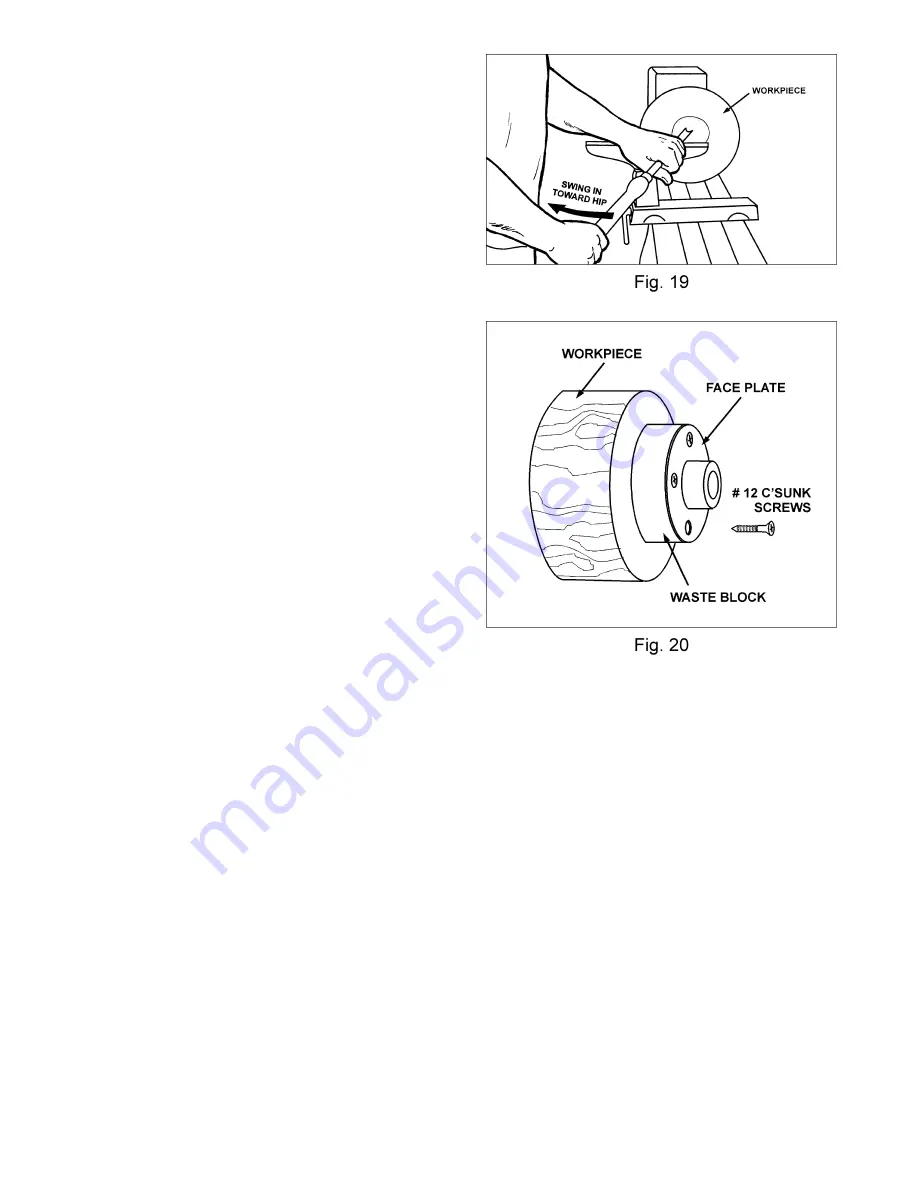
16
Sanding and Finishing
Leaving clean cuts will reduce the amount of
sanding required. Begin with a fine sandpaper
(120 grit or finer). Coarser sandpaper will leave
deep scratches that are difficult to remove, and
dull crisp details. Fold the sandpaper into a pad;
do not wrap sandpaper around your fingers or
the workpiece.
To apply a finish, the workpiece can be left on
the lathe. Turn off lathe and use a brush, or cloth
to apply the finish. Remove excess finish before
restarting lathe. Allow drying and sanding again
with 320 or 400 grit sandpaper. Apply additional
coats of finish and buff.
Face Plate and Bowl Turning
Face plate turning is normally done on the
inboard side of the headstock over the bed see
Figure 19. You must pivot the headstock 180°
for larger workpieces.
Mounting Stock
Use of a face plate is the most common method
for holding a block of wood for turning bowls,
and plates.
1. Select stock at least 1/8" to 1/4" larger than
the dimension on the desired finished
workpiece.
2. True one surface of the workpiece for
mounting against the face plate. It is best
to leave extra stock against the faceplate
that can be cut off when the workpiece is
finished.
3. Using the faceplate as a template, mark the
location of the mounting holes, and drill pilot
holes of the appropriate size. If the mounting
screws on the faceplate interfere with the
workpiece, a waste block can be mounted to
the faceplate and then the waste block
mounted to the workpiece by gluing or
screwing, see Figure 20.
4. Both waste block and workpiece should
have good flat surfaces.
5. Push in on the spindle lock and thread face
plate and workpiece onto the spindle.
Tighten setscrews in the faceplate when
secure.