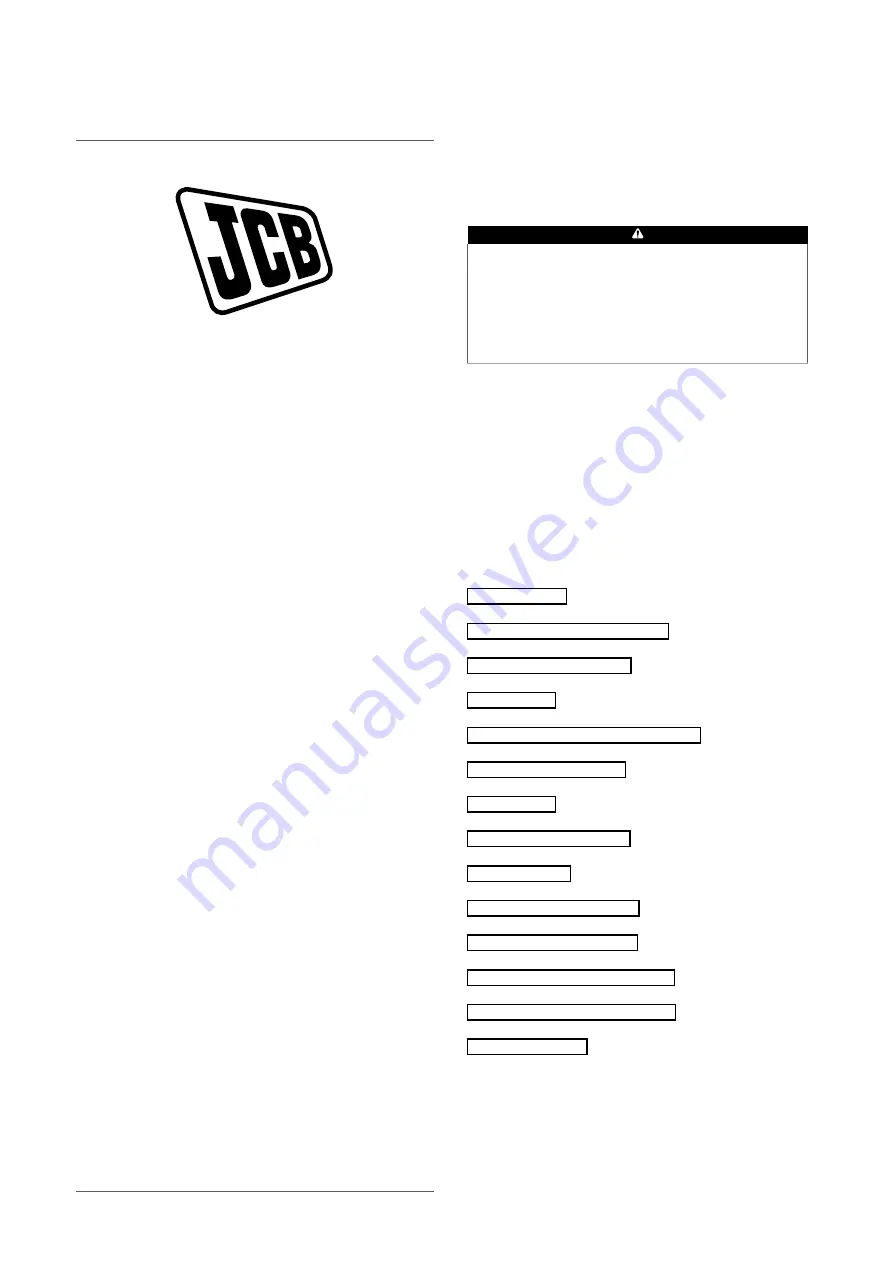
SERVICE MANUAL
6TFT, 6TST
EN - 9813/5300 - ISSUE 1 - 09/2015
This manual contains original instructions, verified by
the manufacturer (or their authorized representative).
Copyright 2015 © JCB SERVICE
All rights reserved. No part of this publication may
be reproduced, stored in a retrieval system, or
transmitted in any form or by any other means,
electronic, mechanical, photocopying or otherwise,
without prior permission from JCB SERVICE.
Foreword
The Operator's Manual
You and others can be killed or seriously injured
if you operate or maintain the machine without
first studying the Operator's Manual. You must
understand and follow the instructions in the
Operator's Manual. If you do not understand
anything, ask your employer or JCB dealer to
explain it.
Do not operate the machine without an Operator's
Manual, or if there is anything on the machine you
do not understand.
Treat the Operator's Manual as part of the machine.
Keep it clean and in good condition. Replace the
Operator's Manual immediately if it is lost, damaged
or becomes unreadable.
Contents
Summary of Contents for 6TFT
Page 2: ...9813 5300 1 Notes Find manuals at https best manuals com...
Page 4: ...Notes 9813 5300 1 Find manuals at https best manuals com...
Page 8: ...Notes 01 2 9813 5300 1 01 2 Find manuals at https best manuals com...
Page 22: ...Notes 01 16 9813 5300 1 01 16...
Page 26: ...Notes 06 2 9813 5300 1 06 2...
Page 30: ...Notes 06 6 9813 5300 1 06 6...
Page 46: ...Notes 06 22 9813 5300 1 06 22...
Page 51: ...This as a preview PDF file from best manuals com Download full PDF manual at best manuals com...