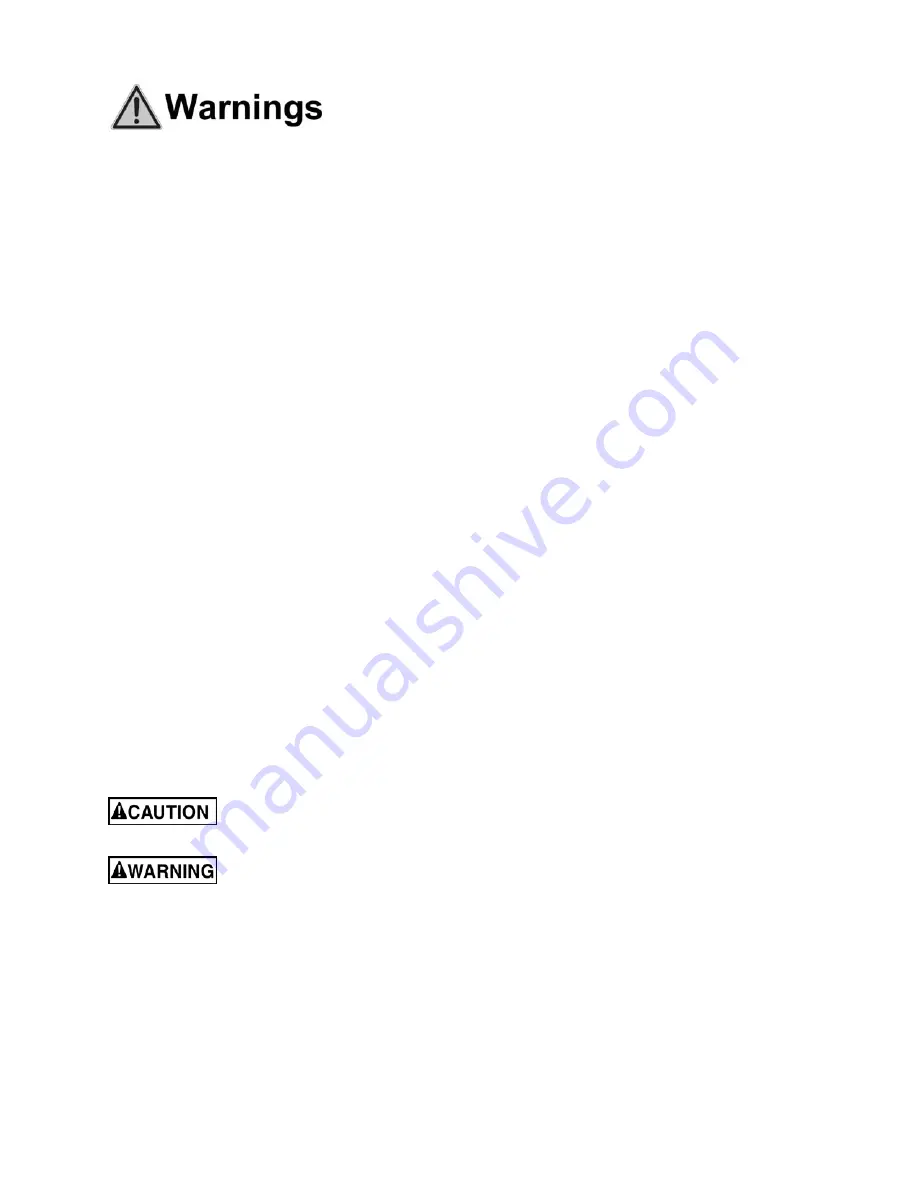
5
19. Provide for adequate space surrounding work area and non-glare, overhead lighting.
20. Keep the floor around the machine clean and free of scrap material, oil and grease.
21. Keep visitors a safe distance from the work area.
Keep children away.
22. Make your workshop child proof with padlocks, master switches or by removing starter keys.
23. Give your work undivided attention. Looking around, carrying on a conversation and “horse-play” are
careless acts that can result in serious injury.
24. Maintain a balanced stance at all times so that you do not fall into the blade or other moving parts. Do
not overreach or use excessive force to perform any machine operation.
25. Use the right tool at the correct speed and feed rate. Do not force a tool or attachment to do a job for
which it was not designed. The right tool will do the job better and safer.
26. Use recommended accessories; improper accessories may be hazardous.
27. Maintain tools with care. Keep saw blades sharp and clean for the best and safest performance.
Follow instructions for lubricating and changing accessories.
28. Make sure the work piece is held firmly against the rip fence or miter gauge as it is fed through the
blade.
29. Turn off the machine before cleaning. Use a brush or compressed air to remove chips or debris — do
not use your hands.
30. Do not stand on the machine. Serious injury could occur if the machine tips over.
31. Never leave the machine running unattended. Turn the power off and do not leave the machine until it
comes to a complete stop.
32. Remove loose items and unnecessary work pieces from the area before starting the machine.
Familiarize yourself with the following safety notices used in this manual:
This means that if precautions are not heeded, it may result in minor injury and/or
possible machine damage.
This means that if precautions are not heeded, it may result in serious injury or possibly
even death.
Summary of Contents for JWBS-14OS
Page 22: ...22 Body Assembly JWBS 14OS Band Saw ...
Page 24: ...24 Electrical Connections ...