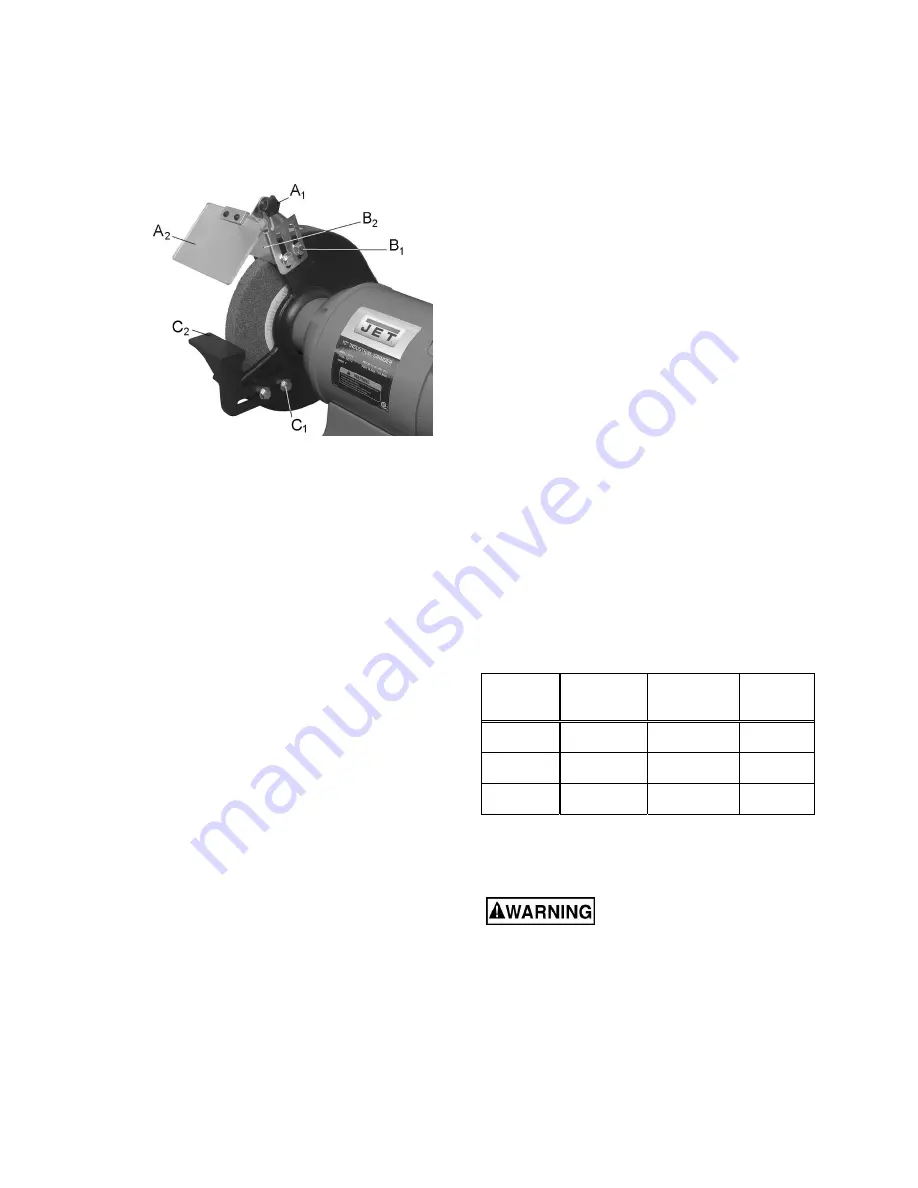
12
8.0
Adjustments
8.1
Eye Shield Tilt Adjustment
1. Loosen lock knob (A
1
, Figure 10).
2. Adjust eye shield (A
2
) to the desired tilt angle.
Figure 10: eye shield adjustment
8.2
Spark Guard
As the wheel wears down, the spark guards must
be re-adjusted to maintain a 1/16" distance.
Refer to Figure 10.
1. Loosen two hex cap screws (B
1
) with a 14mm
wrench.
2. Slide the spark guard (B
2
) to 1/16" distance
from the grinding wheel surface.
3. Tighten screws (B
1
).
8.3
Tool Rest
As the wheel wears down, the tool rests must be
re-adjusted to maintain a 1/16" distance.
Refer to Figure 10.
1. Loosen two hex cap screws (C
1
) with a 14mm
wrench.
2. Slide the tool rest (C
2
) to a distance of 1/16"
from the grinding wheel.
3. Tighten screws (C
1
).
9.0
Maintenance
For safety, turn the switch to OFF and remove plug
from the power source outlet before adjusting and
maintaining the bench grinder. If the power cord is
worn, cut or damaged in any way, have it replaced
immediately.
9.1
Ring Test
Before replacing a grinding wheel, perform this
simple test on the replacement wheel:
1. Loop a piece of string through the grinding
wheel hole and suspend the wheel by holding
up the string.
2. Tap the wheel with a piece of scrap wood or a
wooden dowel.
3. A good wheel will "ring"; a defective wheel will
"thud". Discard any wheel that does not "ring".
An internal defect may not be apparent by visual
inspection alone. The ring test may identify an
internal crack or void.
9.2
Care of Grinding Wheels
In normal use, grinding wheels may become
cracked, grooved, rounded at the edges, chipped,
out of true or loaded with foreign material.
Cracked wheels should be replaced
IMMEDIATELY. The other conditions can be
remedied with a dressing tool. New wheels
sometimes require dressing to make them round.
See
sect. 10.5.
9.3
Changing Wheels
The JET Series bench grinders come equipped
with general purpose grinding wheels. Wheels vary
according to types of abrasive, hardness, grit size,
and structure. Contact your local distributor for the
proper grinding wheel or wire wheel brush for your
application.
If you replace a wheel, obtain one with a safe rated
speed at least as high as the
NO
LOAD RPM
marked on the grinder's nameplate. Refer to Table
2 to determine correct dimensions for the
replacement wheel.
Model
Wheel
Diameter
Maximum
Width
Center
Hole
IBG-8
8" 1"
5/8"
IBG-10
10" 1" 1"
IBG-12
12” 2”
1-1/4”
Table 2
Your bench grinder will accept most polishing and
buffing wheels available at dealers and hardware
stores.
The use of any other
accessory is not recommended and may result
in serious injury!
To change a wheel
(see Figure 11)
:
1. Disconnect grinder from power source.
2. Loosen spark guard (B) and tool rest (C) and
move them away from the wheel.
3. Remove wheel guard using a cross-point or
flathead screwdriver.
Summary of Contents for IBG-8
Page 18: ...18 12 1 1 IBG 8 Grinder Exploded View...
Page 21: ...21 12 2 1 IBG 10 Grinder Exploded View...
Page 24: ...24 12 3 1 IBG 12 Grinder Exploded View...
Page 29: ...29 13 0 Electrical Connections 13 1 Wiring Diagram for IBG 8...
Page 30: ...30 13 2 Wiring Diagram for IBG 10...
Page 31: ...31 13 3 Wiring Diagram for IBG 12...
Page 33: ...33 This page intentionally left blank...
Page 34: ...34 This page intentionally left blank...
Page 35: ...35 This page intentionally left blank...
Page 36: ...36 427 New Sanford Road LaVergne Tennessee 37086 Phone 800 274 6848 www jettools com...