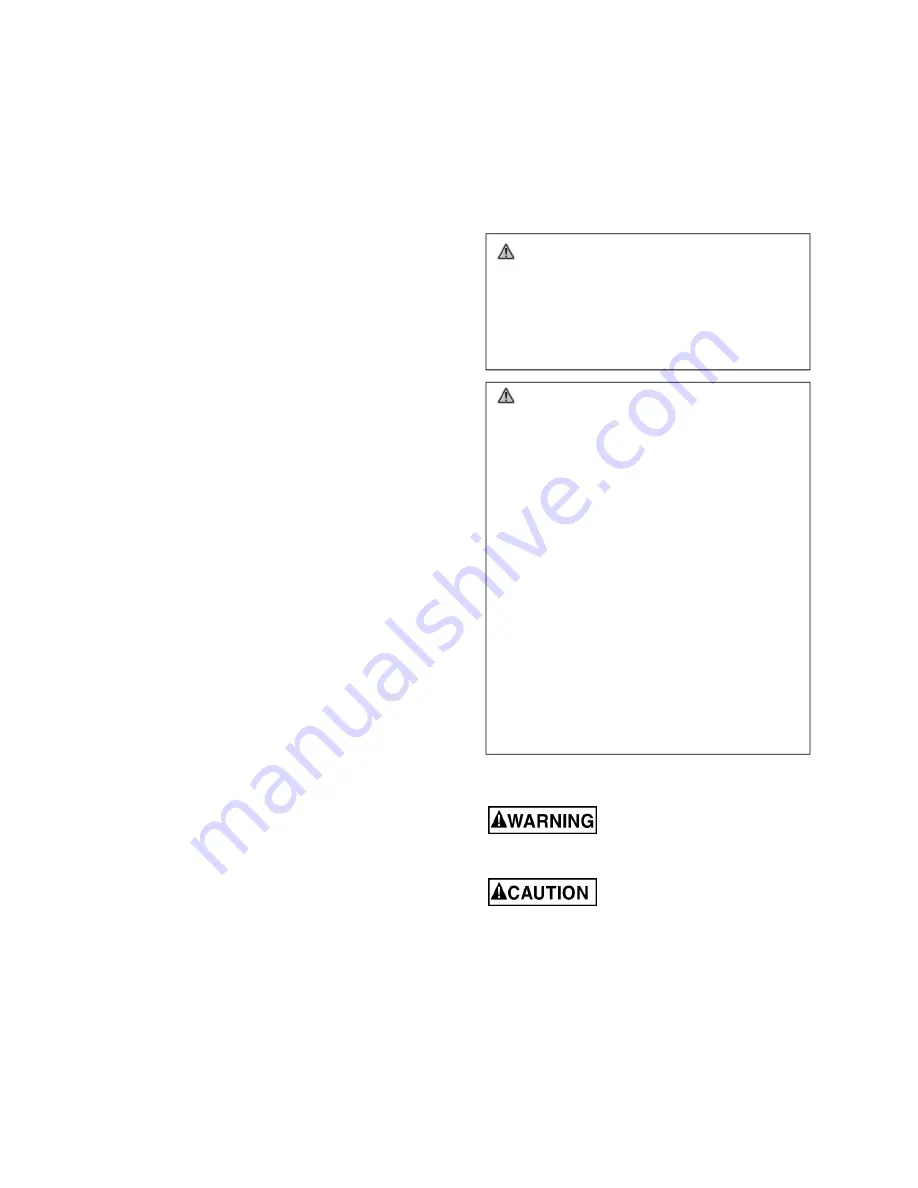
3
28. Keep safety guards in place at all times when
the machine is in use. If removed for
maintenance purposes, use extreme caution
and replace the guards immediately after
completion of maintenance.
29. Check damaged parts. Before further use of the
machine, a guard or other part that is damaged
should be carefully checked to determine that it
will operate properly and perform its intended
function. Check for alignment of moving parts,
binding of moving parts, breakage of parts,
mounting and any other conditions that may
affect its operation. A guard or other part that is
damaged should be properly repaired or
replaced.
30.
Maintain all machine tools with care. Follow all
maintenance instructions for lubricating and the
changing of accessories.
31.
No attempt shall be made to modify or have
makeshift repairs done to the machine. This not
only voids the
warranty but also renders the
machine unsafe.
32. Keep work area clean. Cluttered areas invite
accidents. Keep the floor around the machine
clean and free of scrap material, oil and grease.
33. Keep visitors a safe distance from the work
area. Keep children away.
34. Make your workshop child proof with padlocks,
master switches or by removing starter keys.
35. Give your work undivided attention. Looking
around, carrying on a conversation and “horse-
play” are careless acts that can result in serious
injury.
36. Maintain a balanced stance at all times so that
you do not fall into the blade or other moving
parts. Do not overreach or use excessive force
to perform any machine operation.
37. Use the right tool at the correct speed and feed
rate. Do not force a tool or attachment to do a
job for which it was not designed. The right tool
will do the job better and more safely.
38. Use only recommended accessories; improper
accessories may be hazardous.
39. Keep saw blades sharp and clean for the best
and safest performance.
40. Turn off the machine before cleaning. Use a
brush or vacuum to remove chips or debris —
do not use bare hands. Never brush away chips
while machine is in operation.
41. Do not stand on the machine. Serious injury
could occur if the machine tips over.
42. Never leave the machine running unattended.
Turn the power off and do not leave the
machine until it comes to a complete stop.
43. Avoid dangerous working environments. Do not
use stationary machine tools in wet or damp
locations. Keep work areas clean and well lit.
Familiarize yourself with the following safety
notices used in this manual:
This means that if precautions are
not heeded, it may result in serious, or possibly even
fatal, injury.
This means that if precautions are
not heeded, it may result in minor injury and/or
possible machine damage
SAVE THESE INSTRUCTIONS
WARNING:
This product can expose you to
chemicals including titanium dioxide which is
known to the State of California to cause cancer,
and lead which is known to the State of
California to cause cancer and birth defects or
other reproductive harm. For more information
go to http://www.p65warnings.ca.gov.
WARNING:
Some dust, fumes and gases
created by power sanding, sawing, grinding,
drilling, welding and other construction activities
contain chemicals known to the State of
California to cause cancer and birth defects or
other reproductive harm. Some examples of
these chemicals are:
lead from lead based paint
crystalline silica from bricks, cement and
other masonry products
arsenic and chromium from chemically
treated lumber
Your risk of exposure varies, depending on how
often you do this type of work. To reduce your
exposure to these chemicals, work in a well-
ventilated area and work with approved safety
equipment, such as dust masks that are
specifically designed to filter out microscopic
particles. For more information go to
http://www.p65warnings.ca.gov/ and http://www.
p65warnings.ca.gov/wood.
Summary of Contents for HBS-916EVS
Page 20: ...20 14 1 1 HBS 916EVS 1018EVS Bed and Base Assembly Exploded View...
Page 21: ...21 14 1 2 HBS 916EVS Bow Assembly Exploded View...
Page 22: ...22 14 1 3 HBS 1018EVS Bow Assembly Exploded View...
Page 29: ...29 14 2 1 HBS 916EVS 1018EVS Gear Speed Reducing Box Exploded View...
Page 31: ...31 15 0 Electrical Connections HBS 916EVS 1018EVS...