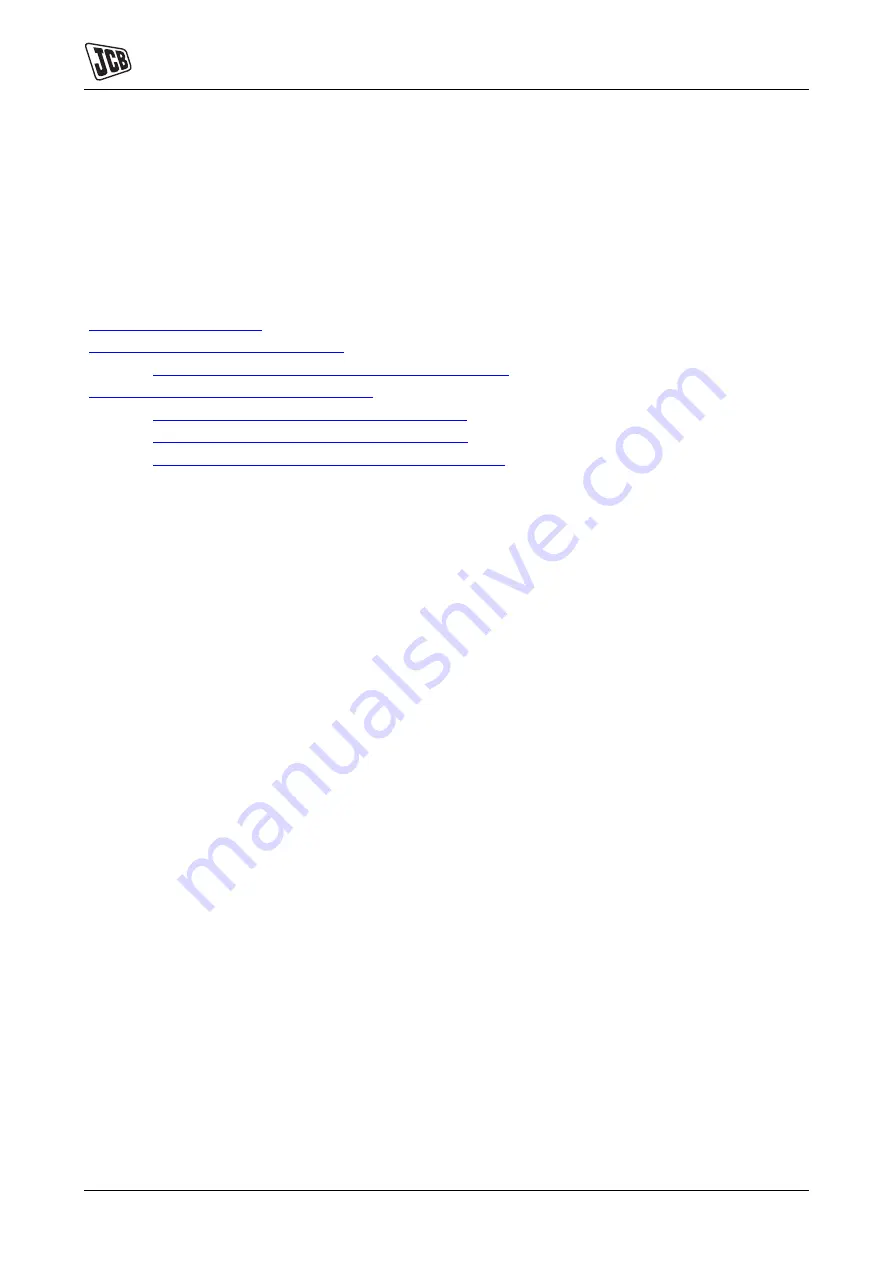
Section 1-3 - General Information
1-3-1
1-3-1
9803/3750-05 (1-02-01)
Machine Identification
Introduction
This topic contains information about a machine identification. On the machine and on the machine devices there are
identification data plates.
Machine Identification Plate (
Typical Product Identification Number (PIN) (
Component Identification Plates (
Typical Engine Identification Number (
Transmission Identification Numbers (
Summary of Contents for 540-170
Page 2: ...Section 0 Service Manual 0 0 0 0 9803 3750 05 Notes ProCarManuals com...
Page 4: ...Section 1 General Information 1 0 1 0 9803 3750 05 Notes ProCarManuals com...
Page 6: ...Page No Contents Section 1 General Information 1 ii 1 ii ProCarManuals com...
Page 84: ...Section 2 Care and Safety 2 0 2 0 9803 3750 05 Notes ProCarManuals com...
Page 121: ...Section 3 Routine Maintenance 3 0 3 0 9803 3750 05 Notes ProCarManuals com...