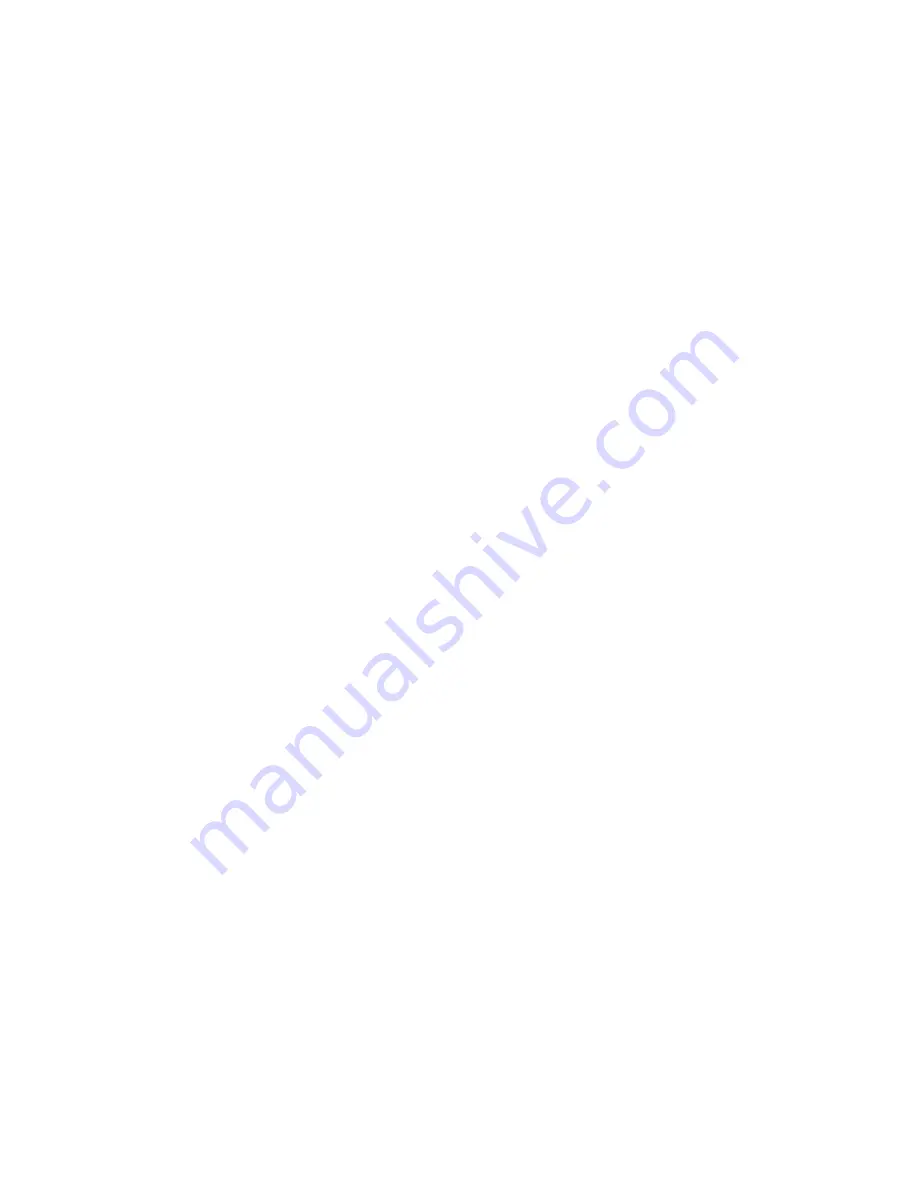
3
28. Keep work area clean. Cluttered areas and
benches invite accidents.
29. Use the right tool. Don't force tool or attachment
to do a job for which it was not designed.
30. Use proper extension cord. An undersized cord
will cause a drop in line voltage resulting in loss
of power and overheating. Table 2
(see sect.
7.2)
shows correct size to use depending on
cord length and nameplate ampere rating.
31. Maintain tools with care. Keep tools sharp and
clean for best and safest performance. Follow
instructions for lubricating and changing
accessories.
32. Direction of feed: Feed work into a blade or
cutter against the direction of rotation of the
blade or cutter only.
1.2
Specific rules for abrasive
sanding machines
Abrasive sanding can be hazardous to operators
and bystanders. Sanding sparks, chips and dust
particles thrown off by the sanding disc can cause
serious injury by contact or inhalation. In addition to
the general safety rules above, you must also
comply with the following specific requirements:
1. If you are not thoroughly familiar with the
operation of belt and disc sanders, obtain
advice from your supervisor, instructor or other
qualified person.
2. A dust collection system is recommended.
Operator shall also wear a dust mask at all
times.
3. Do not sand magnesium; it could catch fire.
Additional precautions may be needed for other
materials that are hazardous or flammable.
Always consult the material manufacturer for
instructions on sawing and handling.
4. Do not start the grinder while a workpiece is
contacting the grinding wheel or the sanding
belt.
5. If there is any risk of the machine tipping or
moving during operation, such as when sanding
long or heavy boards, the machine must be
securely fastened to a supporting surface.
6. Make sure the sanding belt is running in the
proper direction; it must travel downward when
viewed from front of machine.
7. Make sure sanding belt tracks correctly so that
it does not run off the wheels.
8. Make sure sanding belt or disc is not torn or
loose.
9. Before sanding, allow motor to reach operating
speed, then check the sanding disc for wobble,
runout or any unbalanced condition. If the disc
is not operating accurately and smoothly,
immediately stop the motor and make repairs
before attempting sanding operations.
10. Always hold the work firmly on the table when
sanding on the belt or disc. The only exception
is curved work performed on the bottom wheel.
11. Always sand on the downward side of the disc
so that the work is held securely on the table.
Sanding on the upward side of the disc can
cause the workpiece to fly upward, which may
be hazardous.
12. Always maintain a
minimum
clearance of 1/16-
inch between table and sanding belt or disc.
13. This machine can be used for processing wood
or metal products. However, combining wood
dust and metal filings can create a fire hazard.
Make sure that the dust collector is free of wood
dust deposits before processing metal
products.
14. Never wear gloves or hold the work with a rag
when sanding.
15. Sand with the grain of the wood when possible.
16. Do not sand pieces of material that are too small
to be safely supported.
17. When sanding a large workpiece, provide
additional support at table height.
18. Avoid awkward hand positions where a sudden
slip could cause a hand to move into the
sanding belt or disc.
19. Never force the work. Slowing or stalling the
motor will cause overheating.
20. Always remove scrap pieces and other objects
from the belt and disc tables before turning on
the machine.
21. When sanding metal, never use a steady
stream of water on the work piece. Dip the
workpiece in water to cool it.
22. Wear protective clothing such as apron, safety
shoes, or arm guards, where the sanding or
grinding activity presents a hazard to the
operator.
23. Abrasive discs must be stored in a controlled
environment area. Relative humidity should be
35% to 50% and the temperature should be
between 60 and 80 degrees Farenheit. Failure
to do so could cause premature disc failure.
24. Examine the face of the sanding disc carefully.
Excessive sanding which wears down to the
backing material can cause tearing of the disc.
Never use a disc which shows backing, nicks or
cuts on the surface or edge, or damage due to
creasing or poor handling.
Summary of Contents for IBDG-248
Page 20: ...20 13 1 1 IBDG 248 Belt Disc Sander Exploded View ...
Page 23: ...23 13 2 1 IBDG 248VS Belt Disc Sander Exploded View ...
Page 26: ...26 13 3 1 IBDG 436 Belt Disc Sander Exploded View ...
Page 29: ...29 13 4 1 IBDG 436VS Belt Disc Sander Exploded View ...
Page 34: ...34 This page intentionally left blank ...
Page 35: ...35 This page intentionally left blank ...
Page 36: ...36 427 New Sanford Road LaVergne Tennessee 37086 Phone 800 274 6848 www jettools com ...