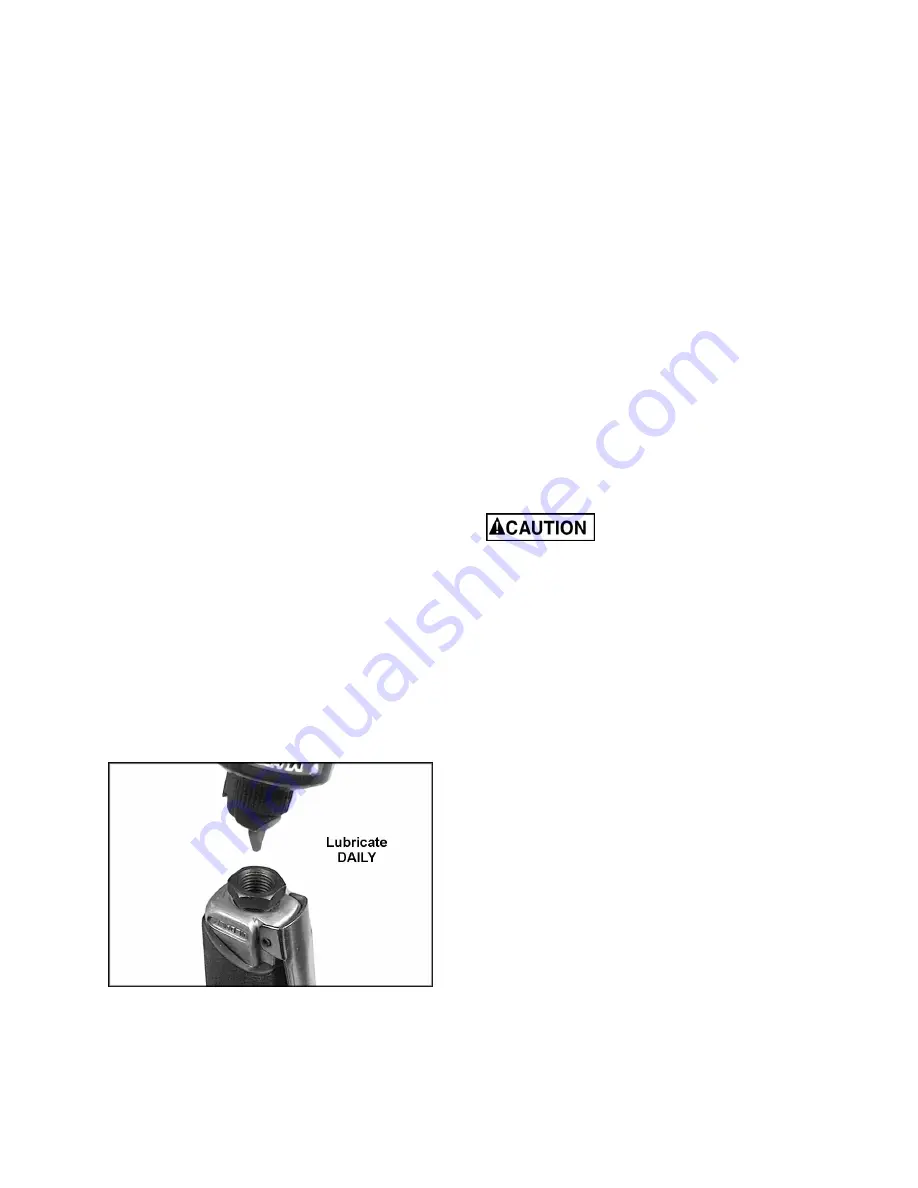
5
Unpacking
Any missing or damaged parts should be
reported to your JET
®
distributor. Read this
instruction manual thoroughly for operation,
maintenance and safety instructions.
Operation
1. The ratchet wrench must be properly
lubricated before operating. See
“Maintenance” section for lubricating
instructions.
2. Remove the protective cap from the air inlet,
and connect the air supply hose. Make sure
the air pressure is set to 90psi.
IMPORTANT:
Connecting a quick-change
coupling directly to the ratchet wrench is not
recommended, as vibration may cause the
connection to fail. Instead, add a leader
hose and install any quick-change couplings
farther down the line.
3. Install a socket on the post of the wrench
and press the trigger to operate.
Maintenance
The ratchet wrench should be lubricated daily
(or before each use) with air tool oil through the
air inlet. During continual operation, it should be
re-oiled every 1 to 2 hours. This can be done
either with an in-line oiler, or manually. If done
manually, proceed as follows:
1. Disconnect the air hose from the ratchet
wrench.
2. Place four or five drops of air tool oil* into
the air inlet (see Figure 1).
Figure 1
[*NOTE: Air tool oil not provided. It may be
purchased from your JET dealer, or is
available at most major hardware and tool
stores. SAE #10 weight oil or sewing
machine oil may be used as a substitute. Do
not use detergent oil.]
3. Re-connect the air. Run the ratchet wrench
without load for a few seconds to distribute
the oil throughout the tool.
4. When you are finished operating the ratchet
wrench, before storing it disconnect the air
hose and place 4 or 5 drops of air tool oil
into the air inlet; re-connect the air and run
the tool for a few seconds to distribute the
oil.
5. Avoid storing the ratchet wrench in very
humid locations which promotes rusting of
internal mechanisms, and always oil it
before storage.
Air Connection
1. Make sure that the air compressor supplies
clean air at the correct CFM for the ratchet
wrench.
Excess air pressure and/or
unclean air will shorten the tool’s life and
may create a hazardous situation.
2. Set air pressure to 90 psi.
3. Drain the water from the air compressor tank
daily, as well as any condensation from the
air lines. Water in the air line may enter the
tool and cause damage.
4. Change filters on the air system on a regular
basis.
5. Air line pressure should be increased
accordingly to compensate for extra long air
hoses (usually over 25 feet). Inside diameter
of the hose should be a minimum of 3/8”.
Summary of Contents for JNS-5052
Page 7: ...7 ...