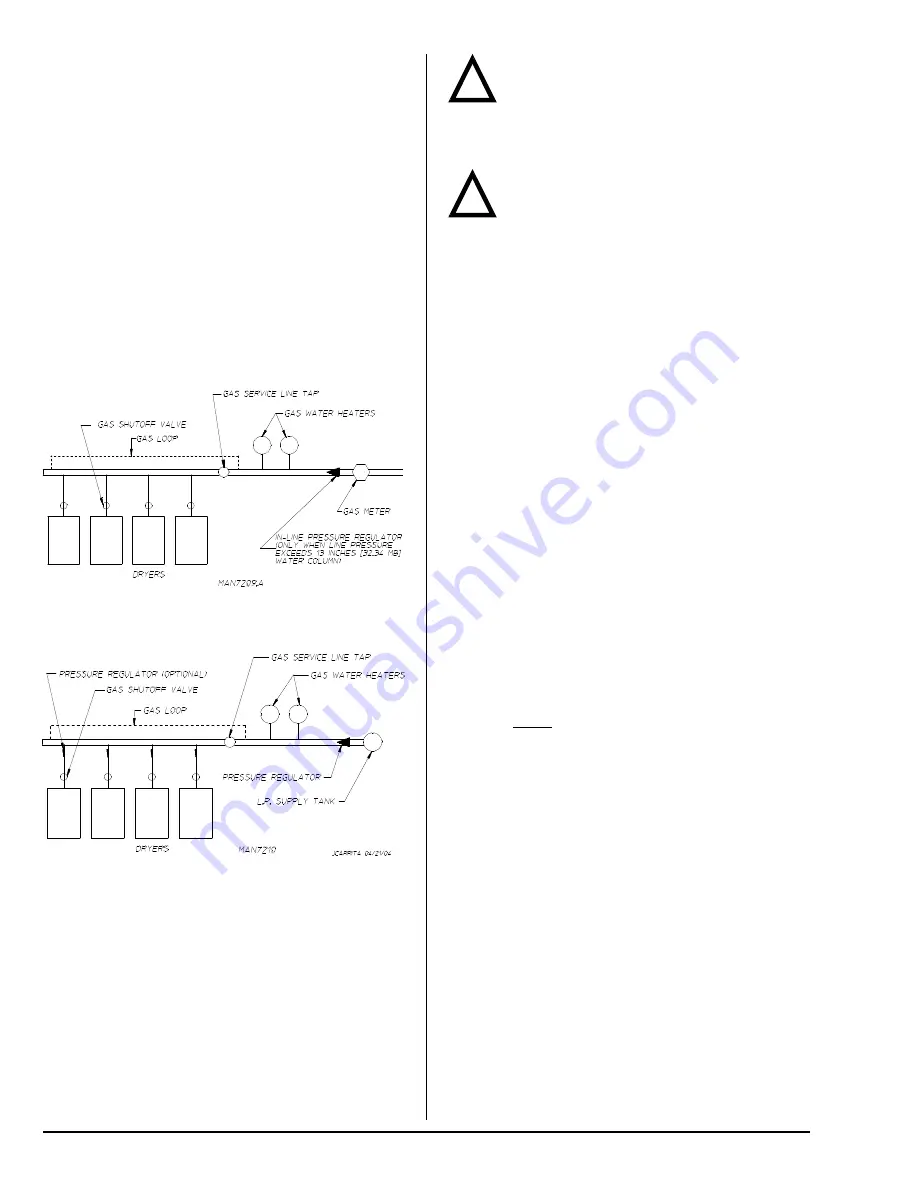
16
JLA Limited
113545 - 3
!
!
Warning
Never test for leaks with a flame!!!
Converting from One Family
of Gas to Another
Warning (CE Dryers)
This appliance must only be operated with the gas
type indicated on the dryer’s data plate. If the
appliance is converted (gas type changed), a data plate
amendment must be obtained from JLA Limited (dryer’s
serial number is required to purchase a conversion kit).
IMPORTANT:
Any burner changes or conversions must be
made by a qualified professional.
The dryers manufactured for Belgium, Luxemburg, Greece,
Estonia, Slovak Republic, Iceland, Malta, Poland and
Cyprus cannot be converted from one family of gas to
another.
Conversion from Natural Gas
to Propane or Butane Gas
The following conversion allows the dryer to be operated with
either propane, butane, or LPG. The use of gas valve kit
(P/N 140414) disables the internal regulator of the gas valve.
Therefore, the gas supply is ungoverned and an external
regulator must be provided at the source of the supply
(example L.P. tank) or the gas supply line to the dryer. The
type of L.P. kit supplied will depend on the country the dryer
is installed in.
Parts Required for Conversion:
Description
P/N
Qty
Unregulated Gas Conversion Kit**
140414
1
OR
Regulated L.P. Gas Conversion Kit***
140416
1
Burner Orifice (Injector)
*
1
L.P. Conversion Label
114515
1
*
Refer to
page 15
for orifice (injector) size.
**
Required for unregulated propane or butane only.
*** Required for regulated LPG or propane only.
Instructions
Disconnect electrical power to the dryer.
Close all shutoff valves in dryer’s gas supply line.
Open the panel located just below the loading door.
Locate the gas train and disconnect the union, three electrical
plugs, and the gas train mounting screws from the burner.
Carefully slide the gas train out of the gas train enclosure.
(The carbon ignitor located at the far end of the gas train is
very fragile.)
TYPICAL L.P. GAS INSTALLATION
Consistent gas pressure is essential at all gas connections.
It is recommended that a 3/4-inch (19.05 mm) pipe gas loop
be installed in the supply line servicing a bank of dryers. An
in-line pressure regulator must be installed in the gas supply
line (header) if the (natural) gas pressure exceeds 13.0 in
WC (32.34 mb) pressure.
A plugged tap, accessible for a pressure gauge connection,
must be installed in the main gas supply line immediately
upstream of the dryers.
IMPORTANT:
Pipe joint compounds that resist the action
of natural, L.P., and butane gases must be used.
Test all connections for leaks by brushing on a soapy
water solution (liquid detergent works well).
Piping / Connections
The dryer is provided with a 3/8” M.P.T. inlet pipe connection.
CE dryer connections will be B.S.P.T., all others will be N.P.T.
There should be a minimum 6-inch (15.24 cm) clearance
between the back guard and the first bend in the gas piping
for ease of servicing. It is recommended that a gas shutoff
valve be provided to the gas supply line of each dryer for
ease in servicing.
The size of the main gas supply line (header) will vary
depending on the distance this line travels from the gas meter
or, in the case of L.P. gas, the supply tank, other gas-operated
appliances on the same line, etc. Specific information
regarding supply line size should be determined by the gas
supplier.
NOTE:
Undersized gas supply piping can create a low or
inconsistent pressure, which will result in erratic operation
of the burner ignition system.
TYPICAL NATURAL GAS INSTALLATION
Summary of Contents for SD20
Page 24: ...Part No 113545 3 12 18 14 ...