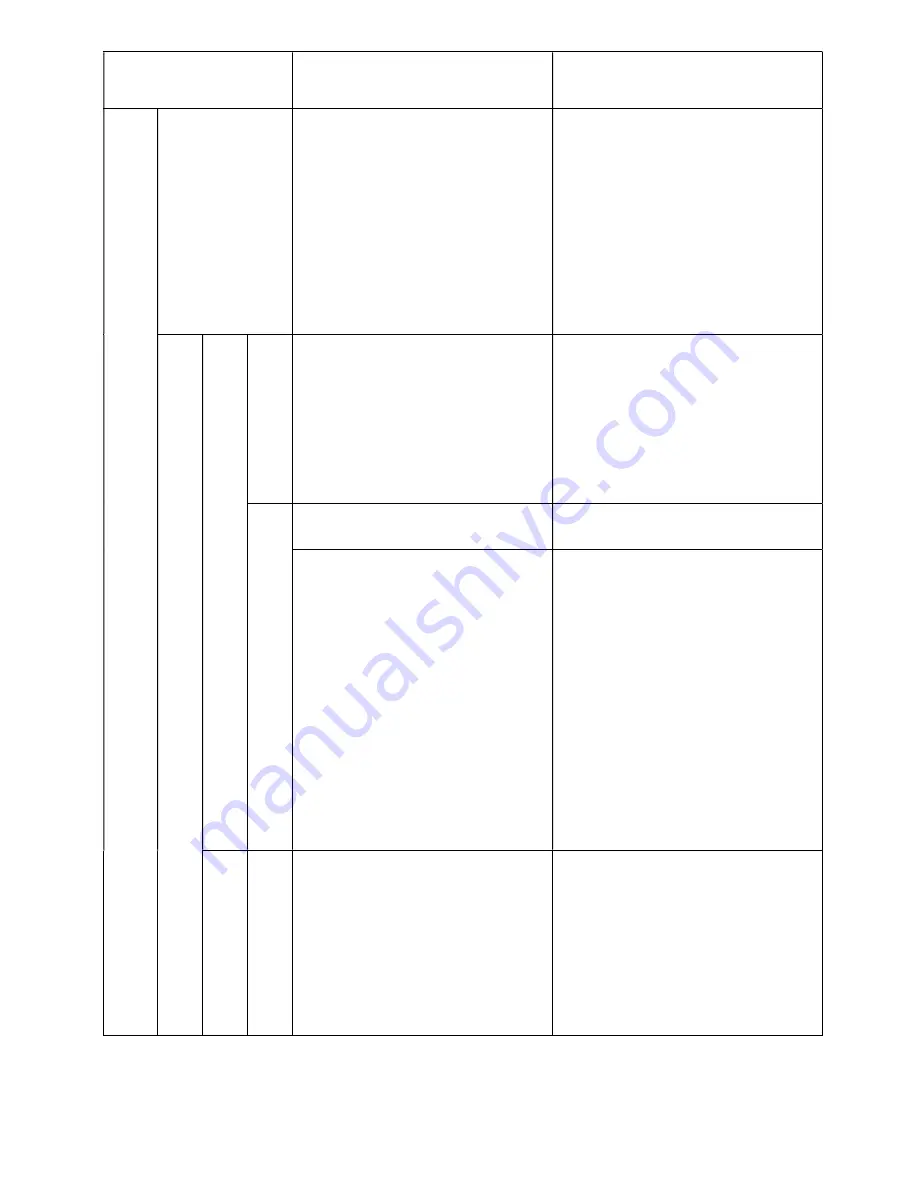
62
Trouble
Location
Remedy
E
n
gi
n
e
w
il
l
n
o
t
fi
re
–
E
n
gi
n
e
h
a
s
st
o
p
p
ed
C
ar
b
u
re
tt
er
c
a
n
n
o
t
b
e
fl
o
od
ed
Empty fuel tank.
Fuel tap off.
Fuel filter above the-tap
clogged.
Chocked fuel pipe or screen in
carburetter.
Clogged filler cap vent on the
fuel tank.
Transfer fuel reserve and re-
fuel at the earliest convenience.
Turn fuel tap on.
Unscrew the fuel tap and clean
the filter.
Remove and blow the fuel
pipe, remove and clean the
carburetter.
Clean filler cap vent.
C
ar
b
u
re
tt
er
c
a
n
b
e
fl
oo
d
ed
Ir
re
gu
la
r
sp
a
rk
in
g
S
p
a
rk
a
t
le
a
d
e
n
d
Oiled sparking plug.
Damaged plug insulation.
Short circuiting between
sparking plug points.
Plug points gap too wide.
Remove and clean sparking
plug.
Replace plug.
Clean sparking plug.
Adjust sparking plug gap to
0.45 mm. (0.018 in.)
N
o
sp
a
rk
a
t
le
a
d
e
n
d
Ignition key not inserted.
Insert the key.
Dirty breaker points.
Faulty breaker points.
H. T. lead broken or loosed.
Burnt lead insulation.
Faulty condenser. .
Damaged stator winding
insulation.
Water in contact breaker.
Clean the point
using a cloth
soaked in petrol.
Have point replaced.
Tape insulation crack,
replace lead at the earliest
convenience.
Tape lead and replace at the
earliest convenience.
Replace condenser.
Refer to a specialist workshop.
Blow out water. wipe off
carefully, allow to dry.
R
eg
u
la
r
sp
a
rk
in
g
C
om
p
re
ss
io
n
p
o
or
Broken piston ring.
Jammed piston ring.
Sparking plug washer leaks.
Replace ring.
Remove, clean and replace
ring.
Replace washer.
Summary of Contents for 353/04
Page 2: ...2 ...
Page 3: ...3 ...
Page 4: ...4 ...
Page 8: ...8 Fig 2 Engine 250 c c sectional view ...
Page 9: ...9 Fig 3 Plan of the Motorcycle ...
Page 16: ...16 ...
Page 29: ...29 Fig 13 Removing the chain connecting link Fig 14 Adjusting the brake ...
Page 47: ...47 Fig 28 Rear wheel sectional view ...
Page 48: ...48 Fig 29 Front wheel sectional view ...
Page 52: ...52 ...
Page 64: ...64 Fig 42 Two stroke engine operation diagram ...