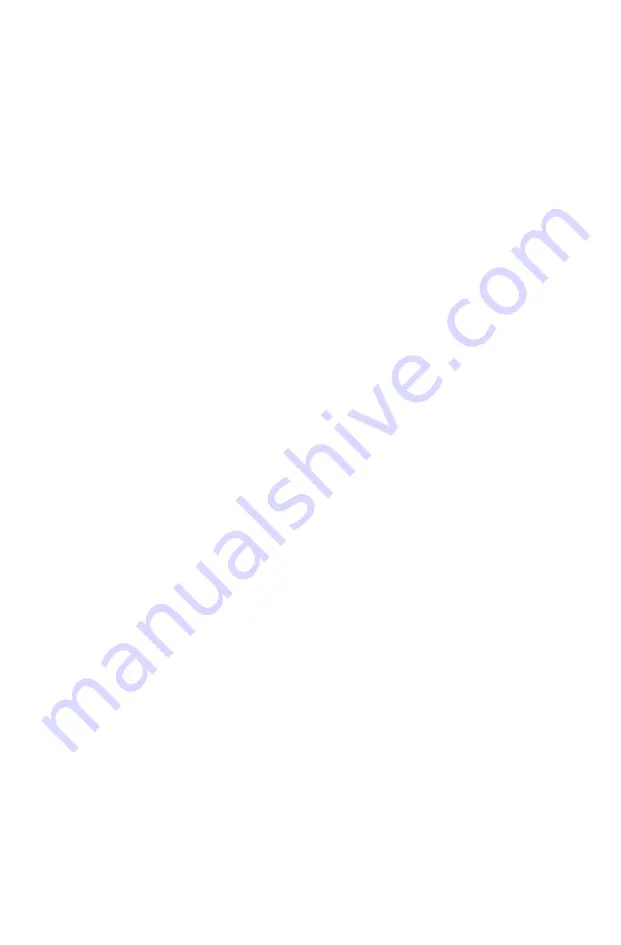
9
PI-198
December 2020
exit tube. Use anti-withdrawal device to prevent lance from exiting tube
unexpectedly.
8. The following
JETSTREAM
lance accessories are
strongly
recommended
for safer lance operation:
A.
Lance Strain Relief
- Helps prevent lance inlet end fitting failure.
B.
Lance Stinger
- Affords the operator greater control of nozzle.
Establishes a “safety zone” so operator knows when nozzle is about to
exit tube; will eliminate possibility of nozzle and lance “double back”
toward operator within large diameter pipe.
C.
Anti-withdrawal device
prevents the lance from exiting the tube
or pipe. Contact JETSTREAM for additional information regarding these
products.
9.
Use only nozzles designed for use with flex lances
(i.e. nozzle
drilled with sufficient rearward orifices so nozzle pulls lance through
tube.)
10. If lance end fittings do not have wrench flats, use properly adjusted
smooth jaw plier wrench (JS PN 64119) to connect lance to pressure
source and nozzle onto lance. Apply wrench on lance and fitting
directly
behind end fitting thread (not on fitting ferrule or collar)
when
installing nozzle on lance. Do not clamp on the lance hose itself with vise
when installing nozzle.
11. Avoid rough handling, stretching or straining of lance.
12. Never attempt to “ramrod” flex lance through blockages or to repair
or recouple lances.
13. After use, drain, coil and store lance properly. Be sure safety tags
remain intact.
RIGID TUBE CLEANING LANCES
1.
Read General Safety
section and Nozzle Safety Warnings prior to
connecting rigid lances.
2. Do not use a rigid lance with a burst rating less that 3.0 times the
pressure at which it will operate. 10,000 psi operating pressure rigid
lances must have a minimum 30,000 psi burst rating. Do not use a rigid
lance that has an unknown burst or unknown manufacturer’s operating
pressure rating.
3. Clearance between lance and tube must be sufficient to permit the
unrestricted backflow of water and debris. With tubes containing hard
deposits this clearance should be 1/8” minimum on the diameter (or
1/16” per side) of the lance. With tubes containing soft, pliable deposits