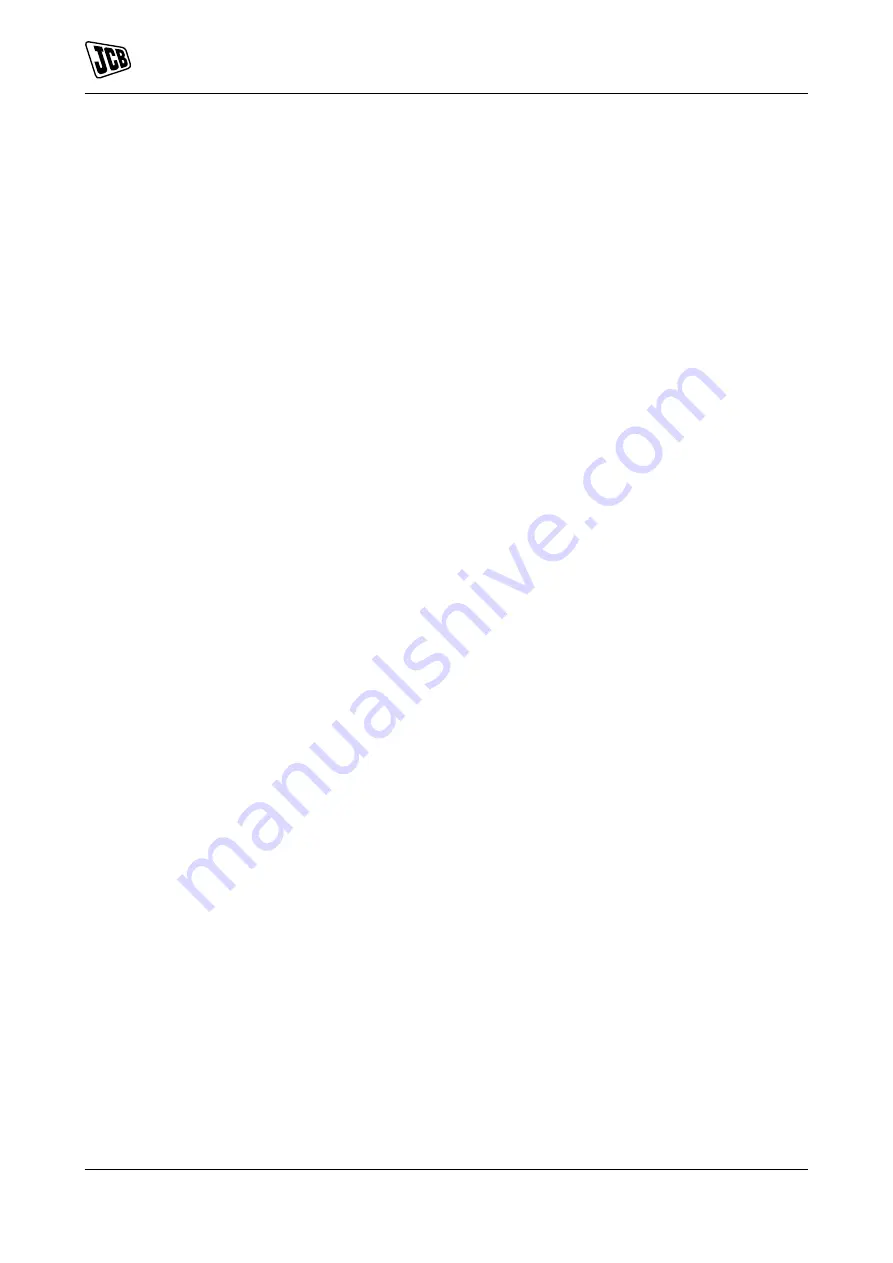
01 - Machine
03 - Safety
12 - Maintenance Safety
01 - 6
9813/6750-1
01 - 6
12 - Maintenance Safety
Introduction
Raised Machine
Never position yourself or any part of your body
under a raised machine which is not correctly
supported. If the machine moves unexpectedly you
could become trapped and suffer serious injury or be
killed.
Air Conditioning Maintenance
The air conditioning system is a closed loop system
and contains pressurised refrigerant. No part of the
system should be disconnected until the system
has been discharged by a refrigeration engineer
or a suitably trained person. You can be severely
frostbitten or injured by escaping refrigerant.
Compressed Air
Compressed air is dangerous. Wear personal
protective equipment. Never point a compressed air
jet at yourself or others.
Springs
Always wear personal protective equipment when
dismantling assemblies containing components
under pressure from springs. This will protect against
eye injury from components accidentally flying out.
Metal Splinters
You can be injured by flying metal splinters when
driving metal pins in or out. Use a soft faced hammer
or copper drift to remove and install metal pins.
Always wear personal protective equipment.
Communications
Bad communications can cause accidents. If two
or more people are working on the machine, make
sure each is aware of what the others are doing.
Before starting the engine make sure the others are
clear of the danger areas. Examples of danger areas
are: the rotating blades and belt on the engine, the
attachments and linkages, and anywhere beneath or
behind the machine. People can be killed or injured
if these precautions are not taken.
Repairs
If your machine does not function correctly in
any way, get it repaired straight away. Neglect of
necessary repairs could result in an accident or affect
your health. Do not try to do repairs or any other
type of maintenance work you do not understand. To
avoid injury and/or damage get the work done by a
specialist engineer.
Hydraulic Pressure
Hydraulic fluid at system pressure can injure you.
Before connecting or removing any hydraulic hose,
residual hydraulic pressure trapped in the service
hose line must be vented. Make sure the hose
service line has been vented before connecting or
removing hoses. Make sure the engine cannot be
started while the hoses are open.
'O' rings, Seals and Gaskets
Badly installed, damaged or rotted 'O' rings, seals
and gaskets can cause leakages and possible
accidents. Renew whenever disturbed unless
otherwise instructed. Do not use Triochloroethane or
paint thinners near 'O' rings and seals.
Arc Welding
To prevent the possibility of damage to electronic
components, disconnect the battery and the
alternator before arc-welding on the machine or
attached implements.
If the machine is equipped with sensitive electrical
equipment, i.e. amplifier drivers, electronic control
units (ECUs), monitor displays, etc., then disconnect
them before welding. Failure to disconnect the
sensitive electrical equipment could result in
irreparable damage to these components.
Parts of the machine are made from cast iron, welds
on cast iron can weaken the structure and break. Do
not weld cast iron. Do not connect the welder cable
or apply any weld to any part of the engine.
Always connect the welder earth (ground) cable to
the same component that is being welded to avoid
damage to pivot pins, bearings and bushes. Attach
the welder earth (ground) cable a distance from the
part being welded no more than 0.6m.
Counterweights
Your machine may be installed with counterweights.
They are extremely heavy. Do not attempt to remove
them.
Accumulators
The accumulators contain hydraulic fluid and gas at
high pressure. Prior to any work being carried out
on systems incorporating accumulators, the system
pressure must be discharged by a JCB dealer, as
the sudden release of the hydraulic fluid or gas may
cause injury.
Hot Components
Touching hot surfaces can burn skin. The engine and
machine components will be hot after the unit has
been running. Allow the engine and components to
cool before servicing the unit.
Soft Ground
A machine can sink into soft ground. Never work
under a machine on soft ground.
Summary of Contents for 135
Page 2: ...9813 6750 1 Notes Find manuals at https best manuals com ...
Page 4: ...Notes 9813 6750 1 Find manuals at https best manuals com ...
Page 8: ...Notes 01 2 9813 6750 1 01 2 Find manuals at https best manuals com ...
Page 32: ...Notes 01 26 9813 6750 1 01 26 ...
Page 36: ...Notes 9813 6750 1 2016 03 21 ...
Page 38: ...Notes 03 2 9813 6750 1 03 2 ...
Page 42: ...Notes 03 6 9813 6750 1 03 6 ...
Page 51: ...This as a preview PDF file from best manuals com Download full PDF manual at best manuals com ...