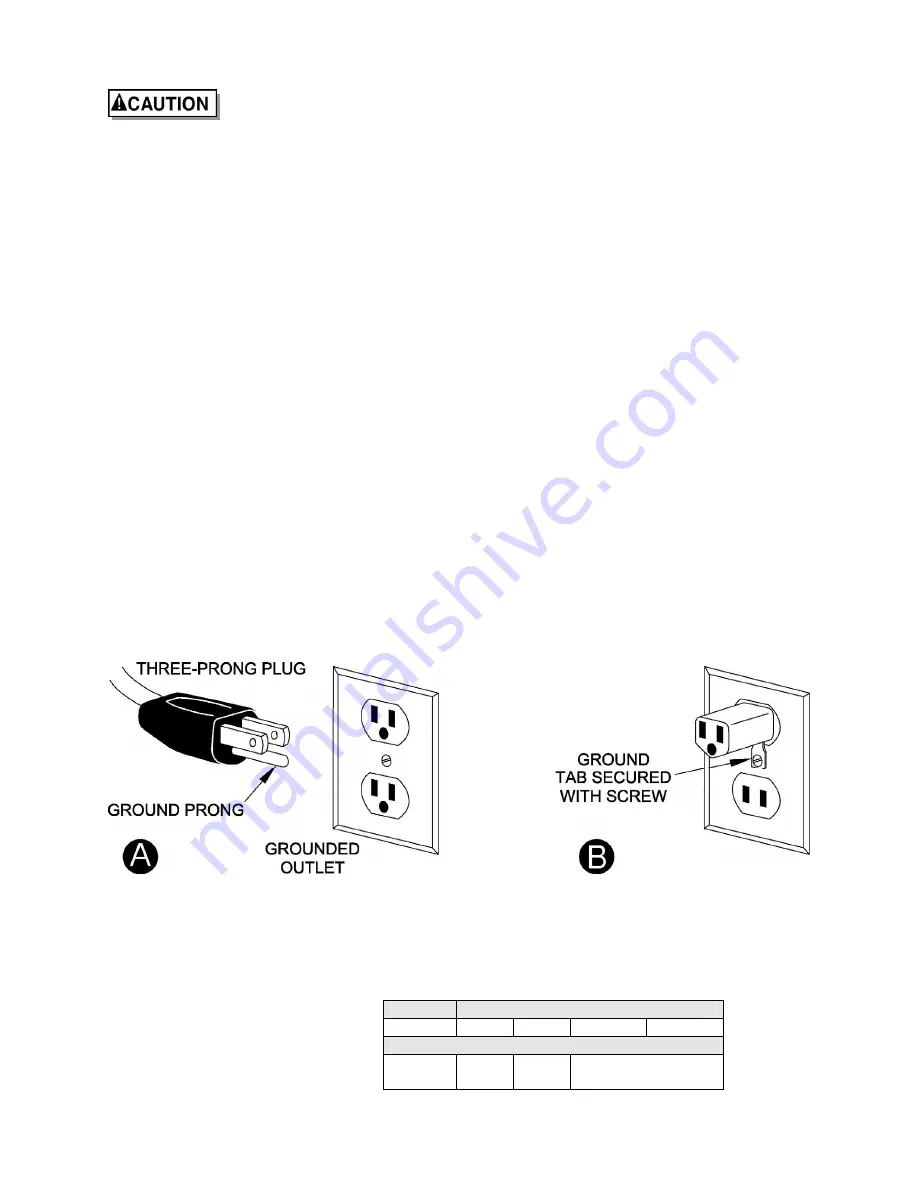
5
Grounding Instructions
This tool must be grounded while in use to protect the operator from electric
shock.
In the event of a malfunction or breakdown, grounding provides a path of least resistance for electric
current to reduce the risk of electric shock. This tool is equipped with an electric cord having an
equipment-grounding conductor and a grounding plug. The plug must be plugged into a matching outlet
that is properly installed and grounded in accordance with all local codes and ordinances.
Do not modify the plug provided. If it will not fit the outlet, have the proper outlet installed by a qualified
electrician.
Improper connection of the equipment-grounding conductor can result in a risk of electric shock. The
conductor, with insulation having an outer surface that is green with or without yellow stripes, is the
equipment-grounding conductor. If repair or replacement of the electric cord or plug is necessary, do not
connect the equipment-grounding conductor to a live terminal.
Check with a qualified electrician or service personnel if the grounding instructions are not completely
understood, or if in doubt as to whether the tool is properly grounded. Use only three wire extension cords
that have three-prong grounding plugs and three-pole receptacles that accept the tool’s plug.
Repair or replace a damaged or worn cord immediately.
115 Volt Operation (Model JWL-1642EVS only)
As received from the factory, your JWL-1642EVS is ready to run at 115-volt operation. This lathe is
intended for use on a circuit that has an outlet and a plug that looks the one illustrated in Figure A. A
temporary adapter, which looks like the adapter as illustrated in Figure B, may be used to connect this
plug to a two-pole receptacle, as shown in Figure B if a properly grounded outlet is not available. The
temporary adapter should only be used until a properly grounded outlet can be installed by a qualified
electrician.
This adapter is not applicable in Canada.
The green colored rigid ear, lug, or tab, extending
from the adapter, must be connected to a permanent ground such as a properly grounded outlet box, as
shown in Figure B.
The use of an extension cord is not recommended. However, if you must use one make sure your
extension cord is in good condition. Be sure to use one heavy enough to carry the current your machine
will draw. An undersized cord will cause a drop in the line voltage resulting in power loss and overheating.
The following table shows the correct size to use depending on the cord length needed and the
nameplate ampere rating. If in doubt, use the next heavier gauge. Remember, the smaller the gauge
number, the heavier the cord.
Volts7
Total Length of Cord in Feet
120V 25 50 100 150
AWG
12-16
Amps
14 12 Not
Recommended
Summary of Contents for JWL-1642EVS
Page 23: ...23 Stand and Bed Assembly ...
Page 25: ...25 Headstock Assembly ...
Page 28: ...28 Wiring Diagram for JWL 1642EVS ...
Page 29: ...29 Wiring Diagram for JWL 1642EVS 2 ...
Page 31: ...31 Notes ...