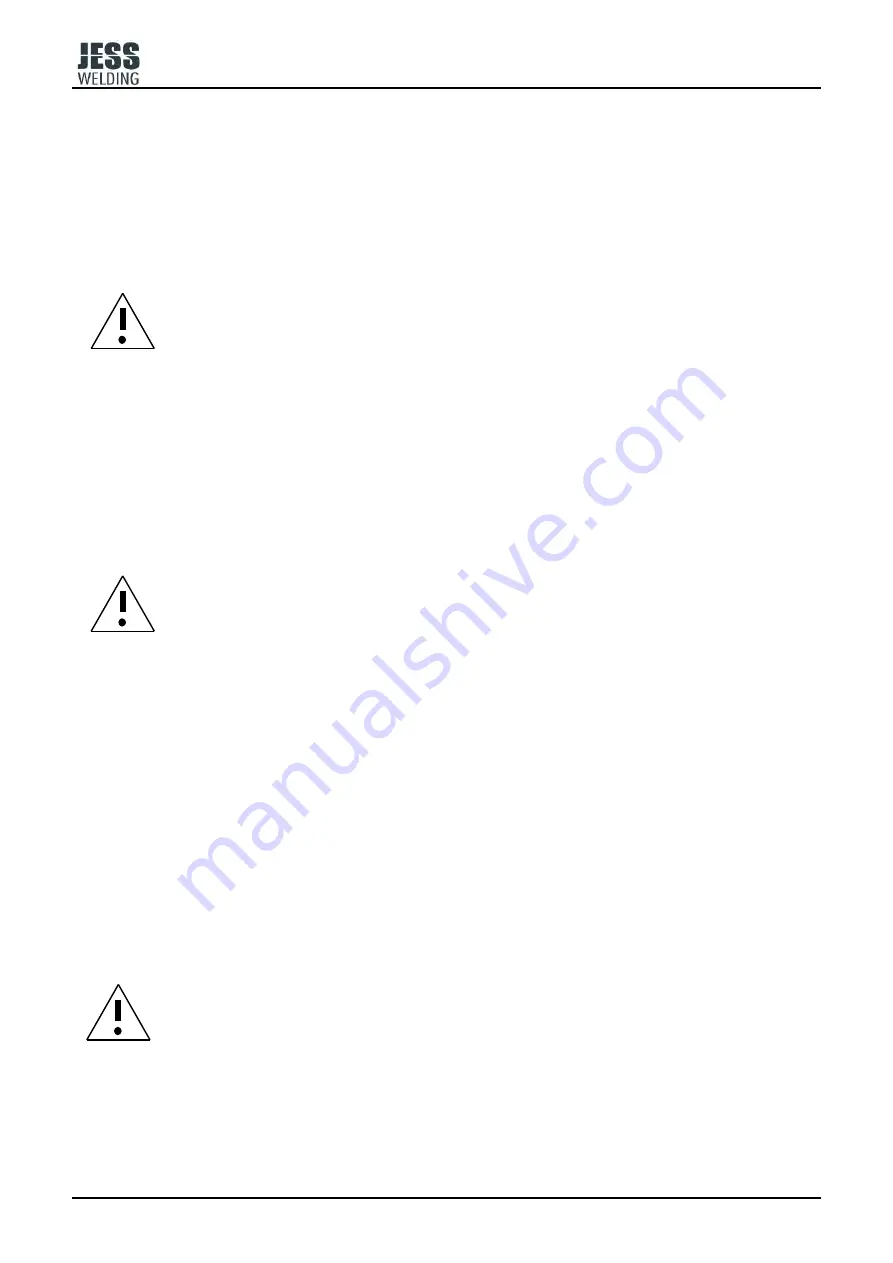
Operating manual
Page 12
8. Initial operation
Installation of the welding unit
When installing the machine, take care of sufficient space for inlet and outlet cooling air so that the rated duty
cycle will be attained.
The machine should not be exposed to moisture, welding spatter or spark rays caused by grinding work.
The welding unit should not be operated in the rain at all.
Mains connection
To be carried out only by a qualified electrician!
Connect mains plug to mains cable as specified on the rating plate. The yellow-green lead has to be connected
to PE earth conductor. The three phases (black, brown, blue) may be connected to L1, L2, and L3 at random.
Connection of shielding gas cylinder
Put the cylinder in place near to the shielded-arc welding unit and secure with chain.
Connect cylinder pressure reducer and check that all connections are tightly sealed.
Connection of welding torch hose pack
Connect hose pack to central adapter.
Both cooling water hoses have to be plugged into the adequate couplings according to the colour with which
they are marked.
Ensure excellent contact between all connections within the welding circuit, i.e.
workpiece, torch connection and contact tip nozzle. Bad contact causes high
transition resistance which leads to overheating and poor quality of the weld.
Connection of workpiece cable
When the earth clamp is attached on the workpiece, choose appropriate spot without paint or rust for good
conductivity.
9. Welding
To obtain a high-quality weld, it is most important to select the right voltage step with optimum wire feed rate
and gas flow.
Setting of cylinder pressure reducer
Set the shielding gas flow rate at the pressure reducer on cylinder (6 - 18 l/min). The gas flow rate depends
chiefly on the welding amperage.
Loading of welding wire
Select the welding wire according to the material being welded. Mount the appropriate contact tip nozzle and
wire feed rollers. For more details see chapter 5 (Wire feed).
- Select weld grade via weld-grade switch, coarse/fine
Do not switch during welding operation
to avoid damage to the grade switches.
Setting of wire feed rate
Wire feed rate is dependent upon voltage step, the material used, diameter of welding wire and type of shielding
gas.
Start welding process by pressing torch trigger
Summary of Contents for MIG 325
Page 17: ...Betriebsanleitung Seite 14 12 Ersatzteile Abbildung 11 1 Frontansicht ...
Page 18: ...Betriebsanleitung Seite 15 Abbildung 11 2 Seitenansichten ...
Page 38: ...Operating manual Page 15 9 Spare parts Picture 11 1 Frontview ...
Page 39: ...Operating manual Page 16 Picture 11 2 Sideview ...
Page 44: ......