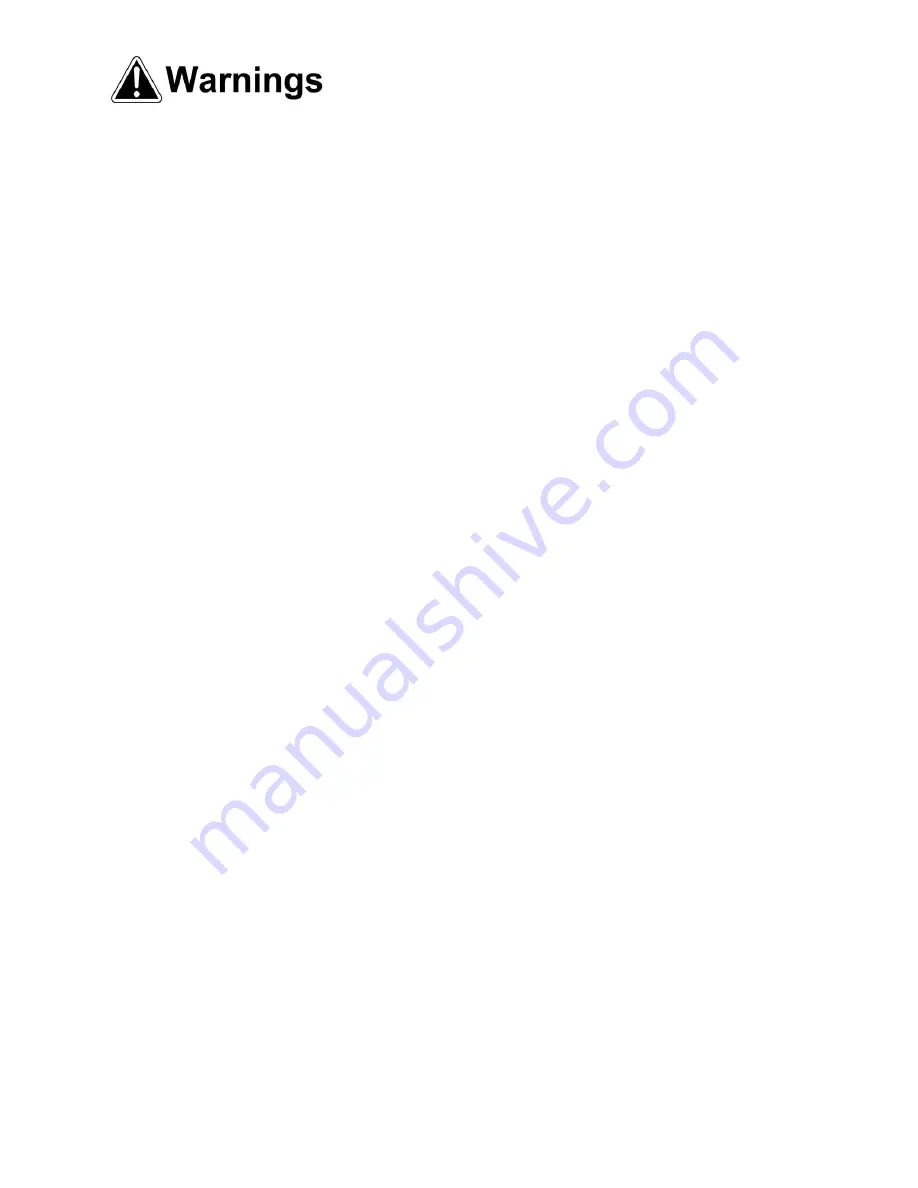
4
Warnings
1. Read and understand the entire owners manual before attempting assembly or operation.
2. Read and understand the warnings posted on the machine and in this manual. Failure to comply with
all of these warnings may cause serious injury.
3. Replace the warning labels if they become obscured or removed.
4. The cold saw is designed and intended for use by properly trained and experienced personnel only. If
you are not familiar with the proper and safe operation of a cold saw, do not use until proper training
and knowledge have been obtained.
5. Do not use this cold saw for other than its intended use. If used for other purposes, WMH Tool Group
disclaims any real or implied warranty and holds itself harmless from any injury that may result from
that use.
6. Always wear approved safety glasses/face shields while using this cold saw. Everyday eyeglasses
only have impact resistant lenses; they are not safety glasses.
7. Before operating the cold saw, remove tie, rings, watches and other jewelry, and roll sleeves up past
the elbows. Remove all loose clothing and confine long hair. Non-slip footwear or anti-skid floor strips
are recommended. Do
not
wear gloves.
8. Wear ear protectors (plugs or muffs) during extended periods of operation.
9. Some dust created by power sanding, sawing, grinding, drilling and other construction activities
contain chemicals known to cause cancer, birth defects or other reproductive harm. Some examples
of these chemicals are:
•
Lead from lead based paint.
•
Crystalline silica from bricks, cement and other masonry products.
•
Arsenic and chromium from chemically treated lumber.
10. Your risk of exposure varies, depending on how often you do this type of work. To reduce your
exposure to these chemicals, work in a well-ventilated area and work with approved safety
equipment, such as face or dust masks that are specifically designed to filter out microscopic
particles.
11. Do not operate this machine while tired or under the influence of drugs, alcohol or any medication.
12. Make certain the switch is in the
OFF
position before connecting the machine to the power supply.
13. Make certain the machine is properly grounded.
14. Make all machine adjustments or maintenance with the machine unplugged from the power source.
15. Remove adjusting keys and wrenches. Form a habit of checking to see that keys and adjusting
wrenches are removed from the machine before turning it on.
16. Keep safety guards in place at all times when the machine is in use. If removed for maintenance
purposes, use extreme caution and replace the guards immediately.
17. Make sure the cold saw is firmly placed on a secure foundation.
18. Check damaged parts. Before further use of the machine, a guard or other part that is damaged
should be carefully checked to determine that it will operate properly and perform its intended
function. Check for alignment of moving parts, binding of moving parts, breakage of parts, mounting
and any other conditions that may affect its operation. A guard or other part that is damaged should
be properly repaired or replaced.
19. Provide for adequate space surrounding work area and non-glare, overhead lighting.
20. Keep the floor around the machine clean and free of scrap material, oil and grease.
21. Keep visitors a safe distance from the work area.
Keep children away.
22. Make your workshop child proof with padlocks, master switches or by removing starter keys.
Summary of Contents for J-CK350-2
Page 17: ...17 Stand Assembly...
Page 19: ...19 Head Assembly...
Page 21: ...21 Base Assembly...
Page 23: ...23 Manual Vise Assembly...
Page 25: ...25 Guard Assembly file 03...
Page 27: ...27 CK350 Mist Coolant Assembly file 04...
Page 31: ...31 Wiring Diagram...