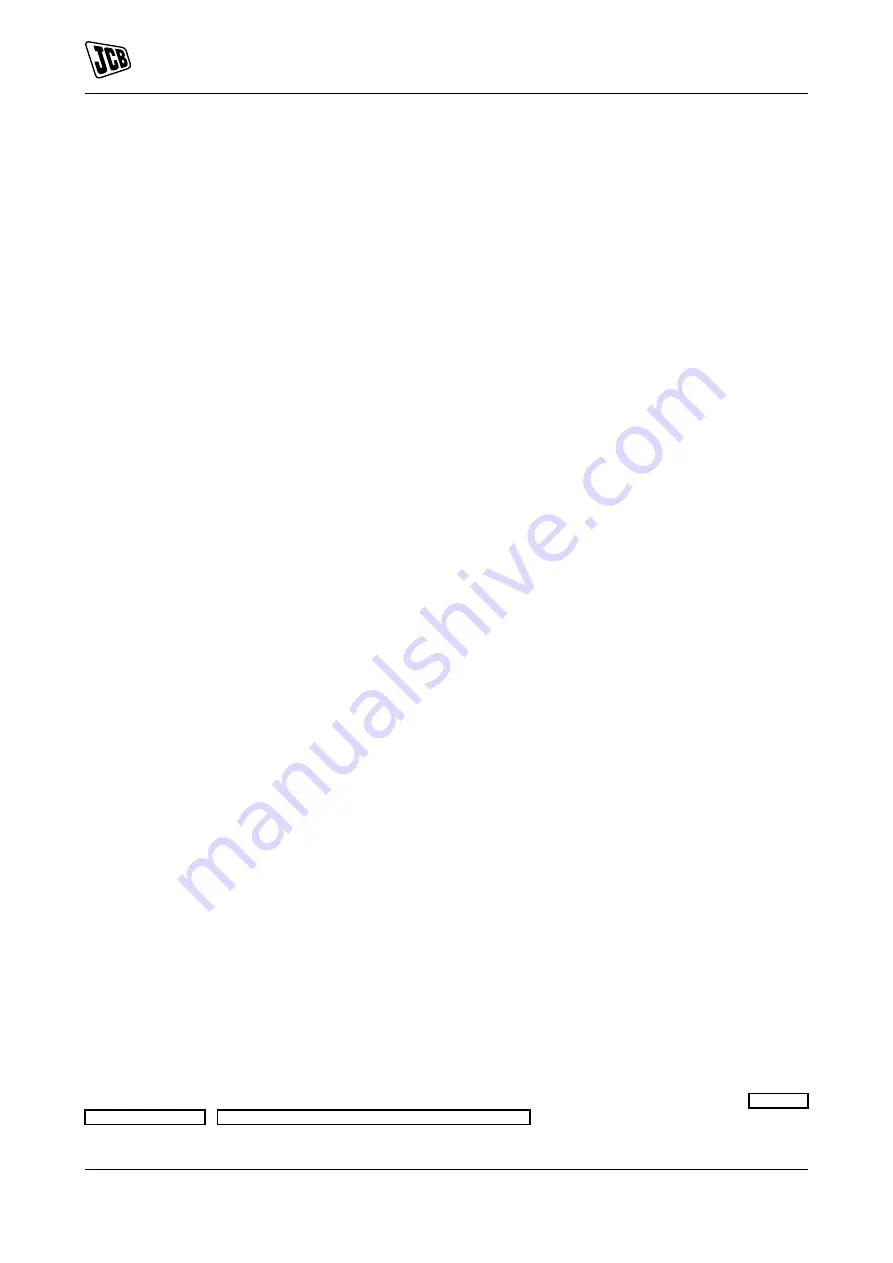
About the Product
Description
8
9831/7750-1
8
Description
General
The JCB Tandem roller machine is a self-propelled, vibratory tandem drum rollers which is powered by a 3
cylinder, diesel engine.
The machine is designed for compacting soil types ranging from stones to silty sand, or asphalt construction
materials when rolling over the subgrade in a forward or reverse direction (with or without vibration).
Four scrapers (two on each drum) are mounted on the machine and sprinkler bars are fitted to the front and
rear drums. The spray nozzles and the bar end caps are removable for easy cleaning.
The hydrostatic drive system allows for infinitely variable travel speeds. The drive motors (one motor mounted
on the left side of each drum) are connected in series on the CT160 and parallel on the CT260. The machines
is always driven with all drum drive. Each motor incorporates a spring on, pressure off brake system which
engages when the machine is in neutral. The drive motor hoses are protected inside steel frame plates.
A hydraulic system is also used to turn the machine front and rear vibratory shafts. Designed with an overturning
weight system on the vibratory shafts, the machine has selectable front drum, rear drum or both drums vibration.
The machine operates at a vibratory frequency of between 50 and 66 Hz and a nominal amplitude of 0.5 mm.
The machine has an articulated steering system giving a tight turning radius.
Intended Use
The machine is intended to be used in normal environmental conditions as described in this manual. Normally
the machine is designed only for compacting beds of earth or bituminous construction when running over the
subgrade in the forward or reverse direction, with or without vibration. These compacting material include soil
types ranging from stones to silty sand,and having water contents ranging from 40% to 110% of the optimum
water content. These figures are in accordance to the standard Proctor test DIN 18127.
Application also include road and pavement construction, sub-soil compaction and similar applications.
Soil of fine-grained or soils having higher water contents require a qualified trial compaction.
Use for which it is not intended includes, in particular:
•
It is not permissible to drive on a high gradient which is greater than the permissible gradient of the
machine. The permissible gradient is subgrade gradient .
•
Before driving on a gradient, it is still necessary to check, at the start of the gradient as seen in the
intended driving direction, whether there is adequate frictional engagement between the drums and the
roadway, i.e. whether, on the gradient, the machine can be driven uphill with medium acceleration and
can be braked downhill.
•
It is not permissible to drive on a gradient if the drums skid during braking.
•
Vibration at standstill.
•
Vibrating travel on blocks, rocks, concrete or frozen soil.
•
Vibrating travel in the vicinity of buildings if this could damage parts or installations; This should normally
be assumed for vibrational speeds of 8 mm/s or more at the endangered parts.
•
Earth-moving during forward driving with the pusher blade lowered.
•
Operation in extraordinary applications (see below) without additional safety measures.
•
Driving from above onto an untested gradient.
•
Driving on a subgrade having a gradient greater than the permissible gradient in a direction other than
the incline direction.
•
Use of the roller other than from the operator's seat.
The machine is intended to be used only on a subgrade gradient up to the permissible gradient.
Refer to: Performance Dimensions (Page 131).
Extraordinary applications are, in particular:
Summary of Contents for CT160
Page 2: ......
Page 4: ...9831 7750 1 Notes...
Page 16: ...Notes 6 9831 7750 1 6...
Page 25: ...About the Product Safety Labels 15 9831 7750 1 15 Figure 8 C F G E B A D...
Page 32: ...Notes 22 9831 7750 1 22...
Page 118: ...Maintenance Fuel System 108 9831 7750 1 108 Figure 62 B A A Bowl B Tap...
Page 138: ...Maintenance Electrical System 128 9831 7750 1 128 Figure 76 A B B A Panel B Screws...
Page 166: ...Notes 156 9831 7750 1 156...