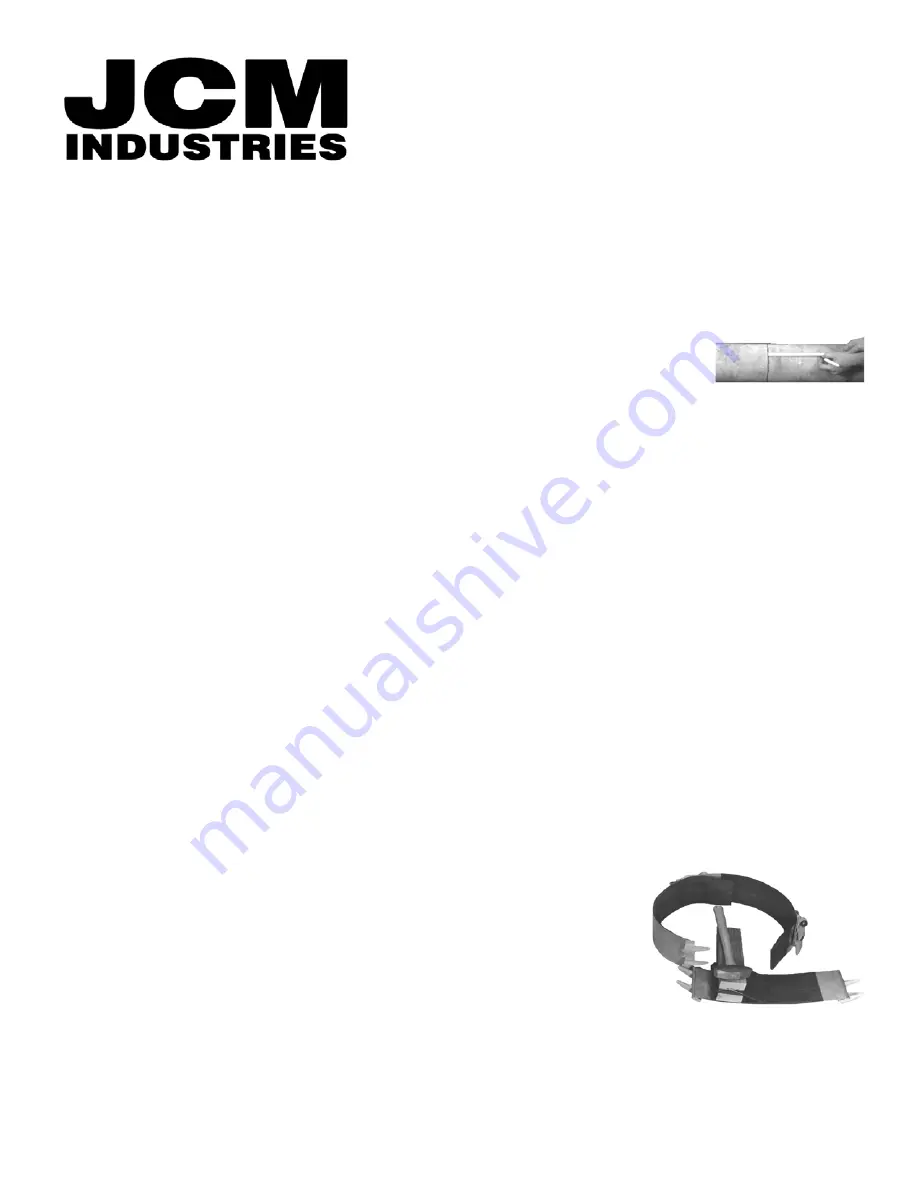
Years of field experience, special applications and product testing have revealed many subtleties regarding application and
installation of repair clamps. For maximum performance under adverse conditions take advantage of the JCM “Tricks of the
Trade.”
• Always clean and lubricate pipe with water or soapy water. This helps overcome friction when rotating the clamp to smooth the gasket.
Do not use oil base pipe lubricant; the oil does not disperse, leaves residue and prevents the gasket from sealing/adhering to the pipe
wall. Use water solvent lubricant. Use of a mirror will assist inspection of backside of pipe or pipe in cramped, limited space.
• Place a reference mark on the pipe back from the damaged area to help in centering clamp over break.
Clamps provide maximum performance when centered over damage area.
• For installation on pipe under pressure: lubricate the clamp gasket with soap/water mixture, assemble clamp
on the pipe beside the damaged area, lightly engage bolts and slid the clamp over the damaged area,
ensure tapered gasket lays flat without curl or fold, proceed with installation steps.
• Breaks involving deflected pipe require a wider clamp. JCM lugs will articulate, permitting clamp to better conform to pipe.
• Damage involving large holes or massive pitted areas - use stainless steel plate over large holes (under repair clamp) to provide the
gasket a surface to seal against.
• Drill holes in the ends of splits or cracks to relieve forces which could cause splits to continue.
• Clamp performance drops when gap between pipe ends is larger than 1/2”. Use a stainless steel spacer to fill or to place over gap.
• Leave sufficient pressure on a broken line to prevent intrusion of foreign matter to prevent excessive line contamination.
• With pressure reduced, spraying water will cease as soon as water level rises above break.
• Lubricating clamp bolts will ease clamp installation and assure proper torquing of bolts.
Making Larger Clamp From Smaller Clamps
Longer than normal gasket tapers permit joining of Universal Clamp Couplings of like width and type to make a larger
clamp. For instance, a 6” and 8” clamp can be joined to make a 14” clamp. This provides you with “on hand” capability to
make repairs on larger pipe sizes.
•
Determine which clamps are available to make needed clamp, usually 2 or 3 clamps
are sufficient. It is recommended that clamps to be joined be not more than one
nominal size apart. Join clamps with ranges that when combined include O.D. of
pipe to be repaired. For Example: Required clamp is 14” to fit 16.44 O.D. Combining
a 101-0905-12 (range 8.99 to 9.39) and a 101-0690-12 (range 6.84 to 7.25) will
make a clamp with a range of 15.84 to 16.64.
•
Prior to joining clamps, reduce the curvature of the recessed bridge plate (as shown
in photo) to slightly less than curvature of pipe to be repaired. This is done by laying
bridge plate between two 2” x 4”’s and hitting with a small sledge hammer.
•
Install as a multi-band clamp, making sure to tighten bolts evenly keeping gaps between lugs approximately even.
Tricks of the Trade for Installation
Models 101, 103, 102 and 104
Universal Clamp Couplings