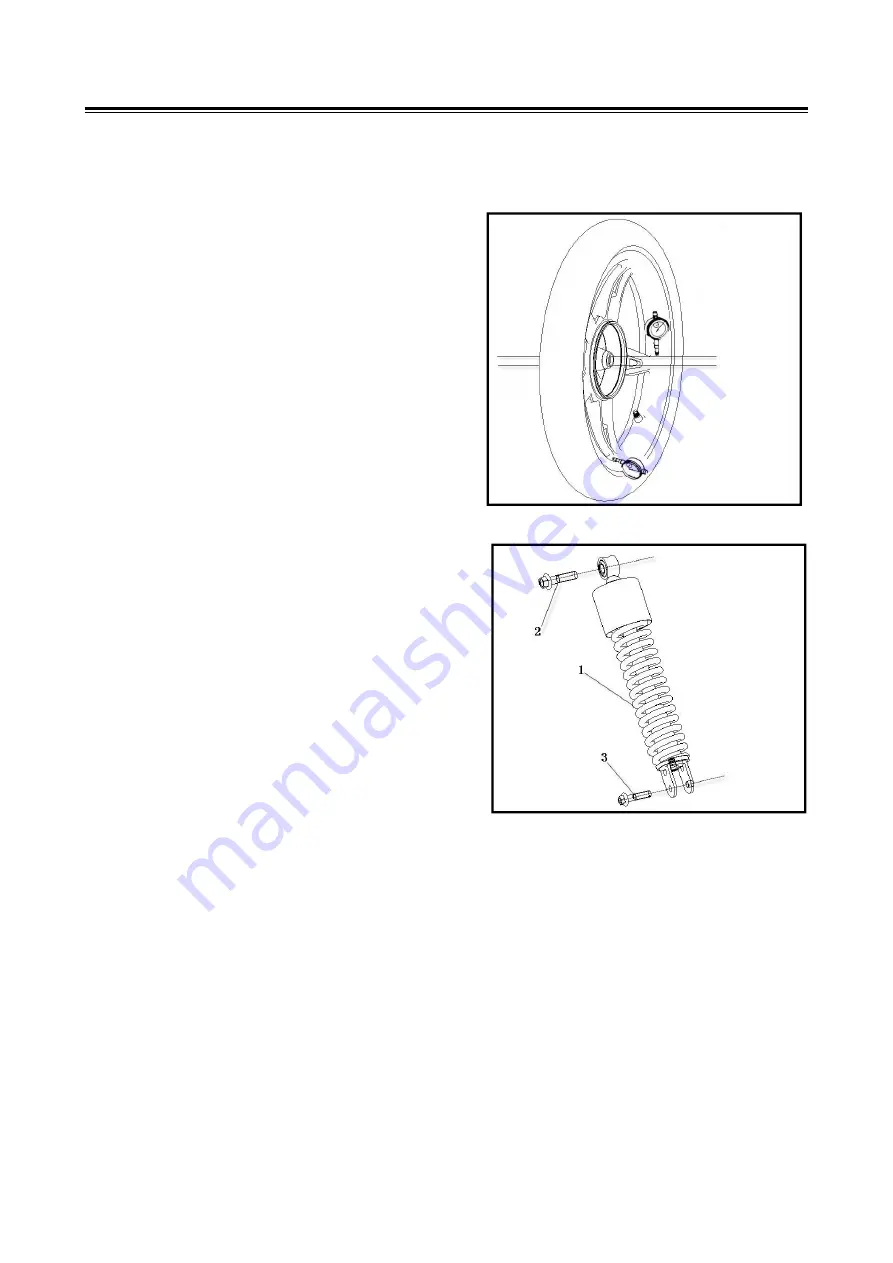
小牛电动
Niu Electric
- 35 -
Remove the motor assembly.
Remove the brake disc.
Inspection
Inspection of the motor oscillation
Manually turn the motor and measure its eccentricity
with a micrometer gauge.
Usability limit:
Vertical direction: replace it if above 2.0mm
Lateral direction: replace it if above 2.0mm
Installation
Install the rear wheel and tighten nuts in the sequence
contrary to removal.
Self-locking nuts on the motor
Torque value: 60-80 N•m
Rear shock absorber
Disassembling:
Remove the seat cushion assembly and the scooter
body assembly.
Loosen tightening bolts on top of the rear shock
absorber.
Loosen tightening bolts on bottom of the rear shock
absorber.
Remove the rear shock absorber.
Installation
Install the rear shock absorber.
Torque value for the rear shock absorber:
Tightening bolts on top:
37-44 N·m
Tightening bolts on bottom:
22-29 N·m
Installation of the rear shock absorber
Install the rear shock absorber and tighten nuts in the sequence contrary to removal.
Summary of Contents for N1S
Page 12: ...Niu Electric 9 Scooter body scooter body panel...
Page 101: ...Niu Electric 98...