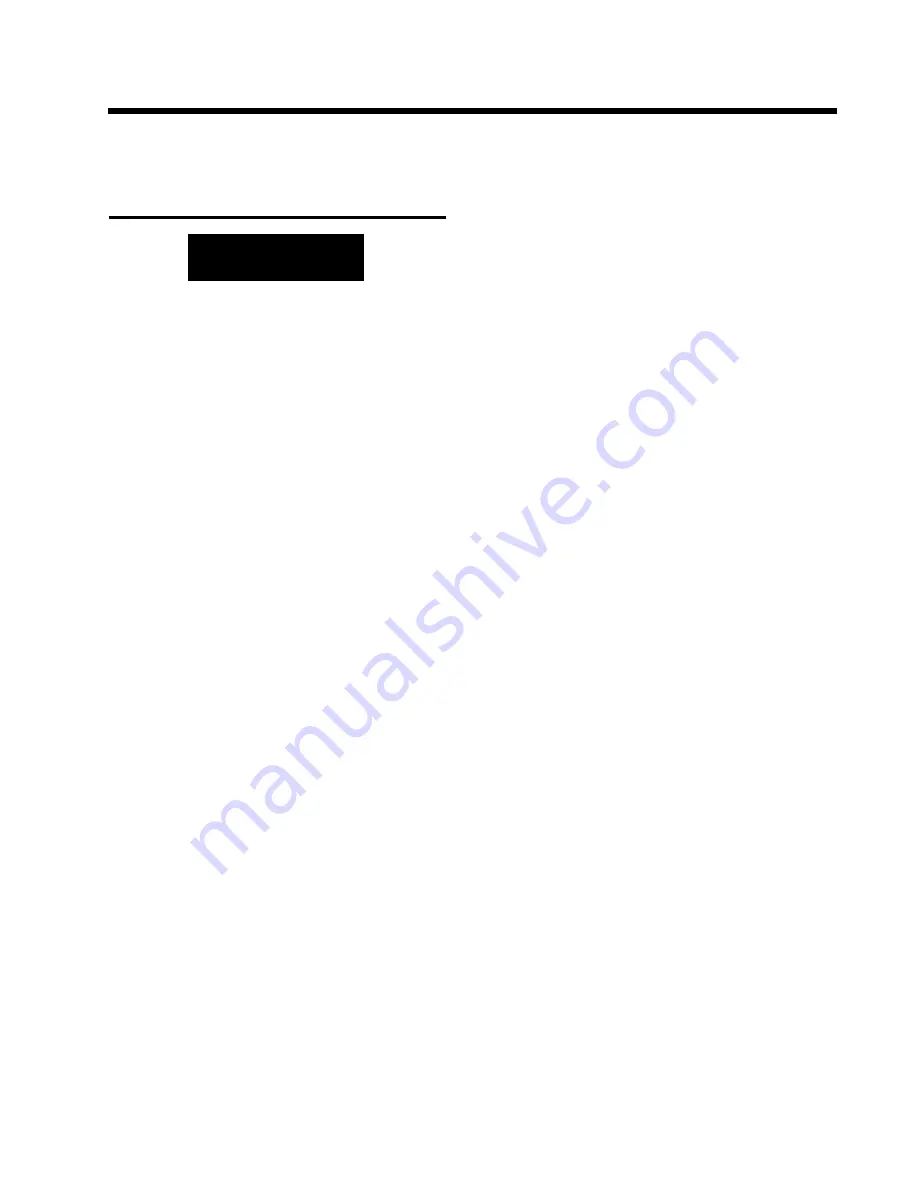
CWF-50 Cold Wire Feeder
- 1 -
Section I
Safety Precautions
CALIFORNIA PROPOSITION 65 WARNING
This product contains chemicals, including lead,
known to the state of California to cause cancer,
and birth defects or other reproductive harm.
Wash hands after use. §248224
A. Arc Welding
Arc Welding can be hazardous.
Protect your-
self and others from possible serious injury or
death. Keep children away. Pacemaker wear-
ers keep away until consulting your doctor.
In welding, as in most jobs, exposure to certain
hazards occurs. Welding is safe when precau-
tions are taken. The safety information given
below is only a summary of the more complete
safety information that will be found in the
Safety Standards listed at the end of this section.
Read and follow all Safety Standards.
Have all installation, operation, maintenance
and repair work performed only by qualified
people.
B. Electric Shock
Touching live electrical parts can cause fatal
shocks or severe burns. The electrode and work
circuit is electrically live whenever the output is
on. The input power circuit and machine internal
circuits are also live when power is on. When
using mechanized wire feed, the wire, wire reel,
drive roll housing and all metal parts touching
the welding wire are electrically live. Incorrectly
installed or improperly grounded equipment is
a hazard.
1.
Do not touch live electrical parts.
2.
Wear dry, hole-free insulating gloves and
appropriate body protection.
3.
Disconnect input power before installing or
servicing this equipment. Lockout/tagout
input power according to OSHA 29 CFR
1910.147 (see Safety Standards).
4.
Properly install and ground this equipment
according to the operation manual and
national, state and local codes.
5.
Always verify the supply ground-check and
be sure that input power cord ground wire
is properly connected to ground terminal
in disconnect box or that cord plug is con-
nected to a properly grounded receptacle
outlet.
6.
When making input connections, attach
proper grounding conductor first - double-
check connections.
7.
Frequently inspect input power cord for
damage or bare wiring. Replace cord imme-
diately if damaged - bare wiring can kill.
8.
Turn off all equipment when not in use.
9.
If earth grounding of the workpiece is required,
ground it directly with a separate cable - do not
use work clamp or work cable.
10.
Do not touch electrode if you are in contact
with the work, ground, or another electrode
from a different machine.
11. Use only well-maintained equipment.
Repair or replace damaged parts at once.
Maintain unit according to manual.
12. Wear a safety harness if working above
floor level.
13. Keep all panels and covers securely in
place.
14. Clamp work cable with good metal-to-
metal contact to workpiece or worktable
as near the weld as practical.
WARNING
Summary of Contents for CWF-50
Page 2: ...Model CWF 50 Cold Wire Feeder ii...
Page 6: ...Model CWF 50 Cold Wire Feeder vi Section VIII 21 Parts Lists 21...
Page 15: ...CWF 50 Cold Wire Feeder 9 Figure 2 Mounting Plate Dimensions...
Page 16: ...CWF 50 Cold Wire Feeder 10...
Page 19: ...CWF 50 Cold Wire Feeder 13 Figure 3 Wire Feed Accessory Kit Components...
Page 20: ...CWF 50 Cold Wire Feeder 14...
Page 22: ...CWF 50 Cold Wire Feeder 16...
Page 24: ...CWF 50 Cold Wire Feeder 18...
Page 26: ...CWF 50 Cold Wire Feeder 20...
Page 28: ...CWF 50 Cold Wire Feeder 22...
Page 30: ...CWF 50 Cold Wire Feeder 24 4 14 08 WGP 1 WIRE GUIDE POSITIONER L...
Page 34: ...CWF 50 Cold Wire Feeder 28 4 10 08 WGP 3 COMPACT WIRE GUIDE POSITIONER FOR COLD WIRE FEEDERS D...