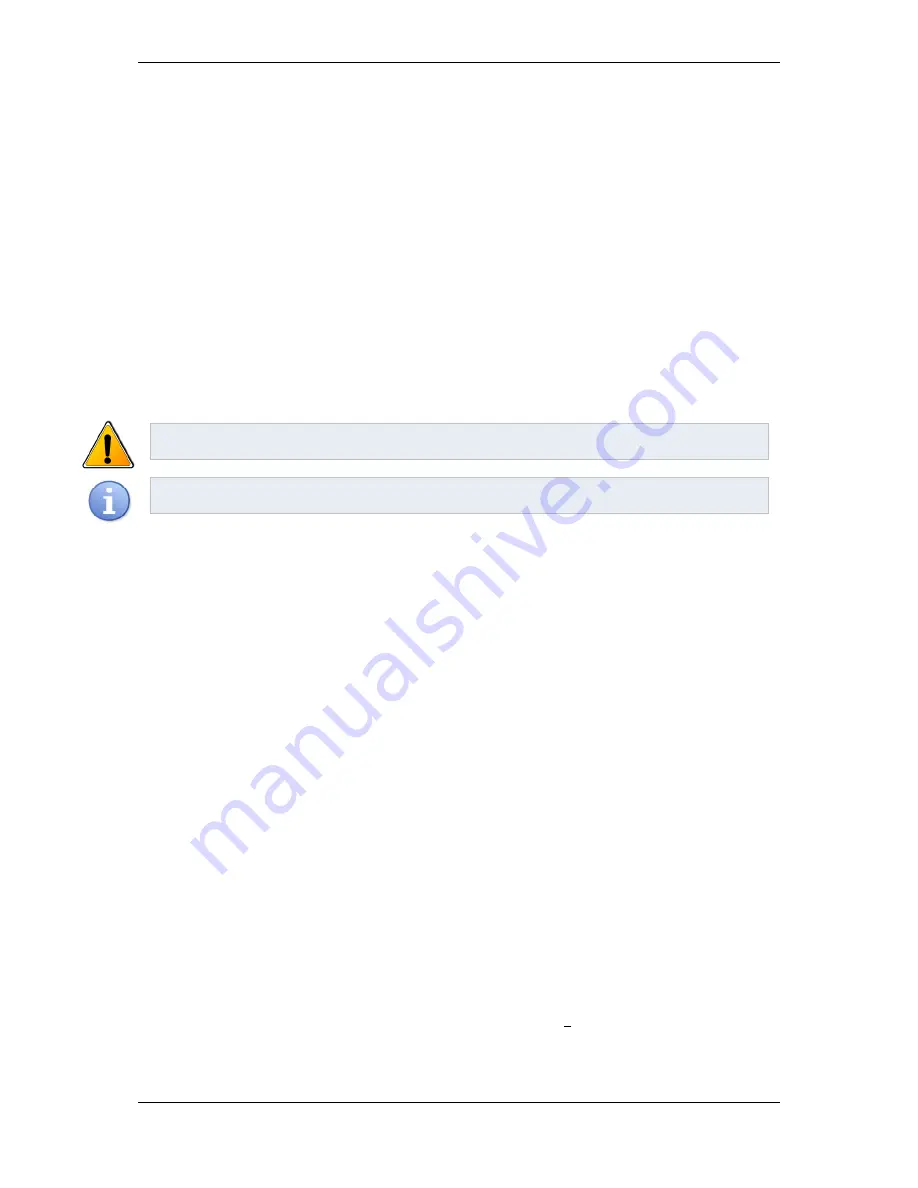
LinX Series Linear Motor - User Guide
12
D-000168 Rev 02
ANCA Motion
The brake must be chosen so that it provides enough force to resist gravity, inertia and machine operation. The
kinetic energy of the moving load will be converted into heat due to friction when the brake is applied. The
amount of kinetic energy must be taken into account to prevent damage to the brake due to overheating.
Vertical Applications
4.2.5
If the LinX cylindrical motor is used in a vertical application, it is recommended to use a counter-balance. The
counter balance should be designed to balance the gravitational forces on the system such that the motor is
stationary when there is no force applied by the motor.
If a counter-balance is not used, the linear motor must constantly produce a force directly opposing gravity. This
will add to the application’s continuous force requirements and, therefore, impact the motor model selection. A
brake is recommended for most applications but must be used to prevent damage in applications where the load
will drop immediately after power is removed.
Support and Bearings
4.3
Shaft
4.3.1
WARNING:
Failure to install the shaft to these requirements could result in damage to machinery and
property as well as severe injury or death.
NOTE:
Shaft deflection must be limited to ensure that the there is no contact with the forcer at any point
over the entire stroke.
The shaft must be mounted with supports at its ends to restrict longitudinal movement and maintain concentricity
with the forcer’s bore. The shaft must not be drilled. The shaft supports need to be able to support the mass of
the shaft and the forces generated by the motor. The supports must clamp the shaft for a length of at least 50mm
with a minimum clamping force of 8kN at each end. A higher clamping force may be required if using low friction
materials, please contact ANCA Motion for more information.
The shaft support can be designed into the structure of the machine or typical shaft hangers can be used. In
either situation, the following points must be taken into consideration.
It is recommended that supports are made of non-magnetic materials to prevent attractive forces being
applied towards the end of stroke.
There should be capability to adjust the shaft position to allow for fine tuning the alignment of the shaft
to the forcer.
It is recommended that the shaft supports are designed for an axial shaft load of twice the peak motor
force.
Design of the shaft supports should cater for any additional application specific load cases such as
vibration or high frequency load cycling.
Integrated soft bump stops are recommended to stop the motor directly contacting the shaft supports
which may cause damage.
Ensure that the shaft supports are properly earthed to the chassis of the machine.
As with any fixed beam, a long shaft will result in vertical displacement at its centre point. This is often referred to
as sag. This displacement distance should be compensated for to ensure to maximise the clearance between the
shaft and forcer.
The recommended method to compensate for shaft sag is to lift the supports relative to the forcer such that the
centreline of the forcer bore matches the average centre line of the shaft. Figure 4-4 demonstrates this method,
the centreline of the shaft supports is given by the centre line of the forcer bore,
,
and the shaft midpoint vertical
displacement,
:
By lifting the shaft centre line by half the vertical displacement, a longer stroke can be achieved without additional
support systems.