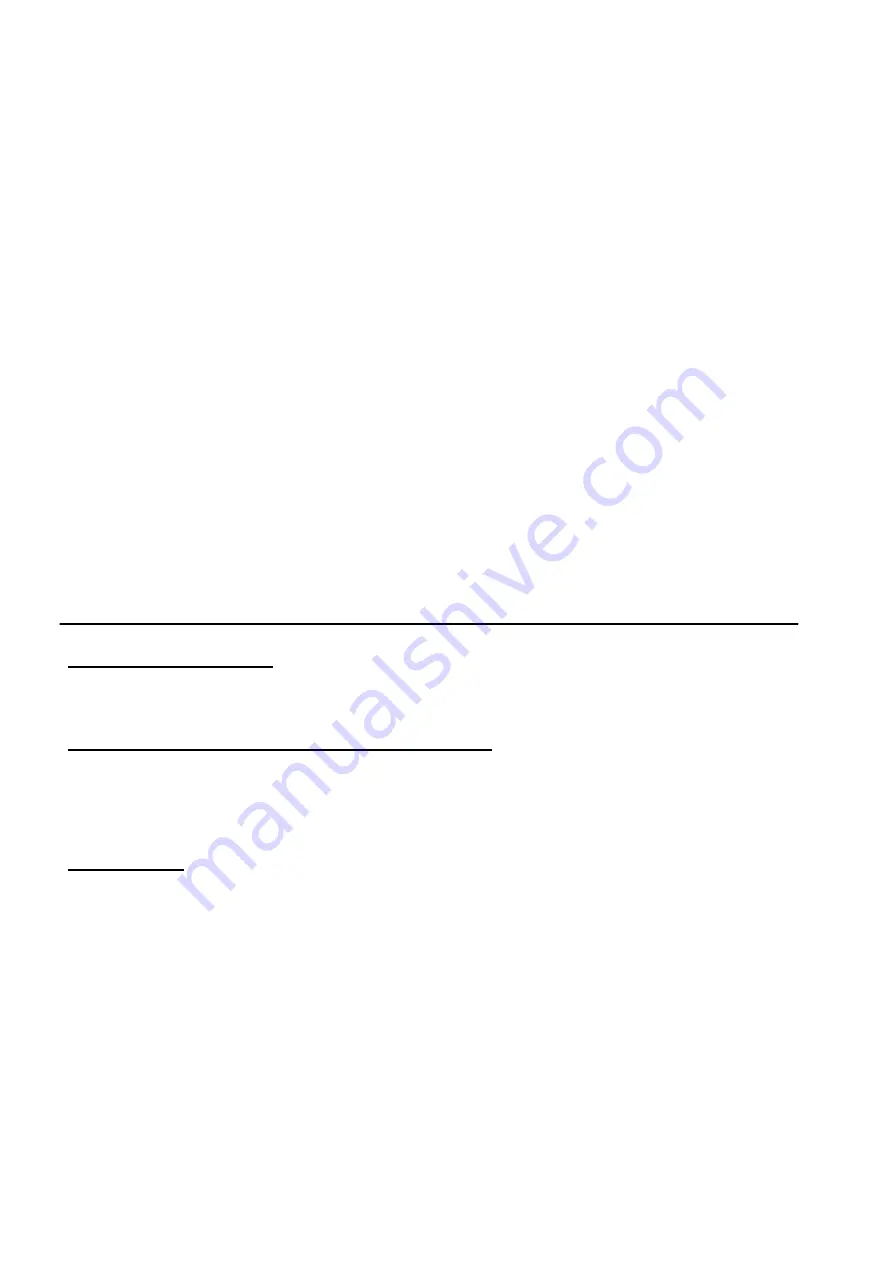
EN – ENGLISH
NOTE:
1.0 Special Safety Rules For Drill Press:
1. Caution : This drill press is intended for use only with drill bits. This use of other accessories may be
hazardous.
2. Correct drilling speeds : Factors which determine the best speed to use in any drill press operation
are : Kind of material being worked, size of hold, type of drill or other cutter, and quality of cut
desired. The smaller the drill, the greater the required RPM. In soft materials, the speed should be
higher than for hard metals.
3. Drilling in metal: Use clamps to hold the work when frilling in metal. The work should never be held
4. in there bare hand, the flutes of the drill may seize the work at any time, especially when breaking
through the stock. If the piece is whirled out of the operator’s hand, he may be injured, in any case,
the drill will be broken when the work strikes the column.
5. The work must be clamped firmly while drilling : Any tilting, twisting, or shifting results not only in a
rough hole, but also increases drill breakage. For flat work, lay the piece on a wooden base and
clamp it firmly down against the table to prevent it from turning. If the piece is of irregular shape and
cannot be laid flat in the table, it should be securely blocked and clamped.
6. The chuck shall be securely fastened to the spindle and so that it can’t separate from spindle.
7. Remove Key from chuck after adjustment.
8. The tool is to be disconnected from the power supply while the motor is being mounted, connected
or reconnected.
9. Secure the tool to the supporting structure if, during normal operation, there is any tendency for the
tool to tip over, slide, or walk on the supporting surface.
10. The set screws of head frame should be screwed tightly before suing this machine.
11. Connect to a supply circuit protected by a circuit breaker or time delay fuse.
12. Fasten base to floor or worktable before using the drill press.
2.0 VII. Important Notice For CE
Handling of Machine
1. The total weight of this machine must be ensured before handling.
2. It is better to handle this machine with the help of lifting tools.
Environment Requirements for Installation
1. Be sure to provide sufficient light for operation according to the codes or regulations published for
local area. If you do not get the information about lighting, a light intensity of 300 Lux is the least
value to be supplied.
2. The place where machine install must be flat and big enough for the operation.
Noise Level
1. The noise level of this machine is about 75 db(A)during operation.
2. While taking provisions for the risk of noise, the noise level of working environment should be taken
into consideration also.