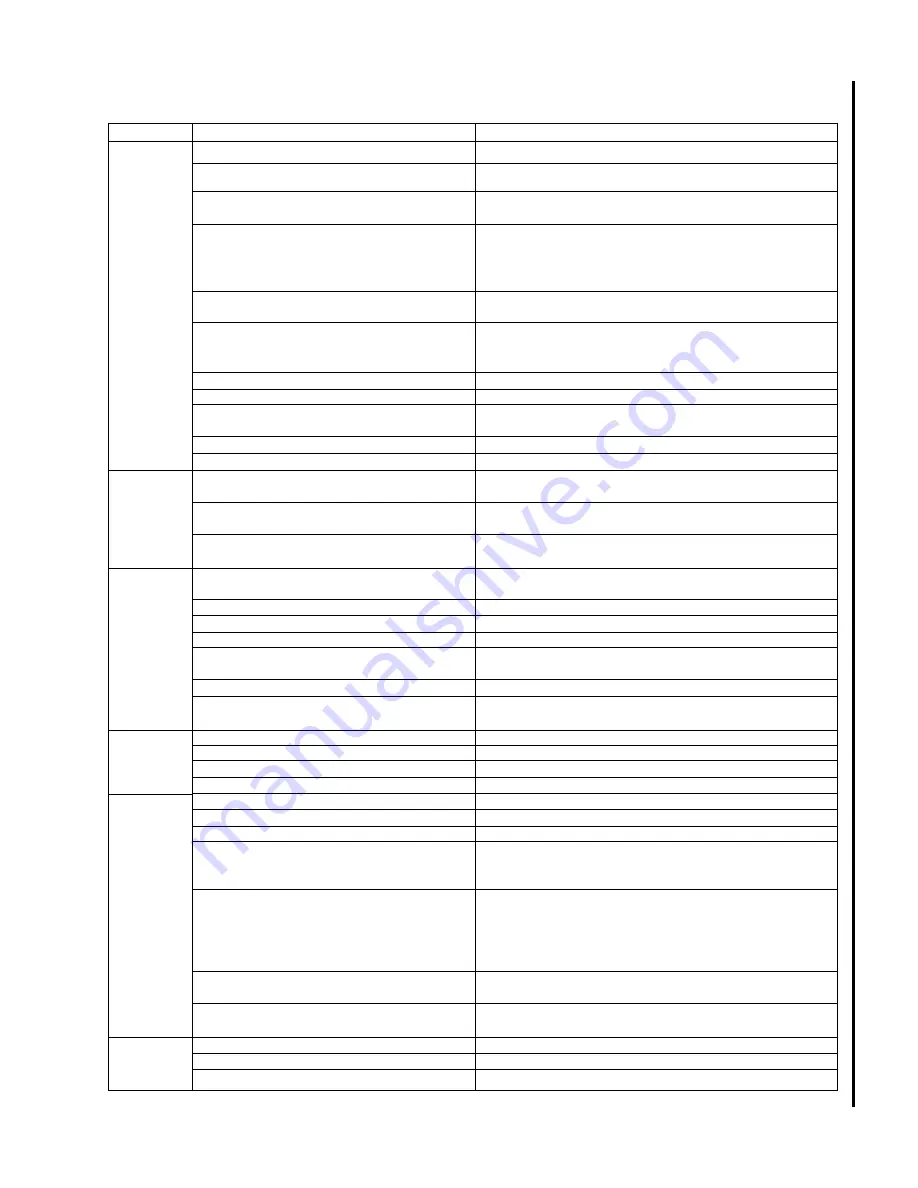
17
1. Observe chip formation to be sure cutting is efficient.
1. Adjust guide bearings according to instructions in this
manual.
1. Increase blade tension so blade does not slip on the
wheels.
1. Move guide brackets until they just clear the workpiece
while making a complete cut.
2. For small section pieces, be sure the blade is sharp
and correctly tensioned. Use less feed pressure.
1. Replace blade when it dulls.
2. Consider using a coolant, if not already used.
1. Check technical literature for recommended speeds
and blade type for material being cut -- observe chip
formation to verify efficient cutting.
1. Tighten guide bracket.
1. Check tightness of bearing seat bolt.
1. Use paper cutting method of setting blade tracking.
1. Replace bearings if worn.
1. Tighten all bolts securing wheel to arm.
1. Try one step lower speed and observe chip formation
for efficient cutting/feed rate.
1. Use finer blade. Check with suppliers for recommen-
dations for the material you are cutting.
1. Check with blade suppliers for recommendations for
exotic or unusual materials or specifications.
1. Be sure workpiece is flat on saw base.
2. Decrease feed pressure.
1. Reduce tension to just above point where blade slips.
1. Check eccentric jam nuts for tightness.
1. Check guide bearings for wear. Replace if necessary.
1. Adjust guide bearings according to instructions in this
manual.
1. Tighten bracket on saw arm.
1. Tighten bearing seat attachment screw -- adjust
bearing clearance.
1. Replace.
1. Check and adjust for proper clearance.
1. Tighten bracket to saw arm.
1. Adjust blade tracking using the paper cutting method.
1. Use blade with finer pitch.
1. Decrease feed rate -- observe chip formation to verify
efficient cutting.
1. Increase blade speed. Check technical literature or
blade or workpiece supplier for blade speed recommen-
dations.
1. Be sure vise is tight.
2. Support slender cross section or long workpieces with
appropriate in feed and out feed supports.
3. If stacking pieces in the vise, be sure all workpieces
are securely captured by the vise.
1. Use coarser blade or one with a tooth geometry more
appropriate to the workpiece being cut.
1. Always allow motor to come fully up to speed before
beginning cut.
1. Decrease blade tension to just above slip point.
1. Replace gears in transmission gearbox.
1. Check gearbox and add oil as required.
Rough
cuts
Blade
twisting
Motor
running too
hot
Feed pressure too great
Guide bearings not adjusted properly
Inadequate blade tension
Blade guides incorrectly spaced
Dull blade
Incorrect speed
Blade guide assembly loose
Blade guide bearing assembly loose
Blade tracking too far away from wheel
flanges
Worn upper wheel bearings
Loose upper wheel mounting assembly
Too much feed or speed
Blade too coarse
Incorrect blade for material
Cut is binding blade
Too much blade tension
Loose guide bearing eccentrics
Worn guide bearings
Incorrect guide bearing adjustment
Loose guide bearing bracket
Loose bearing seat attachment screw
Blade guides worn
Blade guide bearings not adjusted properly
Blade guide bearing bracket loose
Blade running on wheel flange
Teeth too coarse for work
Too heavy feed
Too slow speed
Vibrating work piece
Tooth gullets loading
Blade in contact with workpiece before motor
is started
Blade tension too high
Worn transmission and worm gear
Gears need lubrication
Unusual
wear on
side/back of
blade
Breaking
teeth
Troubleshooting
(Continued)
Problem
Probable cause
Potential solutions
Summary of Contents for J-3130
Page 19: ...19 Exploded View Lower Saw Head...
Page 21: ...21 Exploded View Upper Saw Head...
Page 23: ...23 Exploded View Saw Base...
Page 25: ...25...
Page 27: ......