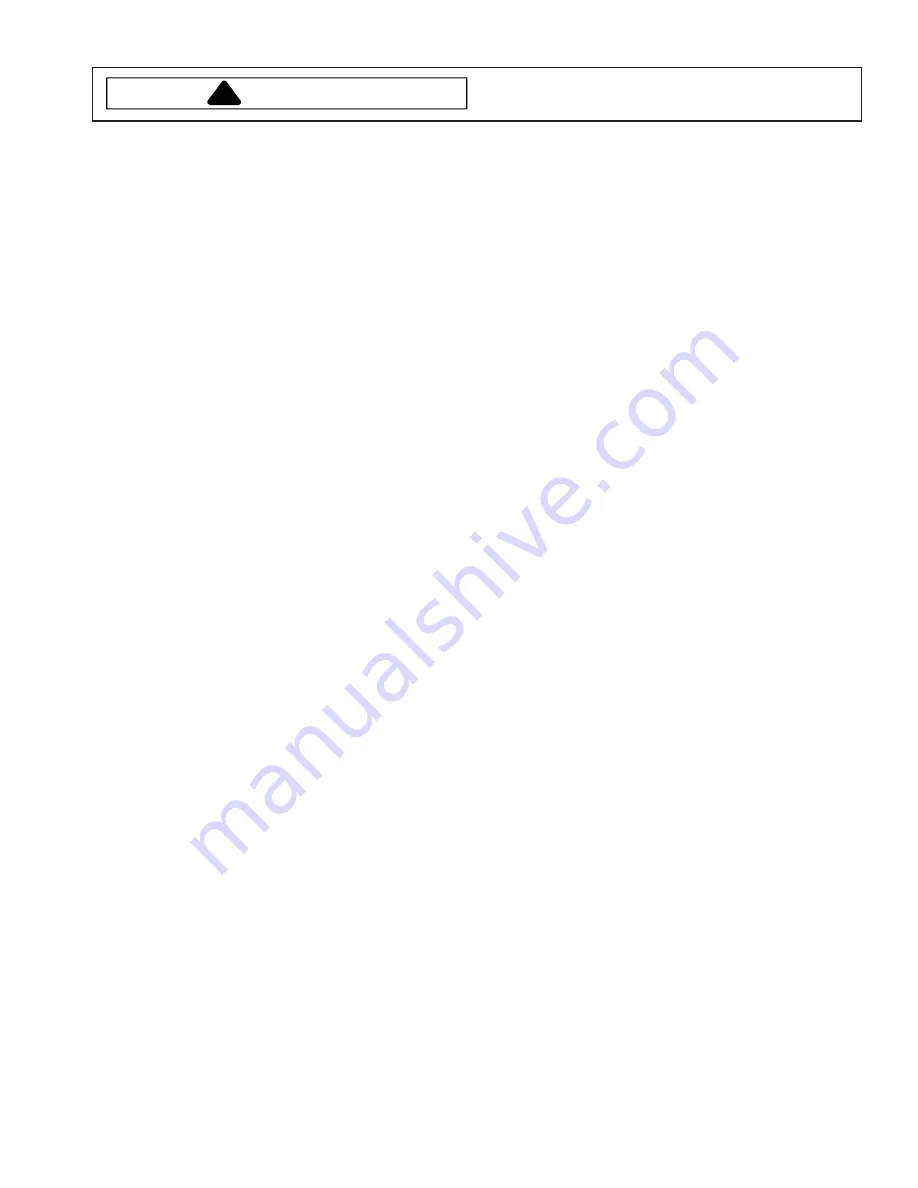
WARNING
!
To avoid risk of electrical shock, personal injury or death;
disconnect power to unit before servicing.
Disassembly Procedures
©2004 Maytag Services
16022882 Rev. 0
19
Burner Switch
1. Disconnect power and shut off gas supply to unit.
2. Remove control panel, see “Control Panel” procedure.
3. Remove C-clips on valve shaft securing switch.
4. Disconnect and label wire terminals from switch and
slide switch off of valve shaft.
NOTE:
On dual flow valve, disconnect and label wire
terminals from switch, remove screw securing
switch, and pull switch off of locating pin.
NOTE:
When removing any wires off of terminals, do not
pull on wire insulation. This can loosen or
damage the crimping connection
5. Reverse procedure to reassemble.
Spark Module
1. Disconnect power supply to unit.
2. Remove control panel, see “Control Panel” procedure.
3. Locate spark module behind the manifold assembly.
4. Only remove the quick disconnect plug located on
spark model at this time.
5. Remove screws securing spark module to the front
baffle.
6. Carefully rotate module around the top of the manifold.
NOTE:
For easier removal of spark module. Landing
ledge may be removed for easier access by
removing the screws located on each end.
7. Once spark module is removed, transfer high voltage
wires onto the new spark module, ensuring proper wire
placement.
NOTE:
Failure to transfer high voltage wires correctly will
result in improper spark operation.
8. Reverse procedure to reassemble.
Single Feed Burner Gas Valve
1. Disconnect power and shut off gas supply to unit.
2. Remove control panel, see “Control Panel” procedure.
3. Remove screws securing landing ledge located on
each end.
4. Remove burner switches, by removing C-clip and
sliding switch off of valve shaft.
5. Remove compression nut on backside of valve.
NOTE:
Take care not to bend or damage tubing.
6. Remove valve clamp.
NOTE:
Check for leaks before installing control panel.
7. Reverse procedure to reassemble.
NOTE:
When reinstalling, ensure valve and gasket is
seated on manifold and tighten down valve clamp
evenly.
Dual Feed Burner Gas Valve
1. Disconnect power and shut off gas supply to unit.
2. Remove control panel, see “Control Panel” procedure.
3. Remove screws securing landing ledge located on
each end.
4. Remove any necessary components to gain access to
the valve being replace (transformer, terminal block,
etc.).
5. Disconnect and label wire terminals from the burner
switch.
6. Remove simmer gas line and the main gas line.
NOTE:
Take care not to bend or damage tubing.
7. Remove valve clamp.
NOTE:
Check for leaks before installing control panel.
8. Reverse procedure to reassemble.
NOTE:
When reinstalling, ensure valve and gasket is
seated on manifold and tighten down valve clamp
evenly.
Oven Thermostat
1. Disconnect power and shut off gas supply to unit.
2. Remove control panel, see “Control Panel” procedure.
3. Remove maintop, see “Maintop” procedure.
4. Remove screws securing sensing bulb to bracket,
located inside the oven cavity.
5. Gently pull sensing bulb out through the oven cavity.
NOTE:
Take care not to disturb the insulation.
6. Remove screws securing selector switch to bracket.
7. Remove screws securing bracket.
8. Remove screws securing thermostat to bracket.
9. Disconnect and label wire terminals from thermostat.
10. Reverse procedure to reassemble.
Single Feed Burner
1. Disconnect power and shut off gas supply to unit.
2. Removing the corresponding grate, burner cap and
port ring.
3. Remove venturi bolt securing burner base.
4. Burner base can now be lifted off maintop.
5. Disconnect electrode wire from burner base.
6. Reverse procedure to reassemble.
NOTE:
When repairing or replacing burner jet or burner
tubing, maintop must be removed.