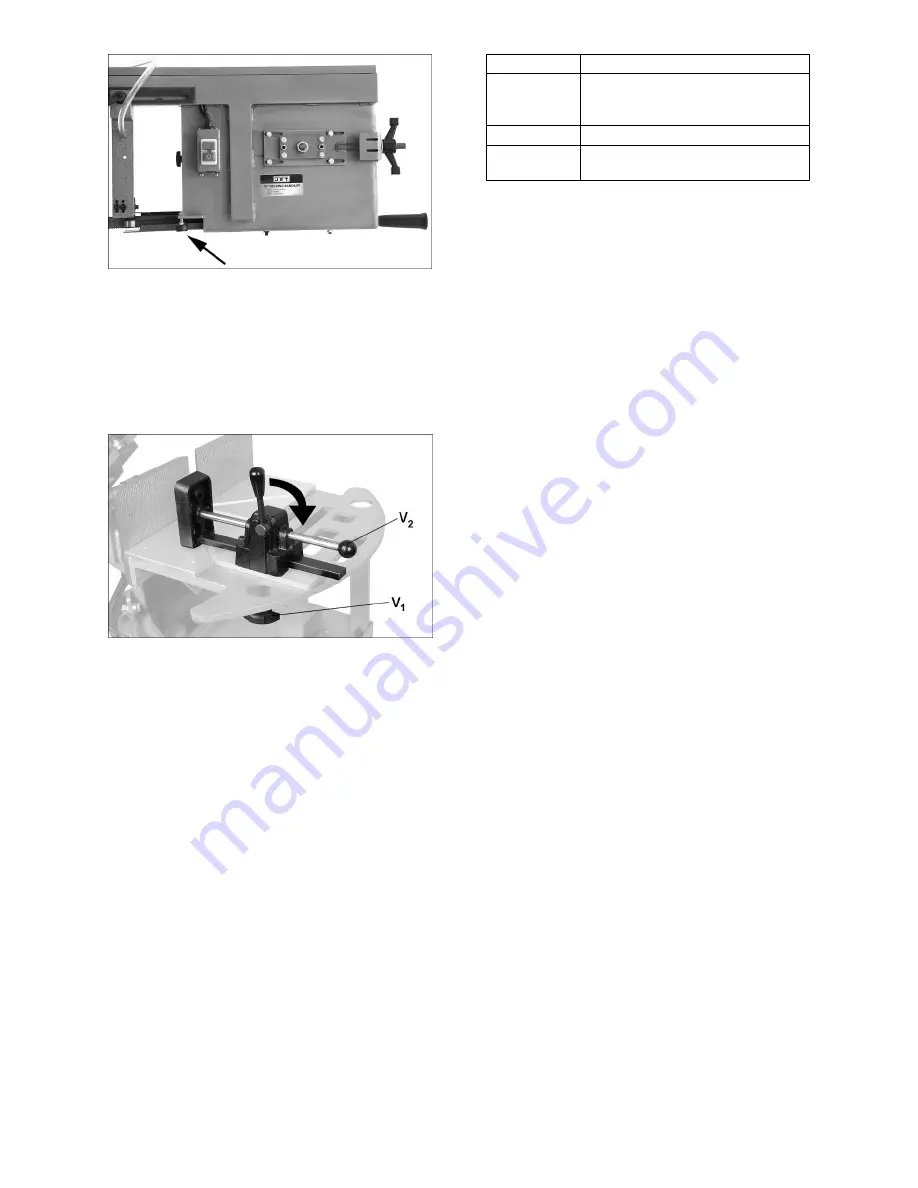
15
Figure 7-14: stop bolt adjustment
7.13
Vise positioning
The floating vise jaw can be moved before or behind
blade. Loosen locking knob (V
1
) and slide vise to
position.
To clamp workpiece, push jaw close to workpiece
using rod (V
2
), then push top handle down to tighten.
Figure 7-15: floating vise jaw
7.14
Work stop
The work stop is generally used when cutting
multiple pieces to identical length. Position stop
desired distance from blade and tighten set screw.
Loosen collar (see A
2
, Figure 5-2) to slide work stop
along lower rod. Retighten collar before operating.
8.0
Operation
8.1
Blade selection
The saw is provided with a blade that is adequate
for a variety of cut-off jobs on a variety of common
materials.
See Table 3 for recommended speeds for various
materials. These selections, while appropriate for
many shop cutting needs, do not encompass the
wide variety of blades of special configuration (tooth
pitch and set) and special alloys for cutting unusual
or exotic materials.
Speed/FPM Material
64
Tool Steel, Stainless Steel,
Phosphor Bronze, Cast Iron,
Malleable Iron
132
Mild Steel, Hard Brass, Bronze
247
Soft Brasses and Bronzes,
Hard Aluminum, Plastics
Table 3
A coarse blade could be used for a solid steel bar
but a finer tooth blade would be used on a thin-wall
tube. In general, the blade choice is determined by
the thickness of the material; the thinner the
material, the finer the tooth pitch.
A minimum of three teeth should be on the work
piece at all times for proper cutting. The blade and
workpiece can be damaged if the teeth are so far
apart that they straddle the workpiece.
For very high production on cutting of special
materials, or to work hard-to-cut materials such as
stainless steel, tool steel, or titanium, ask your
industrial distributor for more specific blade
recommendations. Also, the supplier who provides
the workpiece material should be prepared to
provide specific instructions regarding the best
blade (and coolant or cutting fluid, if needed) for the
material and shape supplied.
8.2
Blade break-in
New blades are very sharp and therefore have a
tooth geometry which is easily damaged if a careful
break-in procedure is not followed. Consult the
blade manufacturer’s literature for break-in of
specific blades on specific materials. However, the
following procedure will be adequate for break-in of
JET-supplied blades on lower alloy ferrous
materials.
1. Clamp a round section workpiece in the vise.
The workpiece should be 2 inches or larger in
diameter.
2. Set the saw on low speed. Start the cut with a
very light feed rate (i.e. bow descent).
3. When the saw has completed 1/3 of the cut,
increase feed rate slightly and allow saw to
complete the cut.
4. Keep the same hydraulic cylinder setting and
begin a second cut on the same or similar
workpiece.
5.
When blade has completed about 1/3 of cut,
increase feed rate. Watch chip formation until
cutting is at its most efficient rate and allow saw
to complete the cut (see
sect. 8.4, Evaluating
cutting efficiency).
6. The blade is now ready for regular service.
Summary of Contents for HVBS-10-DMW
Page 20: ...20 11 1 1 HVBS 8 DMW Bow Assembly Exploded View Figure 11 1...
Page 21: ...21 11 1 2 HVBS 8 DMW Table Assembly Exploded View Figure 11 2...
Page 22: ...22 11 1 3 HVBS 8 DMW Motor and Support Arm Assembly Exploded View Figure 11 3...
Page 28: ...28 11 2 1 HVBS 10 DMW DMWC Bow Assembly Exploded View Figure 11 6...
Page 29: ...29 11 2 2 HVBS 10 DMW DMWC Table Assembly Exploded View Figure 11 7...
Page 30: ...30 11 2 3 HVBS 10 DMW DMWC Motor and Support Arm Assembly Exploded View Figure 11 8...
Page 31: ...31 11 2 4 HVBS 10 DMW DMWC Vise and Table Assembly Exploded View Figure 11 9...
Page 32: ...32 11 2 5 HVBS 10 DMW DMWC Base Assembly Exploded View Figure 11 10...
Page 37: ...37 12 0 Electrical Connections for HVBS DMW Band Saws Figure 12 1...
Page 39: ...39 This page intentionally left blank...
Page 40: ...40 427 New Sanford Road LaVergne Tennessee 37086 Phone 800 274 6848 www jettools com...