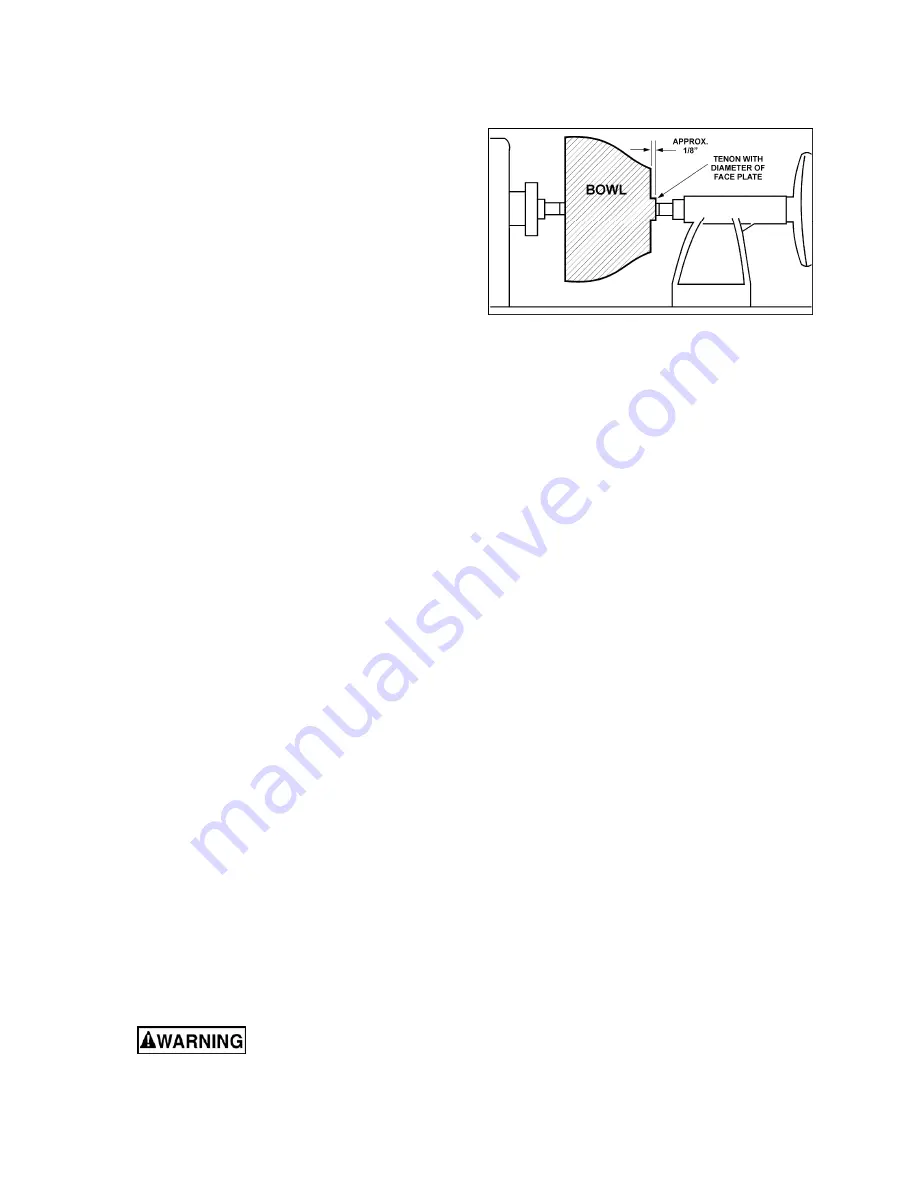
21
other gouges. Most average sized bowl work can
be accomplished with a 3/8" or 1/2" bowl gouge.
A 1/4" bowl gouge is best suited for smaller bowls
and light finishing cuts. Larger 3/4" and 1" bowl
gouges are only used for extremely large pieces.
Large domed scrapers can also be used to help
clean up the interior surfaces of bowls. A light
touch with the scraper slightly tilted will eliminate
some of the ridges occasionally left by an
inexperienced bowl gouge.
9.7
Bowl Turning Techniques
9.7.1
To Shape Outside of Bowl
1. Odd shaped burls, crotches and other irregular
shaped blanks require special preparation
before mounting in a chuck or onto a
faceplate. Remove the bark, if there is any,
from what appears to be the center of the top
of the workpiece.
2. Drive spur center into the top of the workpiece
with a mallet or dead blow hammer.
3. Slip the spur center into the headstock taper
and bring the tailstock with a live or ball
bearing center into position. Lock the tailstock
to the bed and advance the tailstock spindle in
order to seat the cup center into the
workpiece. Tighten the ram locking handle.
4. Turn workpiece by hand to ensure proper
clearance.
5. Start lathe at lowest speed and bring it up to
the maximum safe speed for the size of work
to be turned. If the machine starts to vibrate,
lower the speed until vibration stops.
6. Rough out the outside of the bowl with the 1/2"
deep fluted bowl gouge, holding the handle of
the tool firmly against your hip. For best
control, use your whole body to move the
gouge through the workpiece.
7. As the bowl takes shape, work on the bottom
(tailstock end) to accommodate attaching a
face plate.
8. Turn a short tenon (about 1/8" long) the size of
the hole in the faceplate. See Figure 9-10. This
will allow centering the workpiece when the
faceplate is attached.
(NOTE: If you plan to use a chuck, turn a
tenon of the appropriate length and diameter
to fit your chuck.)
9. Stop the lathe, remove workpiece and attach
face plate or chuck (
see section 9.6.1
"Mounting Stock"
).
The surfaces of faceplate
and workpiece should mount flush to each
other.
10. Finish turning the outside of bowl with 1/2" or
3/8" bowl gouge. Leave additional material at
base of bowl for support while turning interior.
This will be removed later.
Figure 9-10
9.7.2
To Shape Interior of Bowl
1. Stop lathe and move tailstock away. (You may
want to remove the center from the tailstock to
avoid bumping it with your elbow.)
2. Adjust tool support in front of the bowl just
below centerline, at a right angle to the lathe
ways.
3. Rotate workpiece by hand to check clearance.
4. Face off top of bowl by making a light shearing
cut across the top of workpiece, from rim to
center.
5. Place 1/2" bowl gouge on tool support at
center of the workpiece with the flute facing
top of bowl. The tool handle should be level
and pointed toward the four o'clock position, as
shown in Figure 9-11.
6. Use the left hand to control cutting edge of
gouge, while right hand swings tool handle
toward your body (Figure 9-11). The flute
should start out facing top of workpiece, and
rotate upward as it moves deeper into the bowl
to maintain a clean even curve. As the tool
goes deeper into the bowl, progressively work
out toward the rim. It may be necessary to turn
the tool support into the piece as you get
deeper into the bowl.
(NOTE: Try to make one, very light continuous
movement from the rim to the bottom of the
bowl to ensure a clean, sweeping curve
through the piece.
Should there be a few small ridges left, a light
cut with a large domed scraper can even out
the surface.)
Summary of Contents for JWL-1840DVR
Page 30: ...30 14 2 1 JWL 1840DVR Headstock Assembly Exploded View...
Page 34: ...34 14 4 1 JWL 1840DVR Controller Assembly Exploded View...
Page 36: ...36 14 5 1 JWL 1840EVS DVR Bed and Stand Assembly Exploded View...
Page 41: ...41 15 2 Schematic for JWL 1840DVR only...
Page 42: ...42...
Page 44: ...44 427 New Sanford Road LaVergne Tennessee 37086 Phone 800 274 6848 www jettools com...