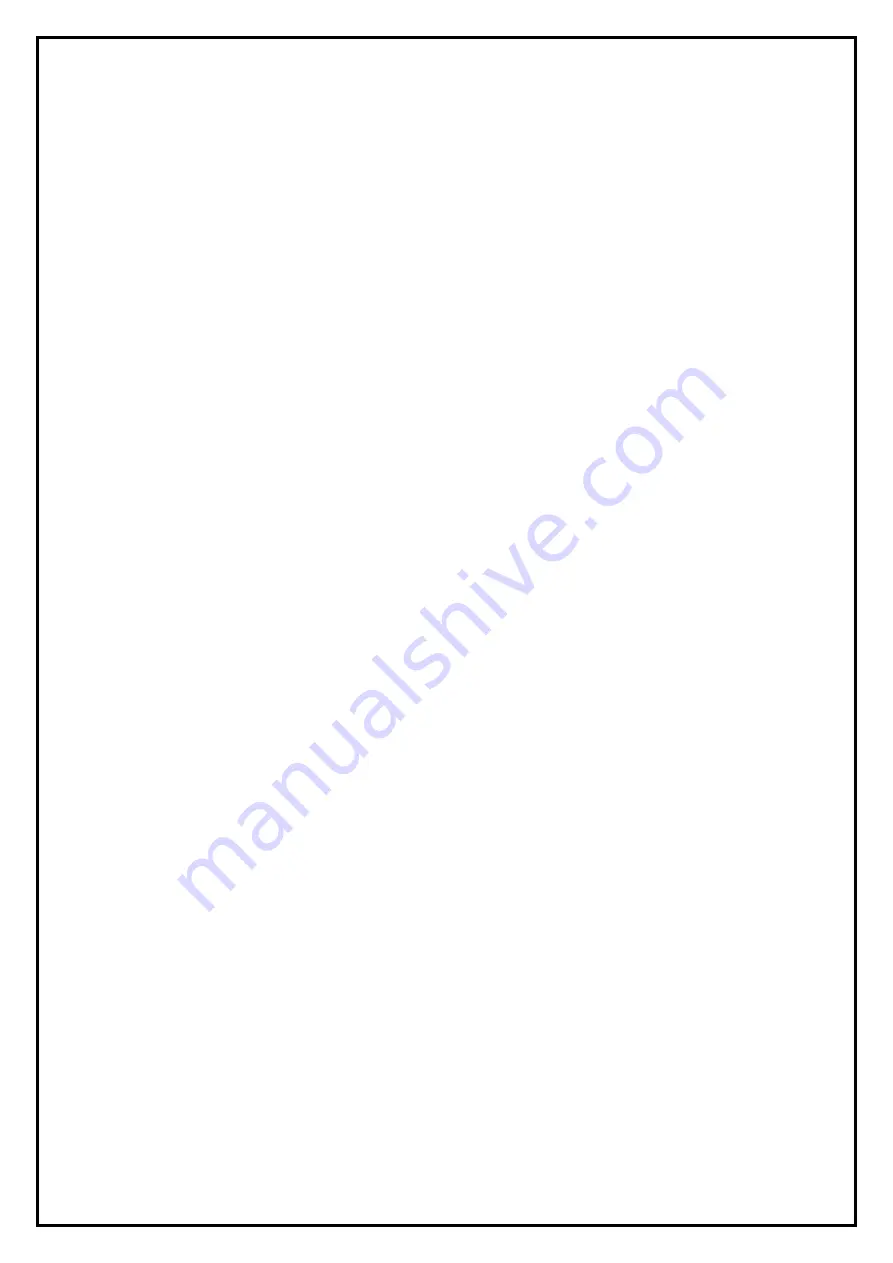
17
6.1 Daily checking items before operation
The user must perform daily check. Daily check of safety latch system is very important
– the discovery of device failure before
action could save your time and prevent you from great loss, injury or casualty.
·Before operation, judge whether the safety latches are engaged by sound.
·Check whether oil hose well connected and whether it leaks or not.
·Check the connections of chain and steel cable and check the power unit.
·Check whether plug bolts firmly screwed.
·Check if safety teeth and safety block matched well or not.
6.2 Weekly checking items
·Check the flexibility of moving parts.
·Check the working conditions of safety parts.
·Check the amount of oil left in the oil tank. Oil is enough if the carriage can be raised to highest position. Otherwise, oil is
insufficient.
·Check whether plug bolts firmly screwed.
6.3 Monthly checking items
·Check whether plug bolts firmly screwed.
·Check the tightness of the hydraulic system and screw firm the joints if it leaks.
·Check the lubrication and abrasion circumstance of axial pins, carriages, lifting arms and other related parts and replace in time
with new ones if they failed to work well.
·Check the lubrication and abrasion circumstance of steel cable.
6.4 Yearly checking items
·Empty the oil tank and check the quality of hydraulic oil.
·Wash and clean the oil filter.
users strictly follow the above maintenance requirements; the lift will keep in a good working condition and meanwhile
accidents could be avoided to a large extent.
Summary of Contents for JA4000FP
Page 18: ...18 7 Annex Annex1 Packing list of the whole lift Annex2 Overall diagram ...
Page 19: ...19 Annex3 Floor plan ...
Page 20: ...20 Annex 4 Steel cable connection ...
Page 21: ...21 ...
Page 22: ...22 ...
Page 24: ...24 ...
Page 25: ...25 ...