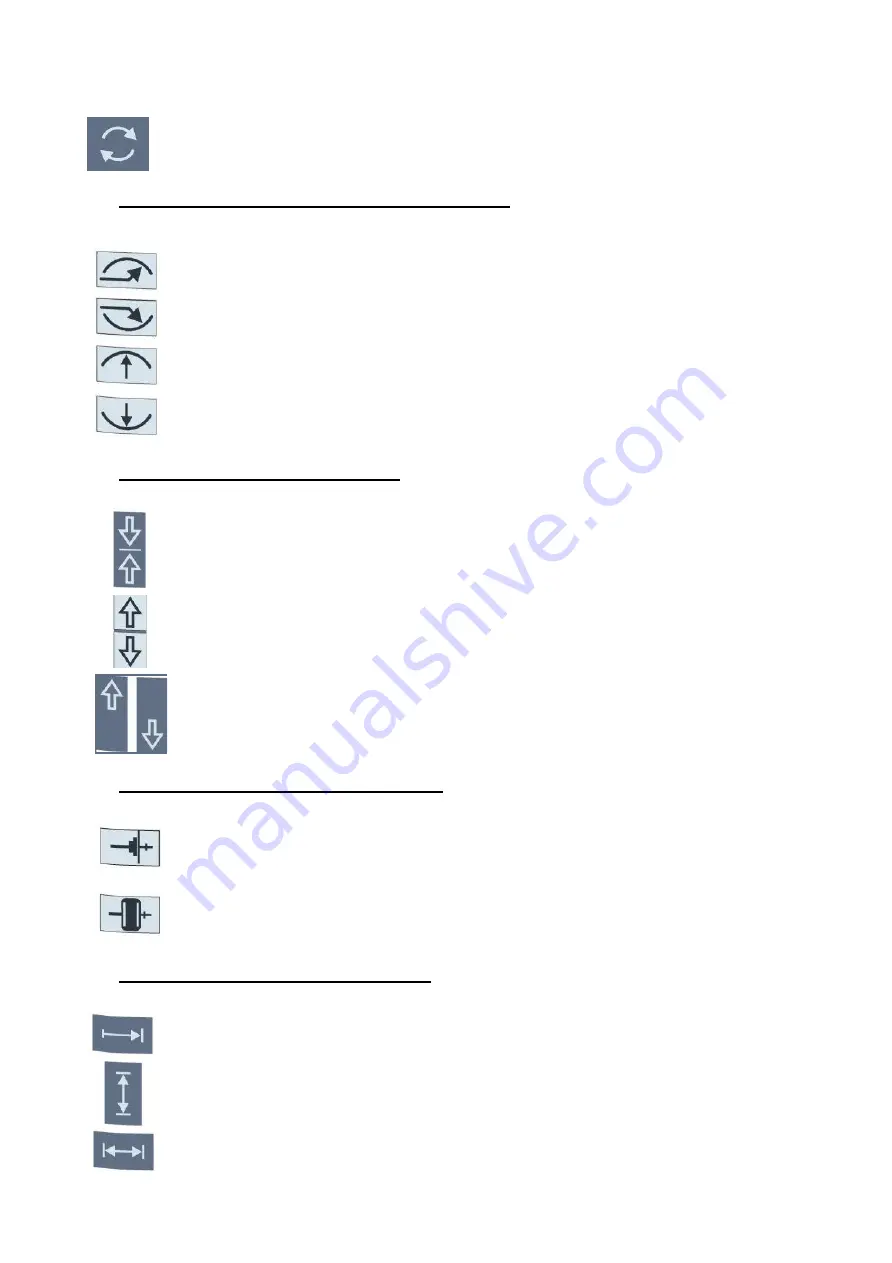
6.4
Other icons on the display
-
26
-
Wheel accelerating and a measurement
Icons presenting weight placement methods
Adhesive weight placement using mechanical adjuster (DWC-9-E)
Adhesive weight placement using laser adjuster (DWC-9-E)
/Hammered/Adhesive weight placement on
"12 o'clock"
Adhesive weight placement on
"6 o'clock"
Icons presenting wheel position
Wheel at the imbalance position
Wheel at the opposite position relative to the imbalance's position
Rotate the wheel according to the arrow's pointing direction
Icons presenting calibration method
Calibration using the device
Calibration using a wheel
Icons presenting wheel parameters
Distance
Diameter
Width