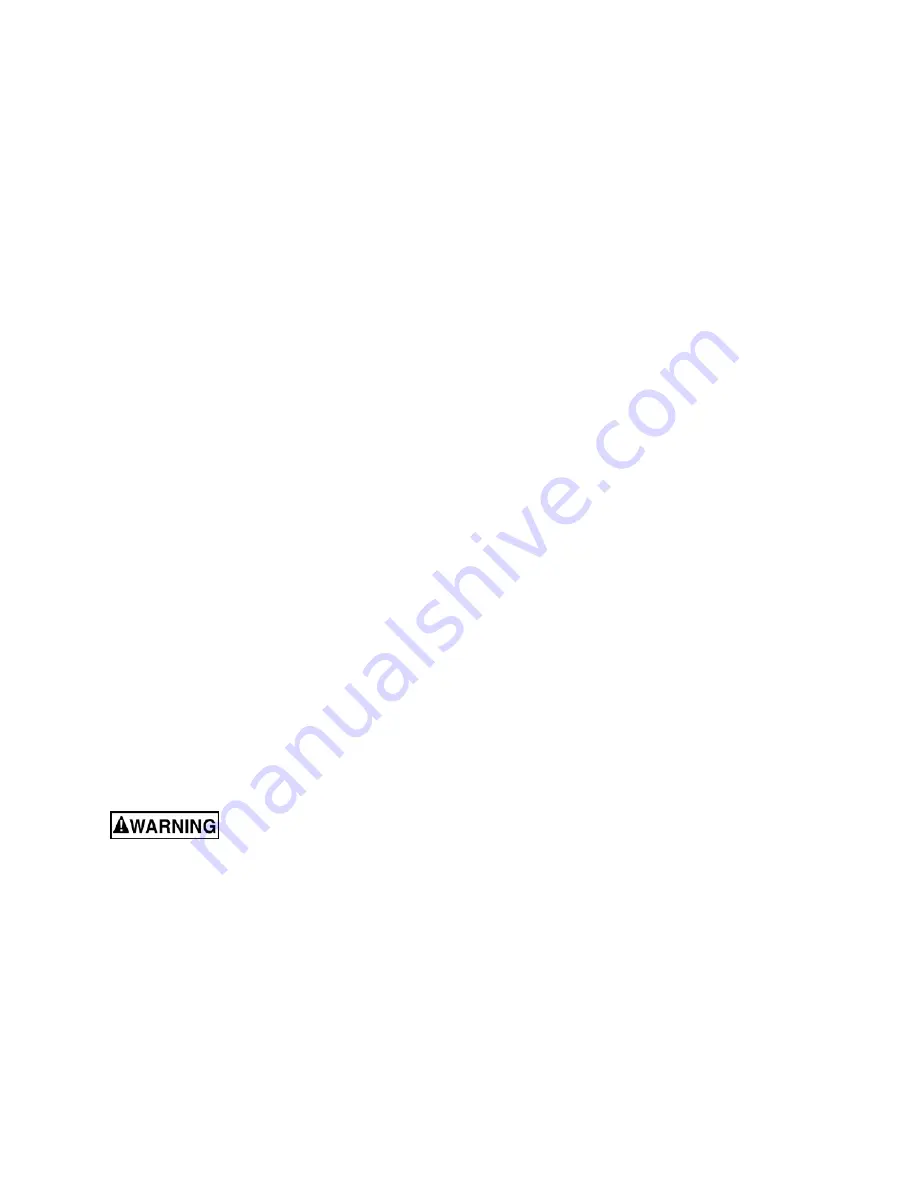
7
6.0
Assembly
Refer to Figure 1 for identification.
1. Use a lifting device, such as a hoist or forklift
with straps, to position machine upright.
2. Bolt the frame brackets to the main frame with
the provided screws and hex nuts.
Finger
tighten only.
3. The press should be placed within a well-lit
area, upon a level floor, preferably concrete.
Lower the press onto the floor, allowing it to
stabilize on the brackets. Fully tighten the hex
nuts on the frame brackets.
4. The hex filler plug (see parts breakdown: item
#17 for HP-5A; #8A for HP-15A; #8D for HP-
35A) was installed for shipping purposes.
Remove this and replace it with the provided
vented plug.
5. Place the end of the pump handle into the
handle socket, and secure it with the screw.
7.0
Operation
Refer to Figure 1 for identification.
1. Remove all items from bed plates.
2. Remove table holding pins. (Support the table
frame on the HP-5A.)
3. Raise or lower table frame to desired position,
so that when workpiece is mounted, it will be
close to the ram press head.
Model HP-5A:
Raise or lower table frame by
hand.
Models HP-15A,-35A:
Rotate crank handle to
raise or lower table frame.
4. Re-insert table holding pins. Pins must be fully
engaged through front and back holes of the
frame.
5. Place workpiece onto bed plates.
Make sure workpiece is
center-loaded and secure before pressing, and
that table holding pins are properly inserted.
Some objects may have a tendency to pop out
or explode under pressure. Exercise proper
precautions.
6. If desired, slide ram assembly laterally (15-
and 35-ton models only) by mounting the hand
crank onto the lateral shaft and rotating it.
Do
not attempt to slide ram during operation.
7. The handwheel can be used to rapidly adjust
the ram extension screw into or out of the
plunger.
Note:
The length of ram screw extending out
of the piston should be kept as short as
possible. Raise the table rather than extend
the screw to its travel limit.
8. Close valve by rotating release valve handle
clockwise as far as it will turn.
9. Pump the handle to lower the ram until it
makes light contact with workpiece. Align the
workpiece to ensure that desired contact point
is directly beneath the press head. Slowly
pump handle again until load begins to be
applied to workpiece.
10. Remove your hand from workpiece area and
step toward the side of the press (do not stand
directly in front of workpiece). Continue slowly
pumping to complete the operation.
11. When operation is complete, slowly retract ram
by incrementally turning release valve handle
counter-clockwise.
8.0
Maintenance
•
Keep the press clean, and periodically
lubricate joints and moving parts with light oil.
•
Inspect the press before each use, for signs of
damage, bent pins, missing or loose bolts,
cracked welds, oil leaks, abnormal operation,
and the like. Make repairs or replacements as
needed before putting the machine back into
service.
•
Periodically remove filler plug (#17/HP-5A;
#8A/HP-15A; #8D/HP-35A) to check that
hydraulic cylinder is filled with oil. Top off as
needed with good quality hydraulic oil.
Reinsert filler plug.
•
Flush and replace the oil in the hydraulic
cylinder approximately every 2 years. Refer to
section
4.0 Specifications
for oil capacity for
your particular model.
9.0
Replacement Parts
Replacement parts are listed on the following pages. To order parts or reach our service department, call 1-
800-274-6848 Monday through Friday, 8:00 a.m. to 5:00 p.m. CST. Having the Model Number and Serial
Number of your machine available when you call will allow us to serve you quickly and accurately.
Non-proprietary parts, such as fasteners, can be found at local hardware stores, or may be ordered from JET.
Some parts are shown for reference only, and may not be available individually.
Summary of Contents for HP-15A
Page 8: ...8 9 1 1 HP 5A Head Assembly Exploded View...
Page 10: ...10 9 2 1 HP 5A Frame Assembly Exploded View...
Page 12: ...12 9 3 1 HP 15A Head Assembly Exploded View...
Page 14: ...14 9 4 1 HP 15A Frame Assembly Exploded View...
Page 16: ...16 9 5 1 HP 35A Head Assembly Exploded View...