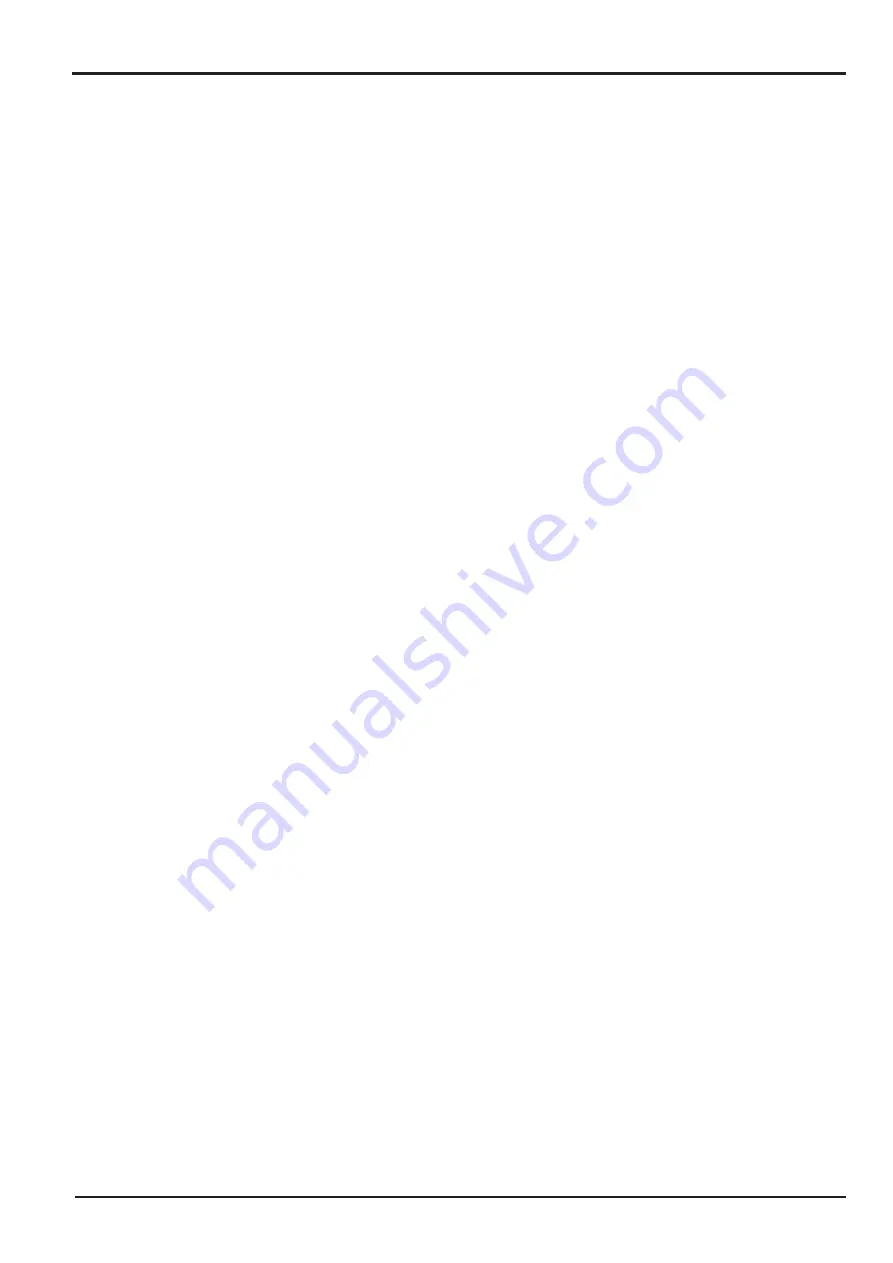
5 - 4
Removal and Replacement
from machine no. 807226
Slew Cylinder - Removal
Position the machine on firm level ground, rest the front
shovel on the ground and position the excavator bucket just
above the ground. Stop the engine. Operate the excavator
controls to vent residual hydraulic pressure.
Release the hydraulic connections to the slew cylinders.
Unscrew and remove capscrews 1 from each slew cylinder 2.
Position an oil tray underneath the kingpost and remove plug
C to drain the oil from the slew gearbox.
Withdraw the cylinders by manually swinging the excavator
assembly to one side and then the other. This will push off
each cylinder in turn.
Remove rack seals 3 as each side of the rack 4 is exposed.
Kingpost - Removal
If required, remove the boom and dipper (see pages B/3-1
and B/4-1).
Note: Unless the kingpost is to be renewed, it is not
necessary to remove the boom and dipper to release the
kingpost from the machine.
!
!
WARNING
Hydraulic Pressure
Hydraulic fluid at system pressure can injure you. Before
disconnecting or connecting hydraulic hoses or
couplings, vent the pressure trapped in the hoses in
accordance with the instructions given in this
publication.
HYD 1-5
At the kingpost, disconnect and plug the hydraulic hoses,
marking the hoses to ensure correct reconnection (see page
E/2-1).
Position an oil tray underneath the kingpost and remove plug
C to drain the oil from the slew gearbox. Remove capscrews
5 and lift off the thrust cap 6 complete with vent tube
assembly 7.
Slacken and remove the pinion capscrews 8.
Support the backhoe by placing a sling from a crane around
the boom ram to kingpost pivot. (If the boom and dipper
have been removed, place the sling around the kingpost.)
Remove locking bolt 9 and kingpost pivot pin 10.
Using the crane, lift the excavator assembly up which will
free the pinion from the carriage base then pull the assembly
back away from the carriage, taking care to collect shim 11.
Remove pinion 12 and thrust washer 13 from the kingpost.
Remove the anti-rotation pin 14 and withdraw the rack 4.
Note: From machine no. 808254 (or possibly slightly before)
flanged bush 16a is fitted in place of bush 16. The flanged
bush cannot be fitted to later machines unless a new later
kingpost is also fitted.
If bushes 17 or 18 are to be renewed, first unscrew the
retaining screw D. Remove the bushes using a suitable
press.
Kingpost - Replacement
Repacement is a reversal of the removal procedure.
If bush 16 is to be renewed, coat outside diameter with JCB
Multi-Gasket before pressing into position.
Lubricate the pinion and rack with gear oil before assembly.
Apply JCB Special MPL grease to pivot pin 10.
Clean threads of capscrews 8 and apply JCB Threadlocker
and Sealer. Tighten to correct torque.
Note: From machine no. 808254, special lock washers are
used with capscrews 8. These can be fitted to earlier
machines if required.
After replacement, refill the slew housing with the appropriate
grade of oil (see page 3/6-1 for correct procedure).
Slew Cylinder - Replacement
Fit new seals 3 to rack 4. Ensure that plungers A move freely
in their bores without sticking.
Assemble cylinders 2 using new ‘O’ ring 15. Reconnect
hydraulic pipework.
After replacement, refill the slew housing with the appropriate
grade of oil (see page 3/6-1 for correct procedure).
When assembly is complete, operate excavator services fully
to bleed the hydraulic system then check the hydraulic level.
Torque Settings
Item
Nm
kgf m
lbf ft
1
300
30.6
221
5
159
16.2
117
8
395
40.3
291
Section B
9803/8550
Section B
5 - 4
Issue 2*
Kingpost Assembly
*
*
Summary of Contents for 1CX
Page 2: ...www WorkshopManuals co uk Purchased from www WorkshopManuals co uk...
Page 6: ...www WorkshopManuals co uk Purchased from www WorkshopManuals co uk...
Page 18: ...www WorkshopManuals co uk Purchased from www WorkshopManuals co uk...
Page 26: ...www WorkshopManuals co uk Purchased from www WorkshopManuals co uk...
Page 30: ...www WorkshopManuals co uk Purchased from www WorkshopManuals co uk...
Page 44: ...www WorkshopManuals co uk Purchased from www WorkshopManuals co uk...
Page 58: ...www WorkshopManuals co uk Purchased from www WorkshopManuals co uk...
Page 70: ...www WorkshopManuals co uk Purchased from www WorkshopManuals co uk...
Page 80: ...www WorkshopManuals co uk Purchased from www WorkshopManuals co uk...
Page 106: ...www WorkshopManuals co uk Purchased from www WorkshopManuals co uk...
Page 110: ...www WorkshopManuals co uk Purchased from www WorkshopManuals co uk...
Page 114: ...www WorkshopManuals co uk Purchased from www WorkshopManuals co uk...
Page 122: ...www WorkshopManuals co uk Purchased from www WorkshopManuals co uk...
Page 165: ...www WorkshopManuals co uk Purchased from www WorkshopManuals co uk...
Page 194: ...www WorkshopManuals co uk Purchased from www WorkshopManuals co uk...
Page 196: ...www WorkshopManuals co uk Purchased from www WorkshopManuals co uk...
Page 199: ...www WorkshopManuals co uk Purchased from www WorkshopManuals co uk...
Page 220: ...www WorkshopManuals co uk Purchased from www WorkshopManuals co uk...
Page 222: ...www WorkshopManuals co uk Purchased from www WorkshopManuals co uk...
Page 227: ...www WorkshopManuals co uk Purchased from www WorkshopManuals co uk...
Page 230: ...www WorkshopManuals co uk Purchased from www WorkshopManuals co uk...
Page 234: ...www WorkshopManuals co uk Purchased from www WorkshopManuals co uk...
Page 239: ...www WorkshopManuals co uk Purchased from www WorkshopManuals co uk...
Page 242: ...www WorkshopManuals co uk Purchased from www WorkshopManuals co uk...